Our 26th Annual Conference in San Diego, California was the biggest and best we've ever held, with an incredible lineup of speakers and record breaking attendance. Thank you to all who made it out, and to those of you who didn't, we hope to see you this spring in Miami!
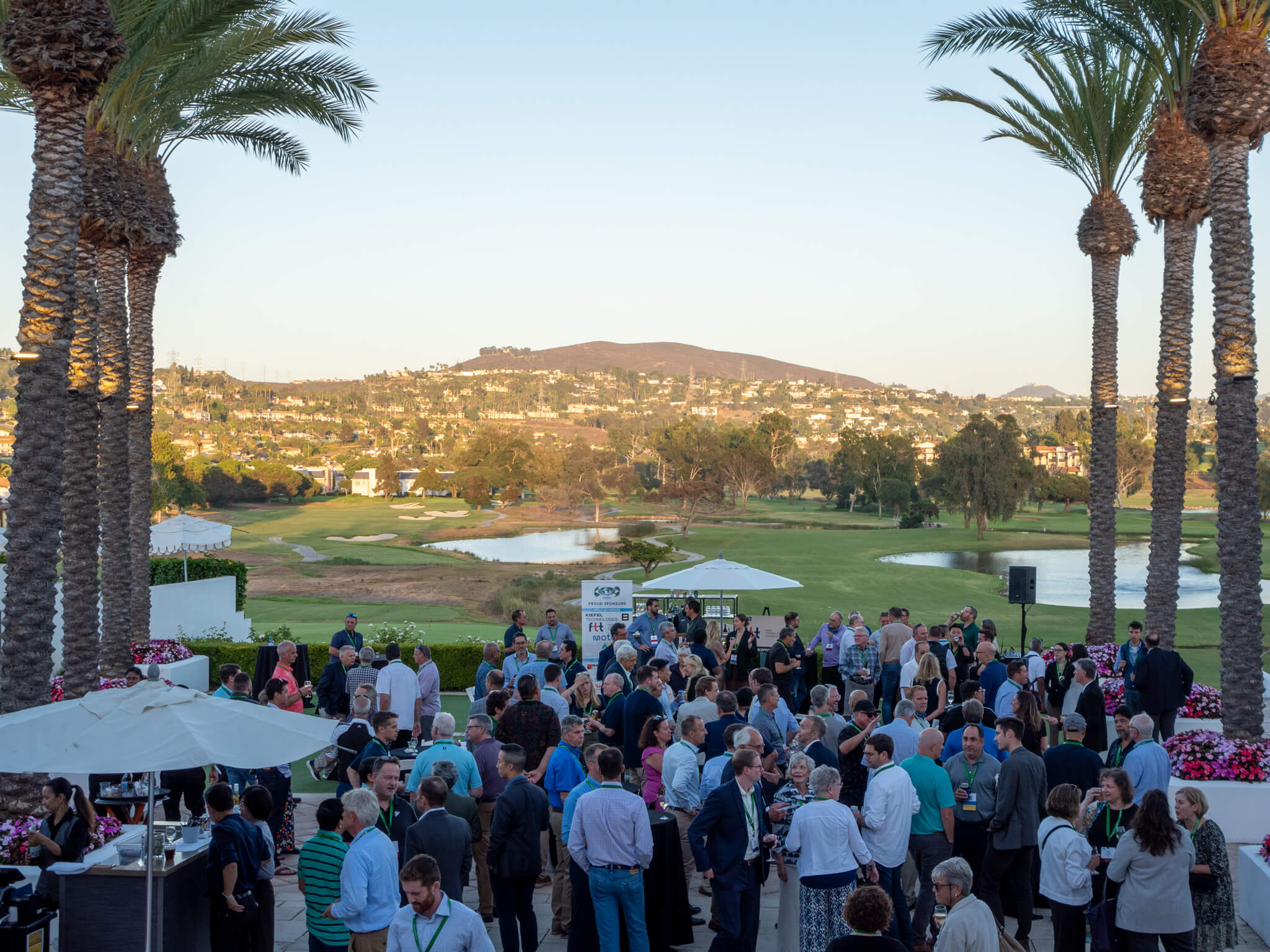
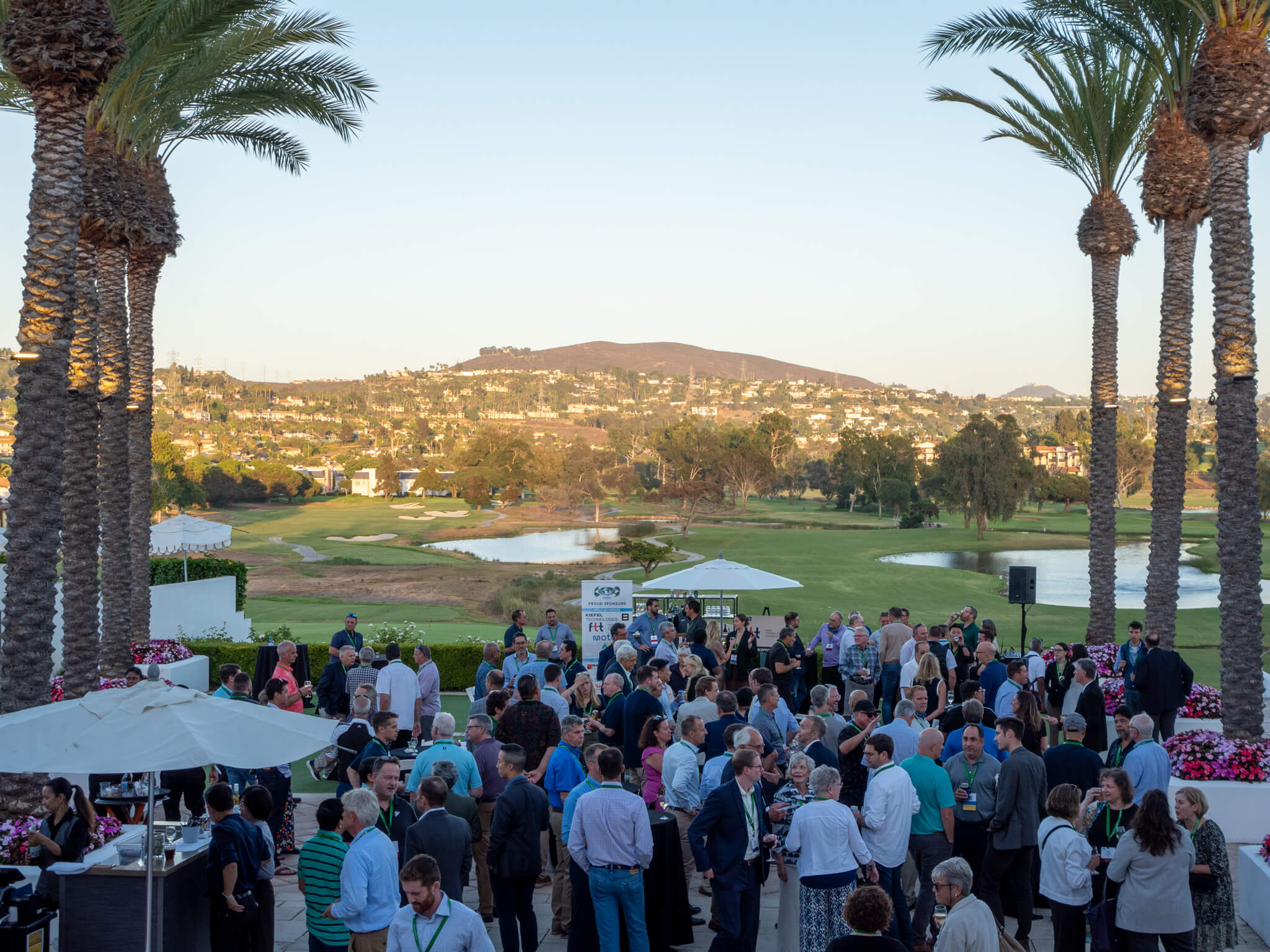
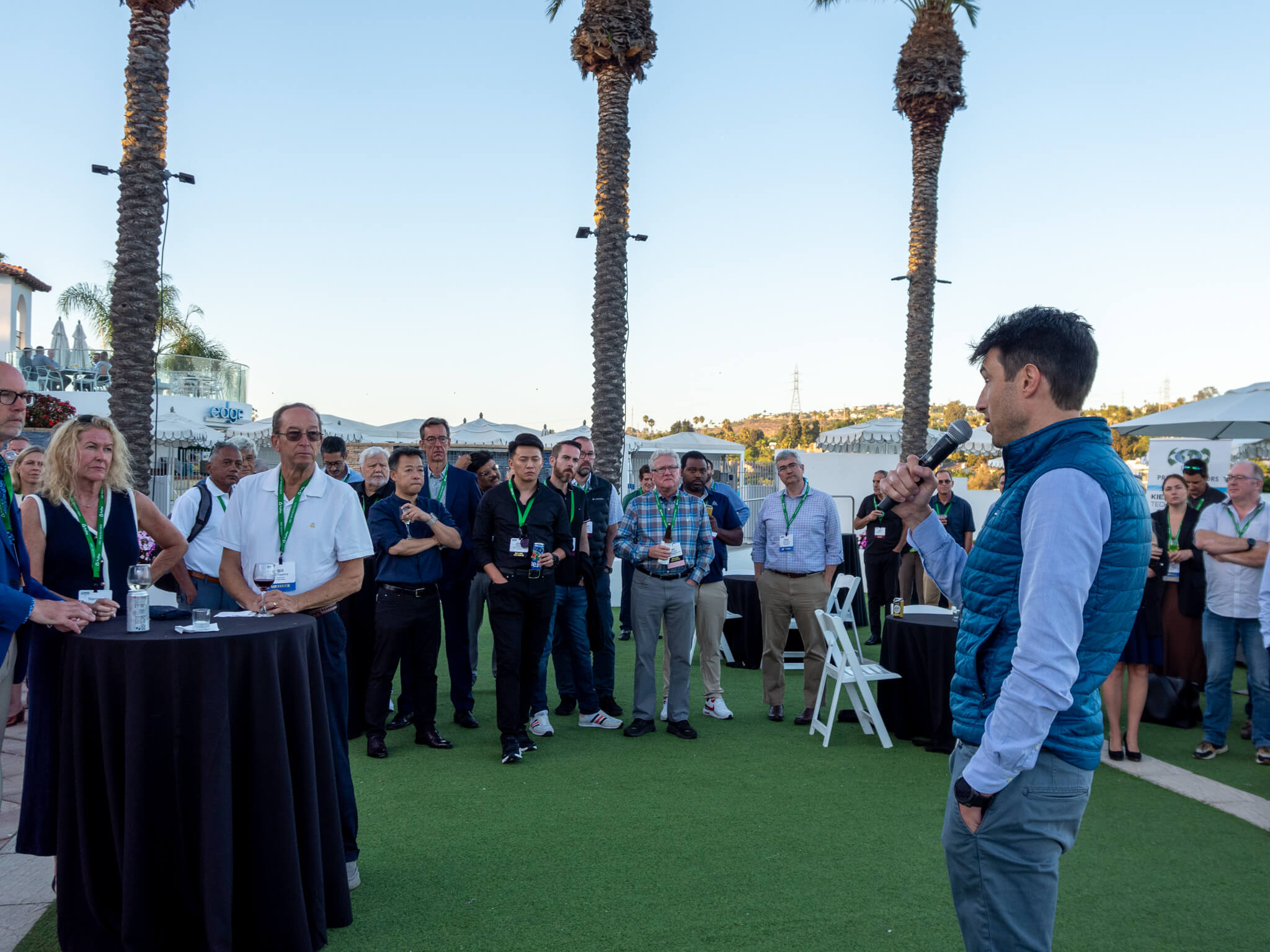
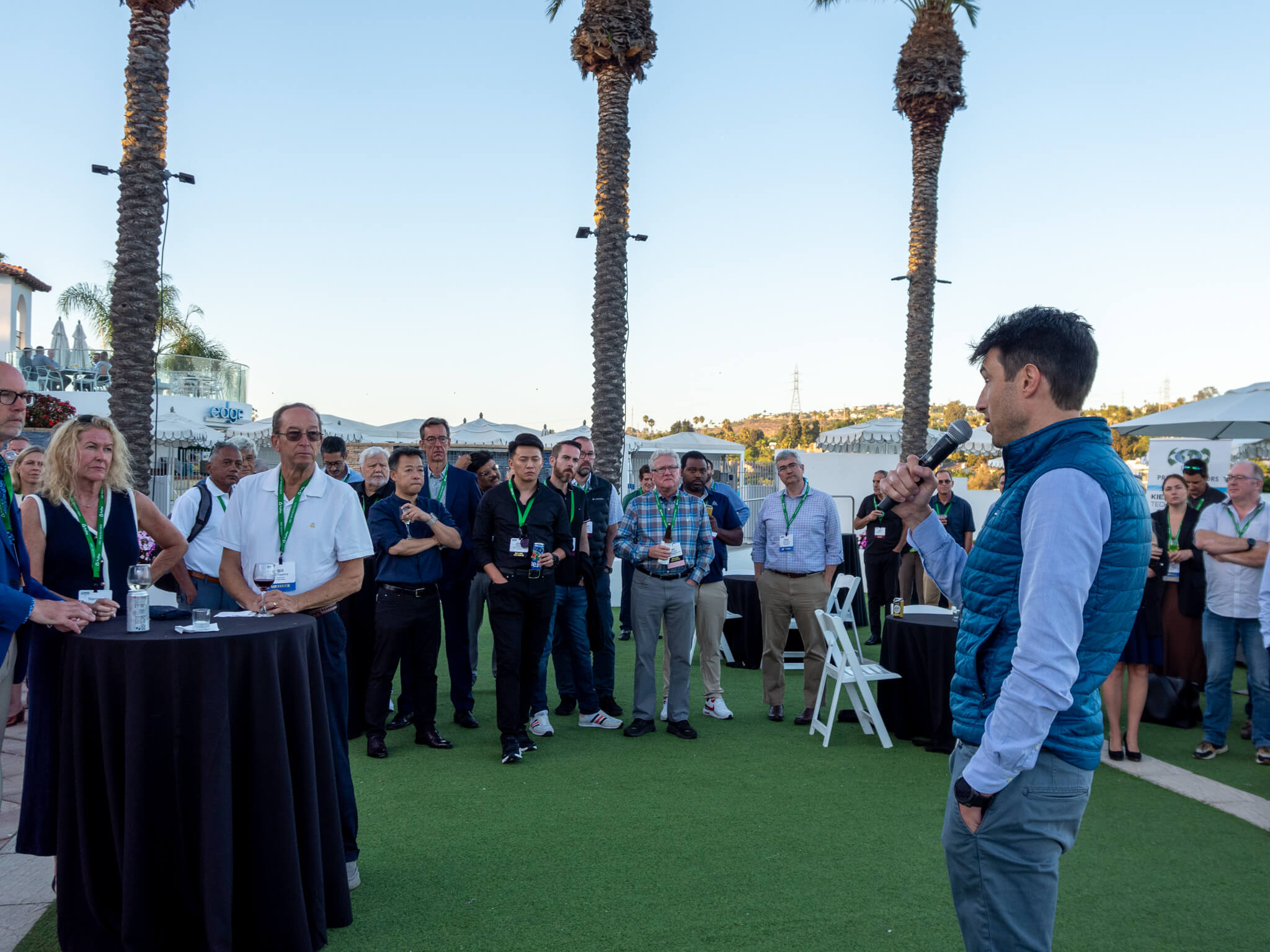
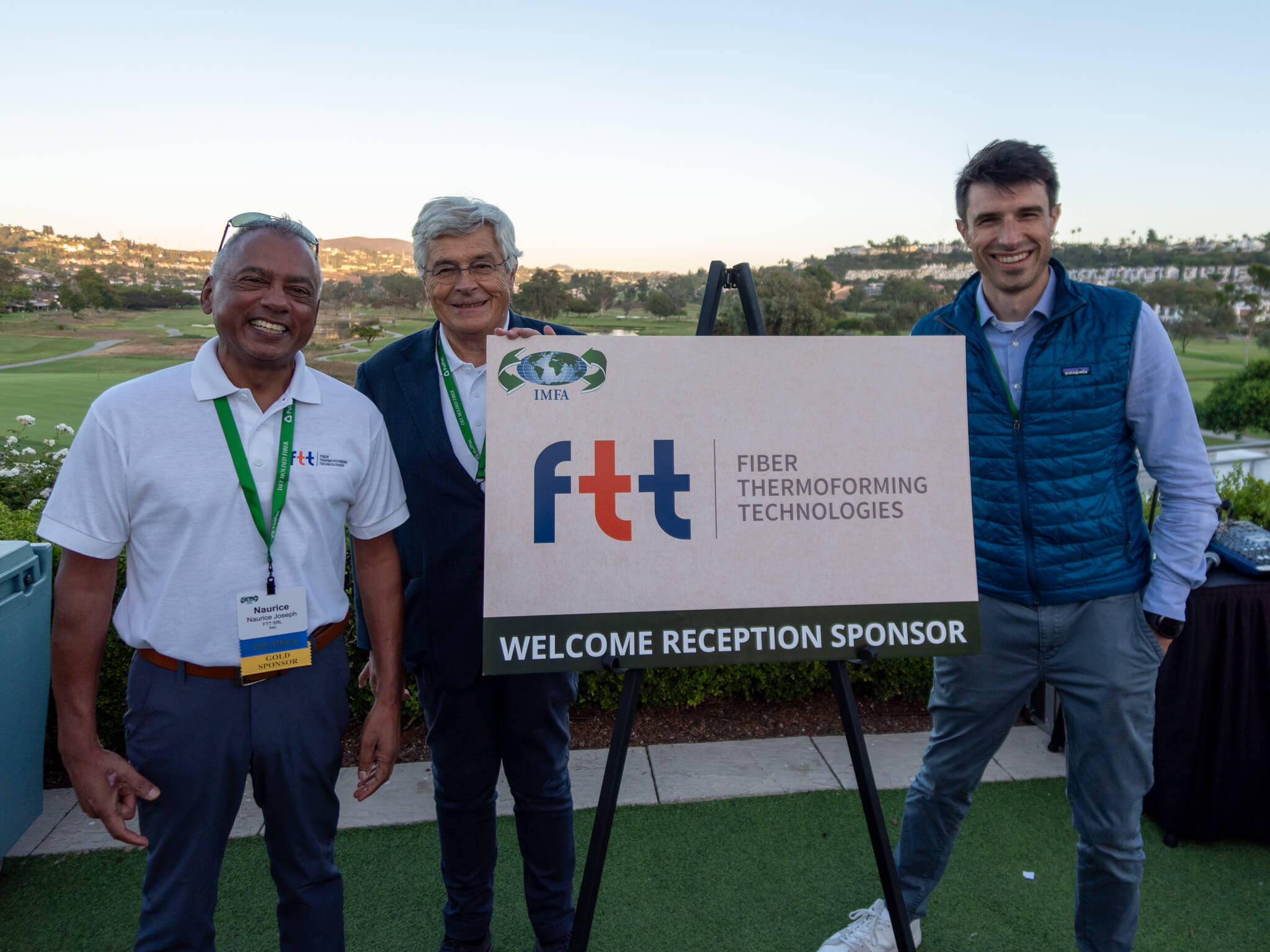
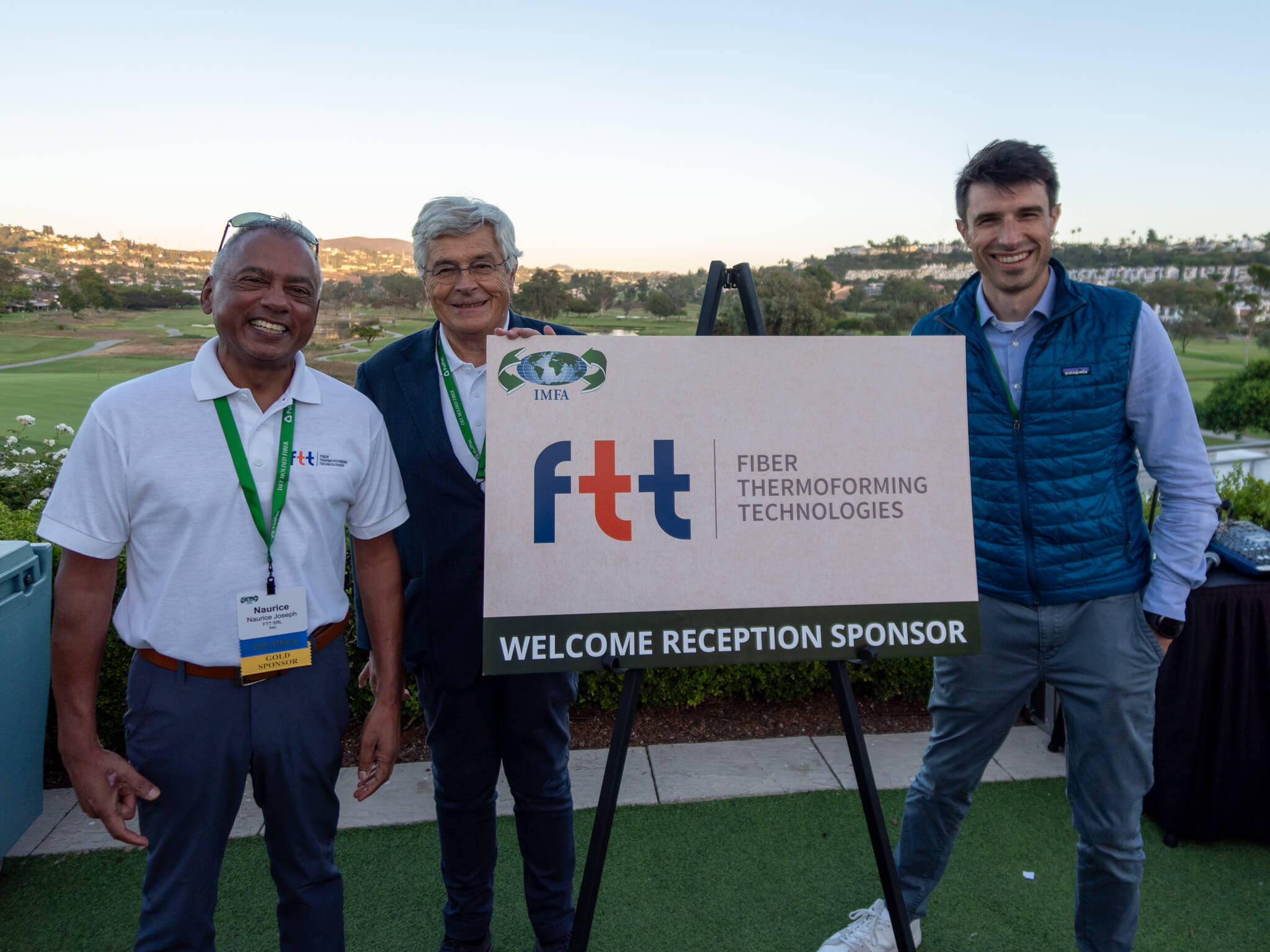
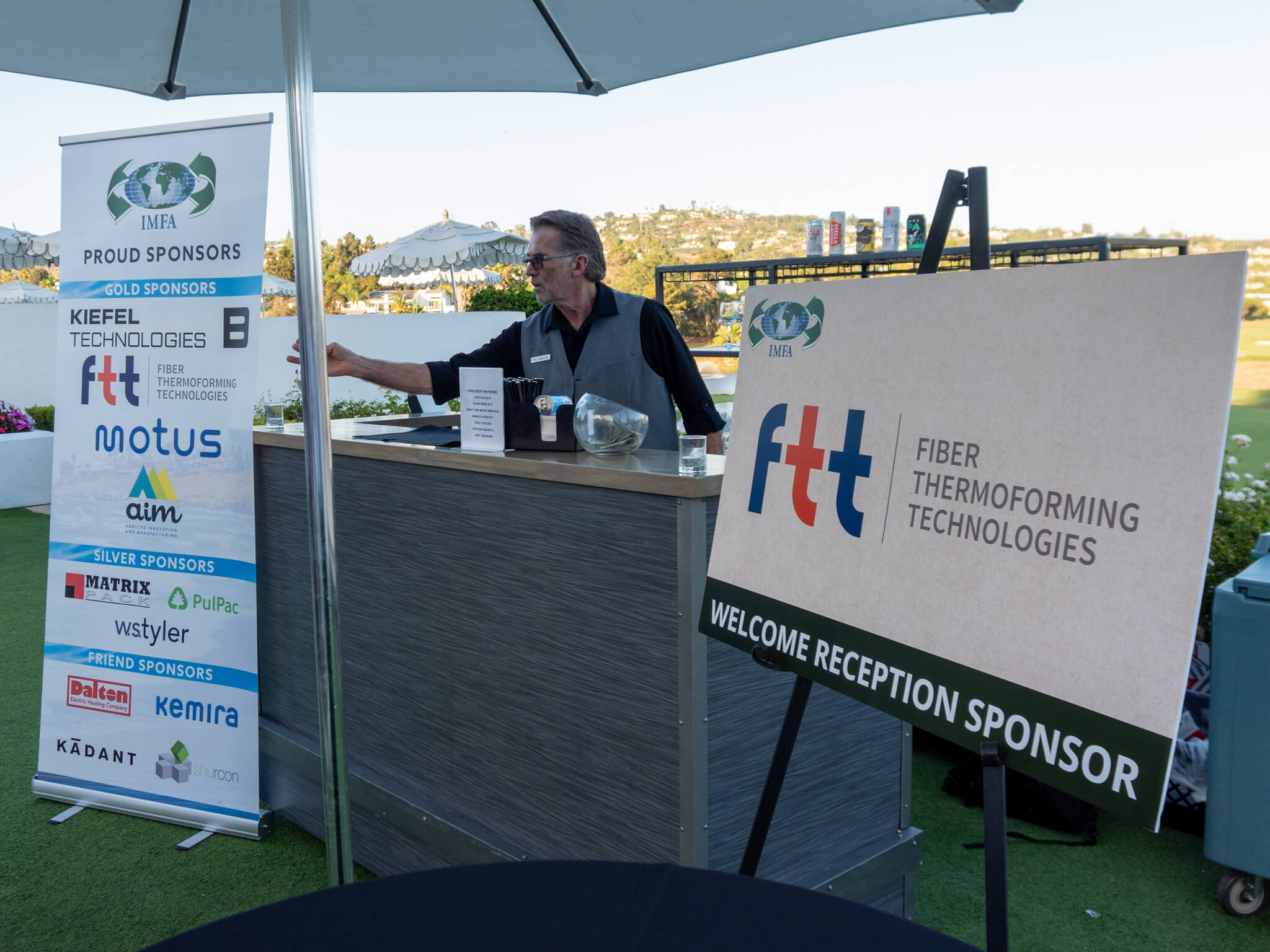
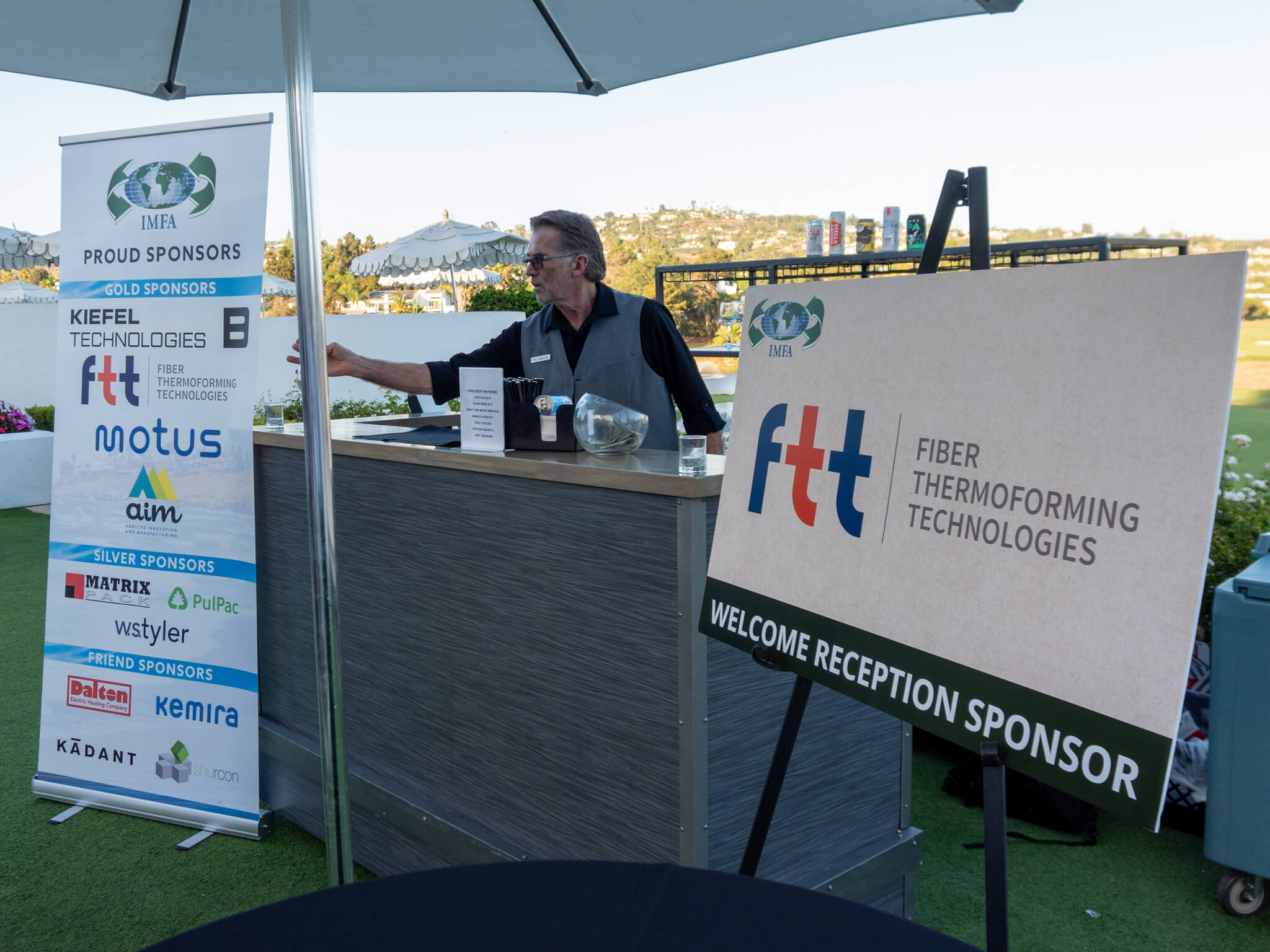
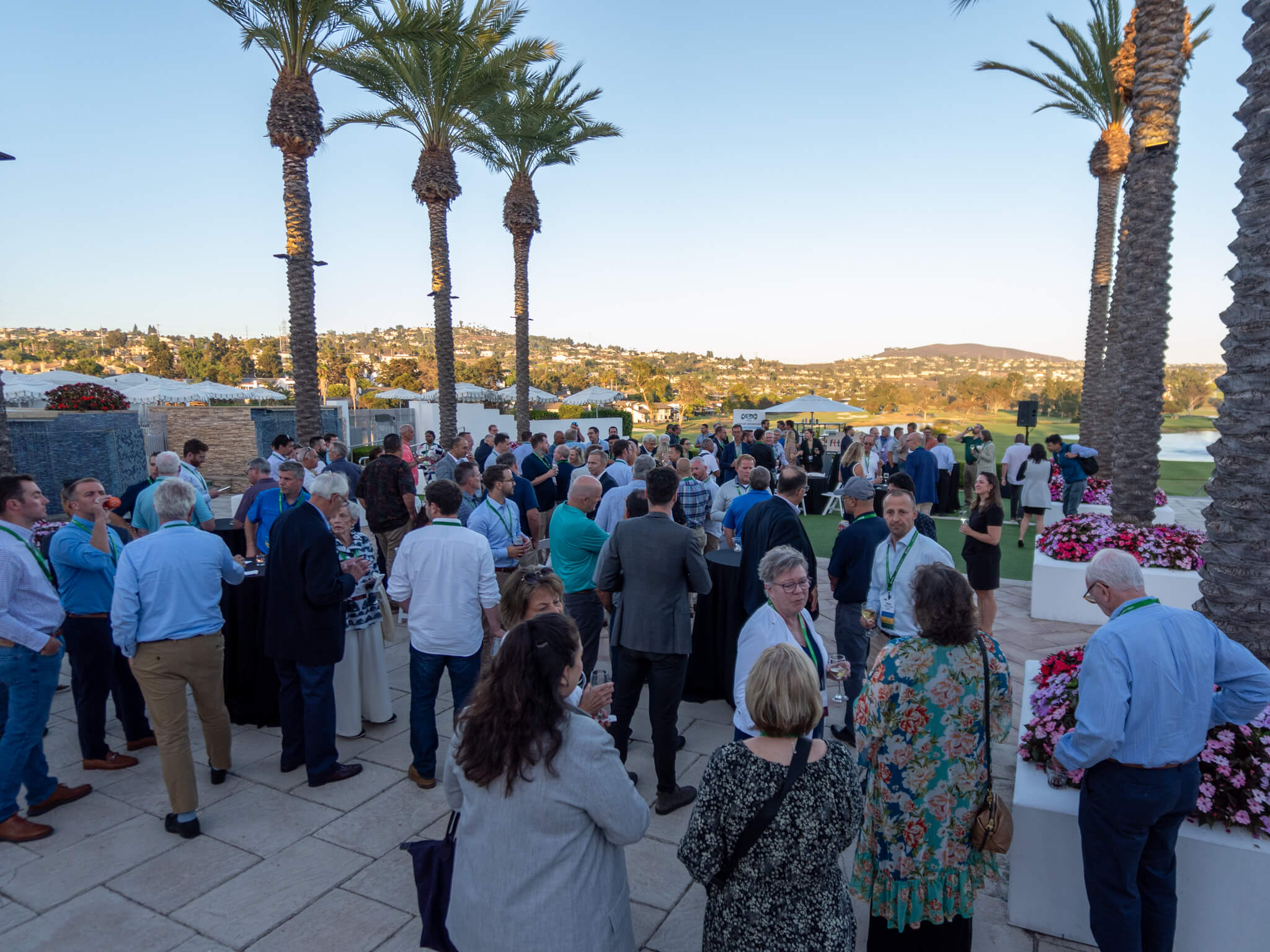
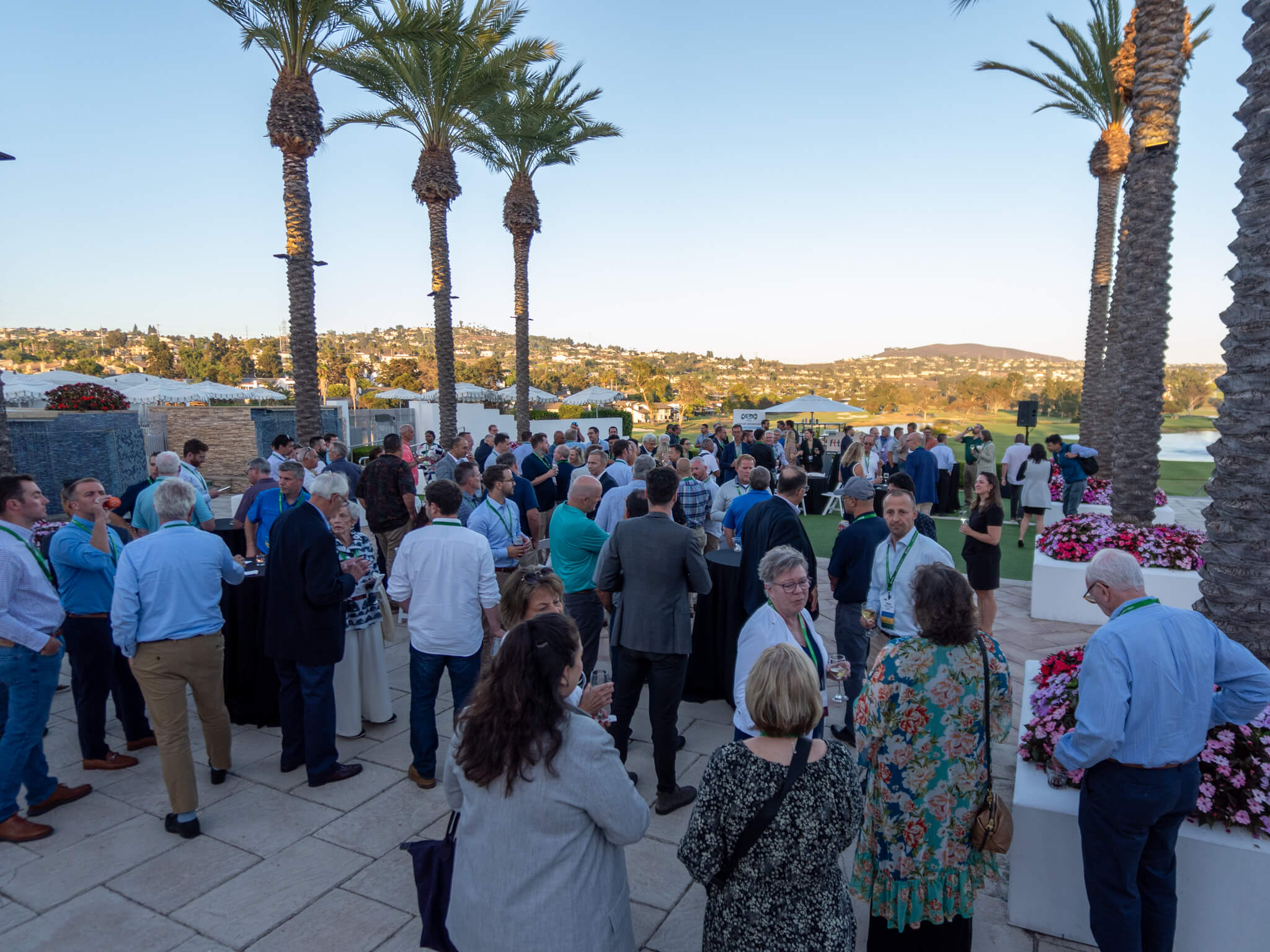
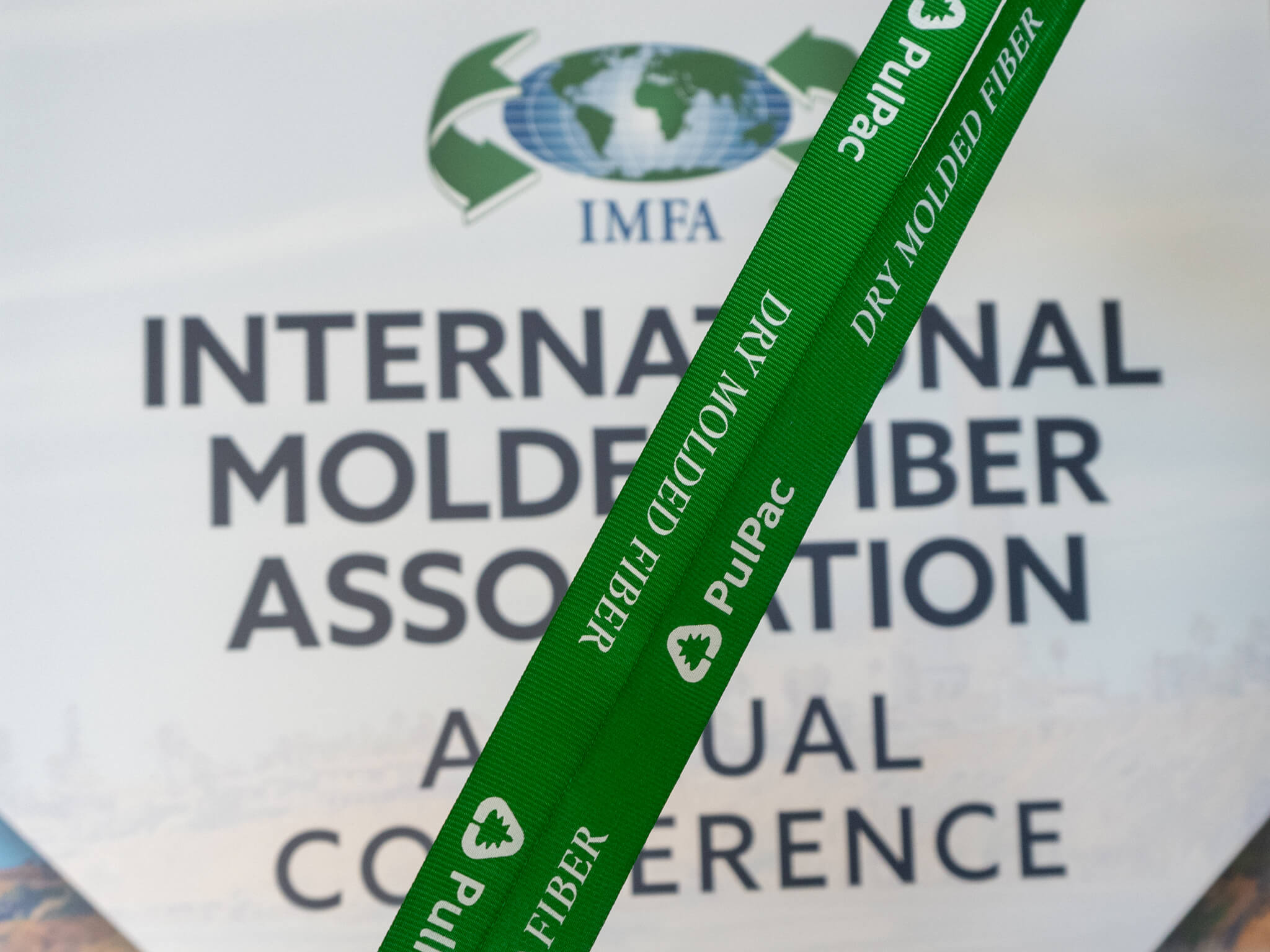
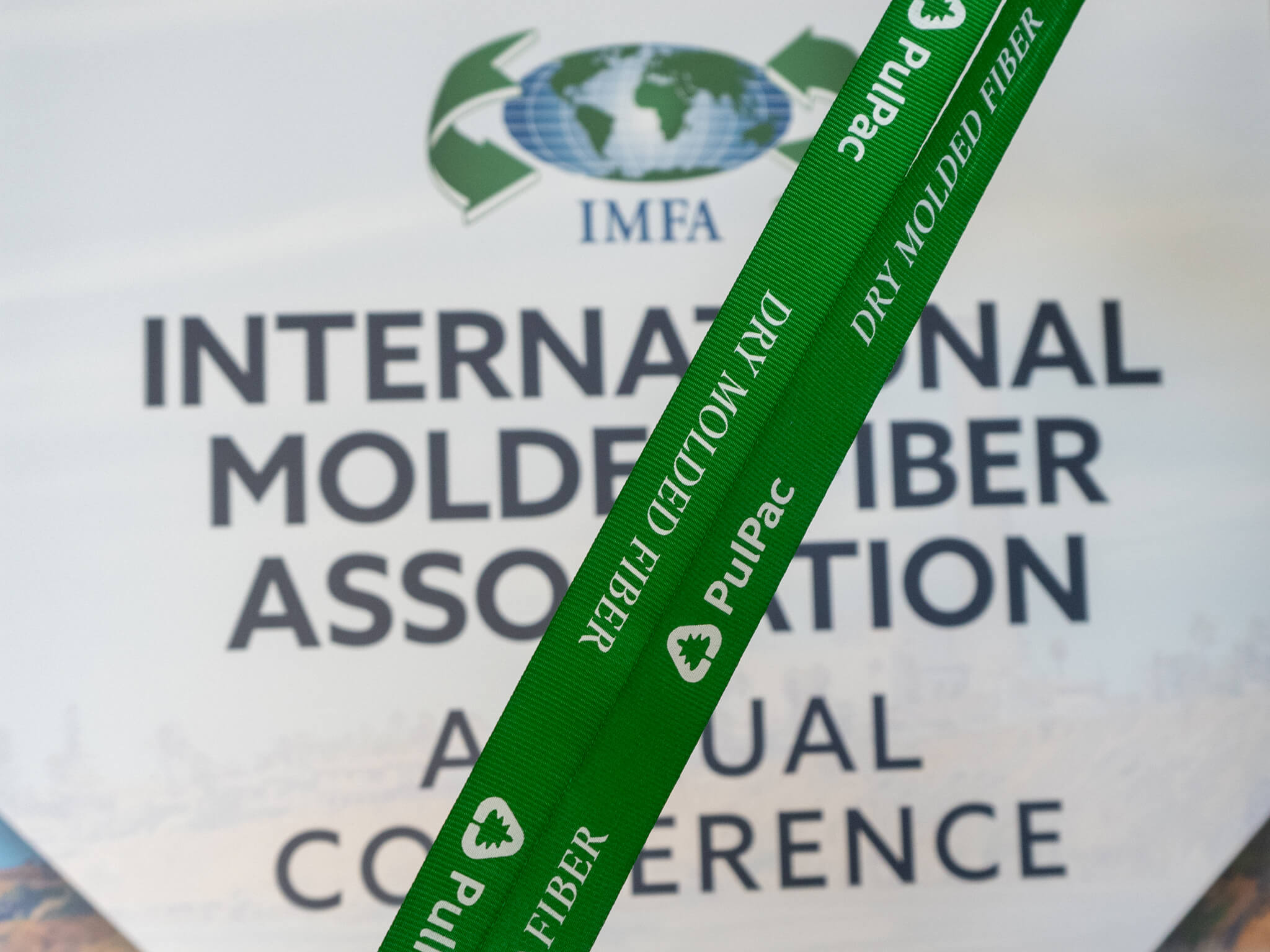
On Wednesday we all got into town and swung by registration to get lanyards and conference materials, sponsored by PulPac. We also got to enjoy the all-new exhibitor hall, where all attendees had the opportunity to connect with individuals and organizations that are pushing the boundaries of what molded fiber can do. As a pilot, we were incredibly pleased to have over a dozen companies participate as exhibitors, and we're looking forward to bringing this back next year!
Once registered, we were once again treated to an opening reception by our friends at FTT. The views couldn't have been better setting over the coastal mountains, and we hope everyone had a great time reconnecting with colleagues from across the globe.
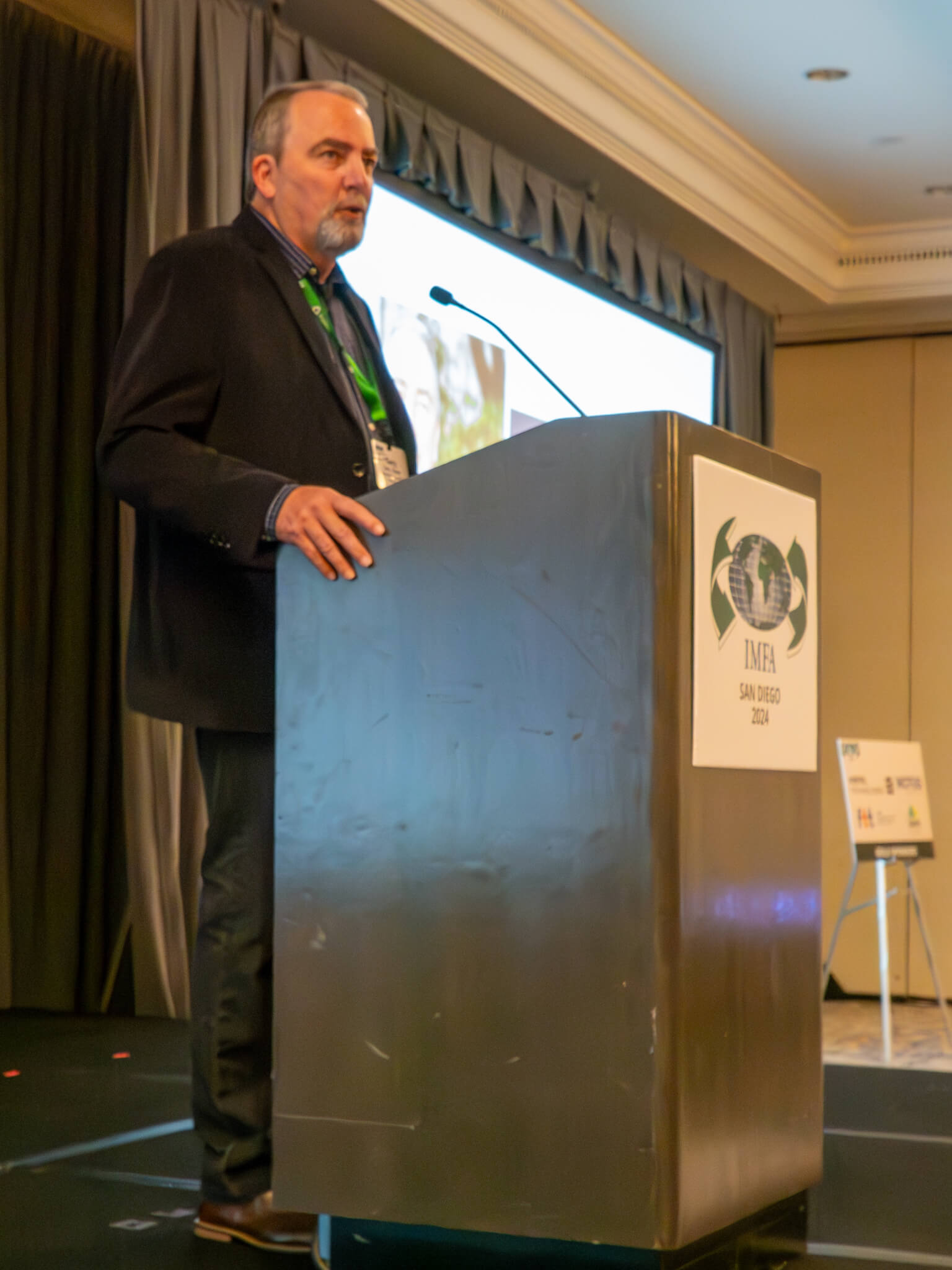
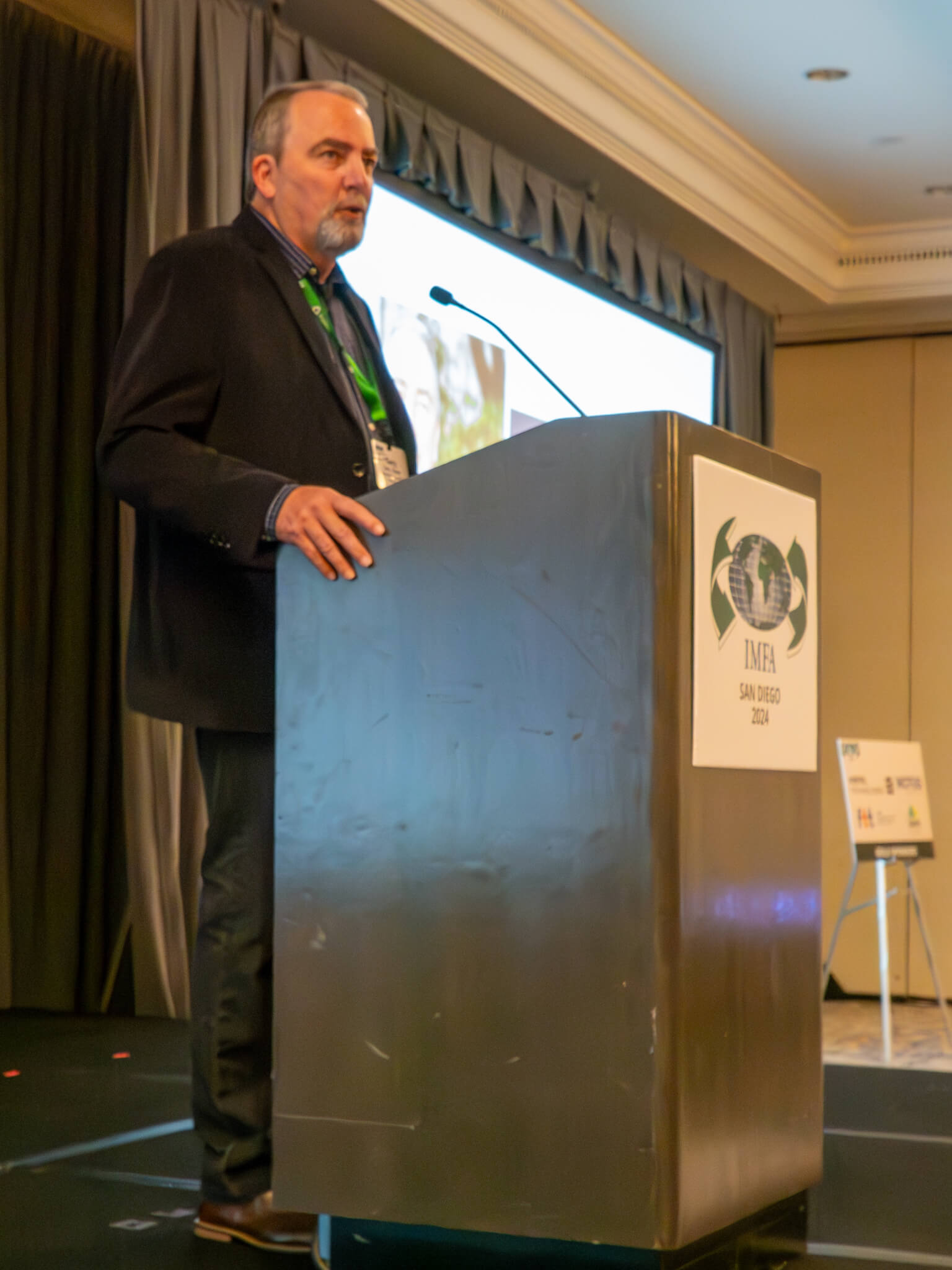
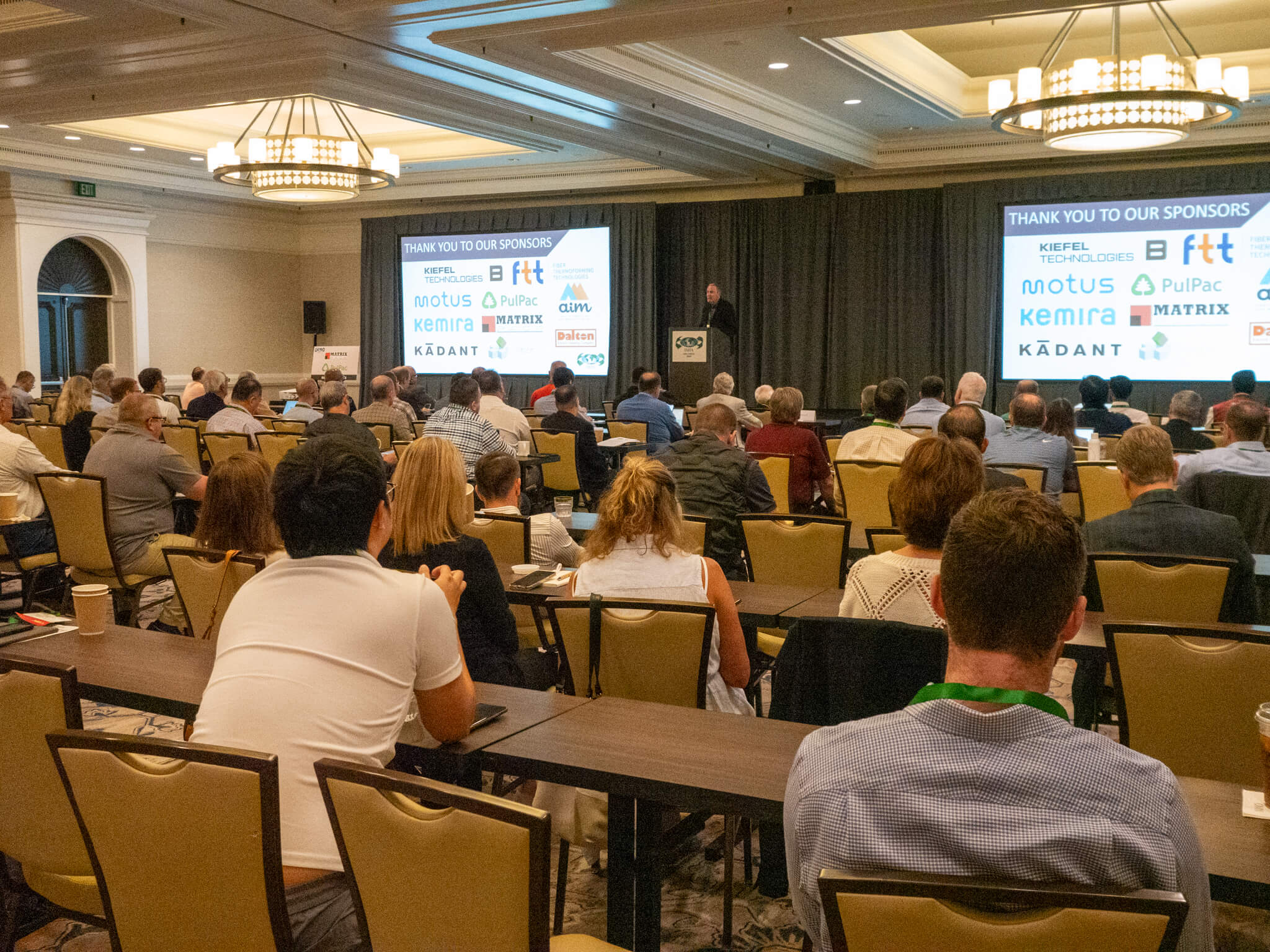
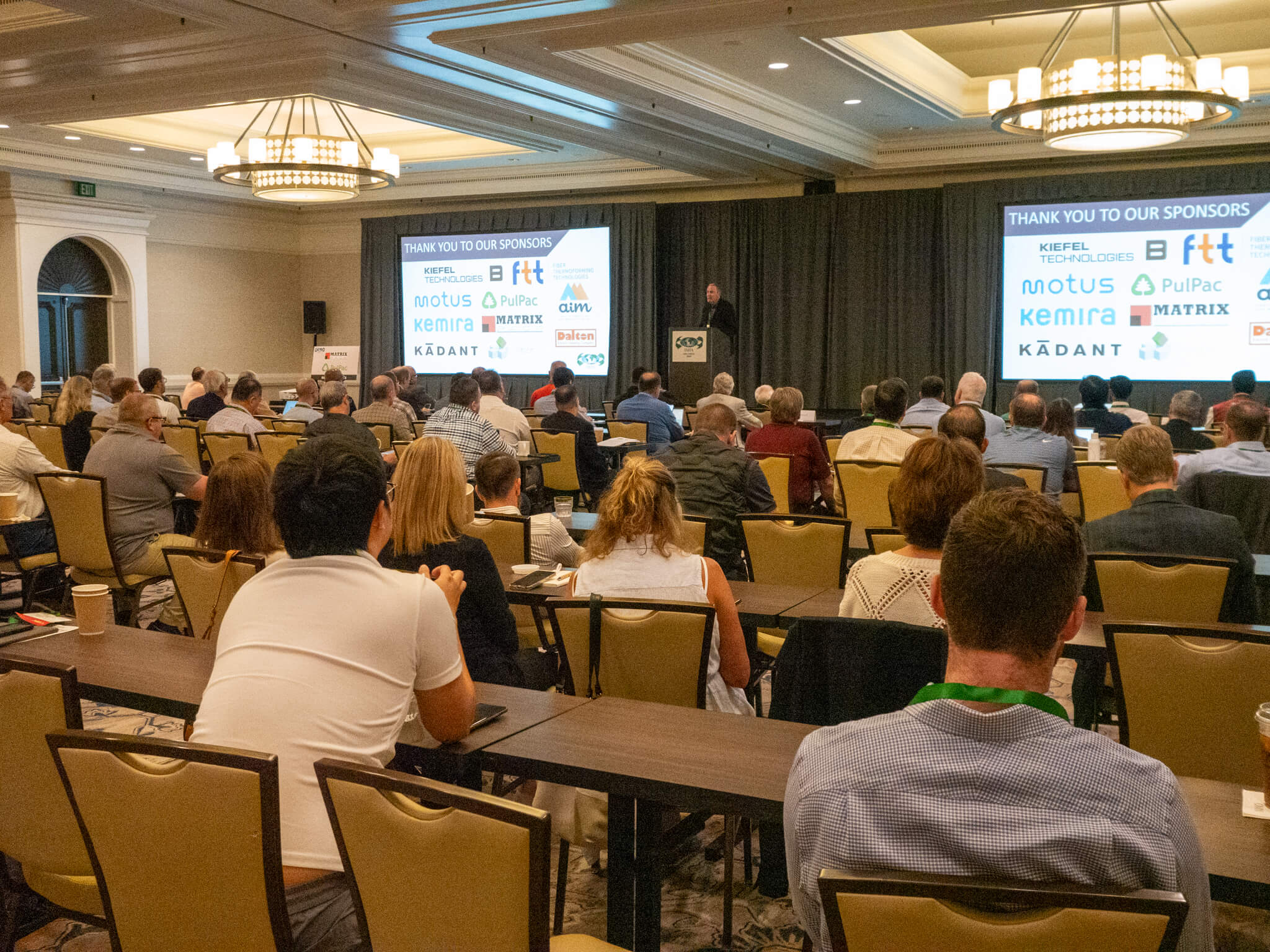
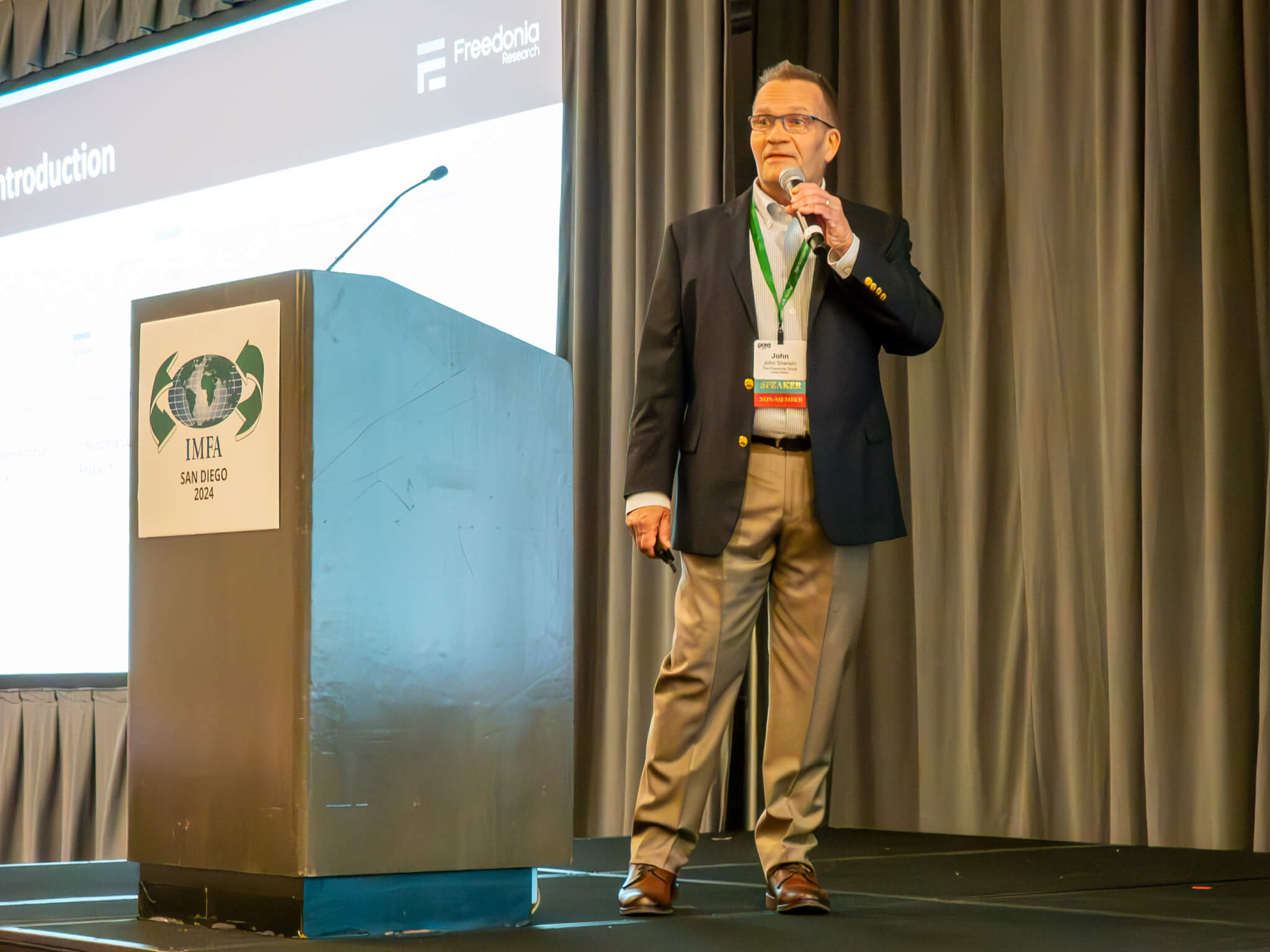
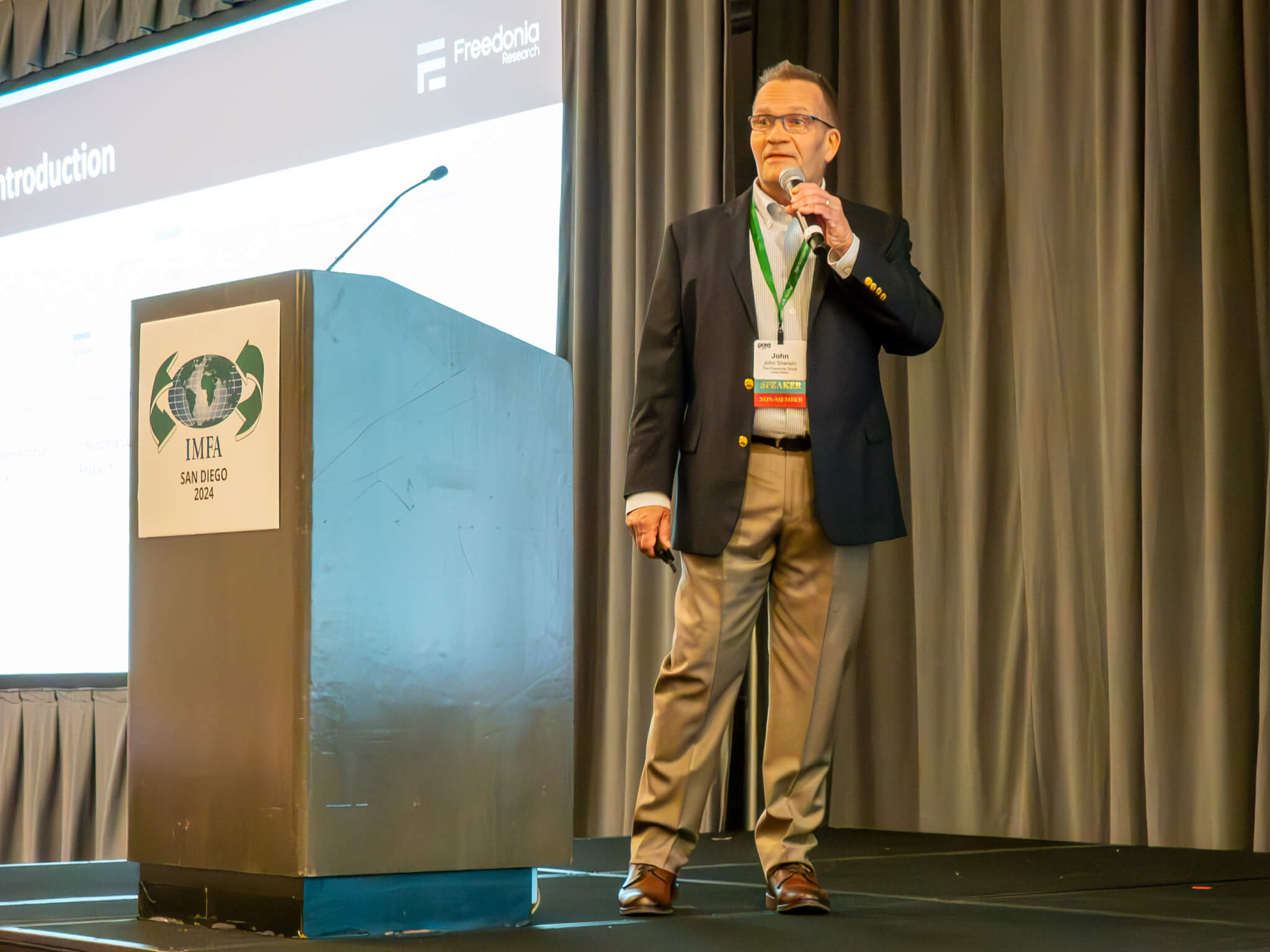
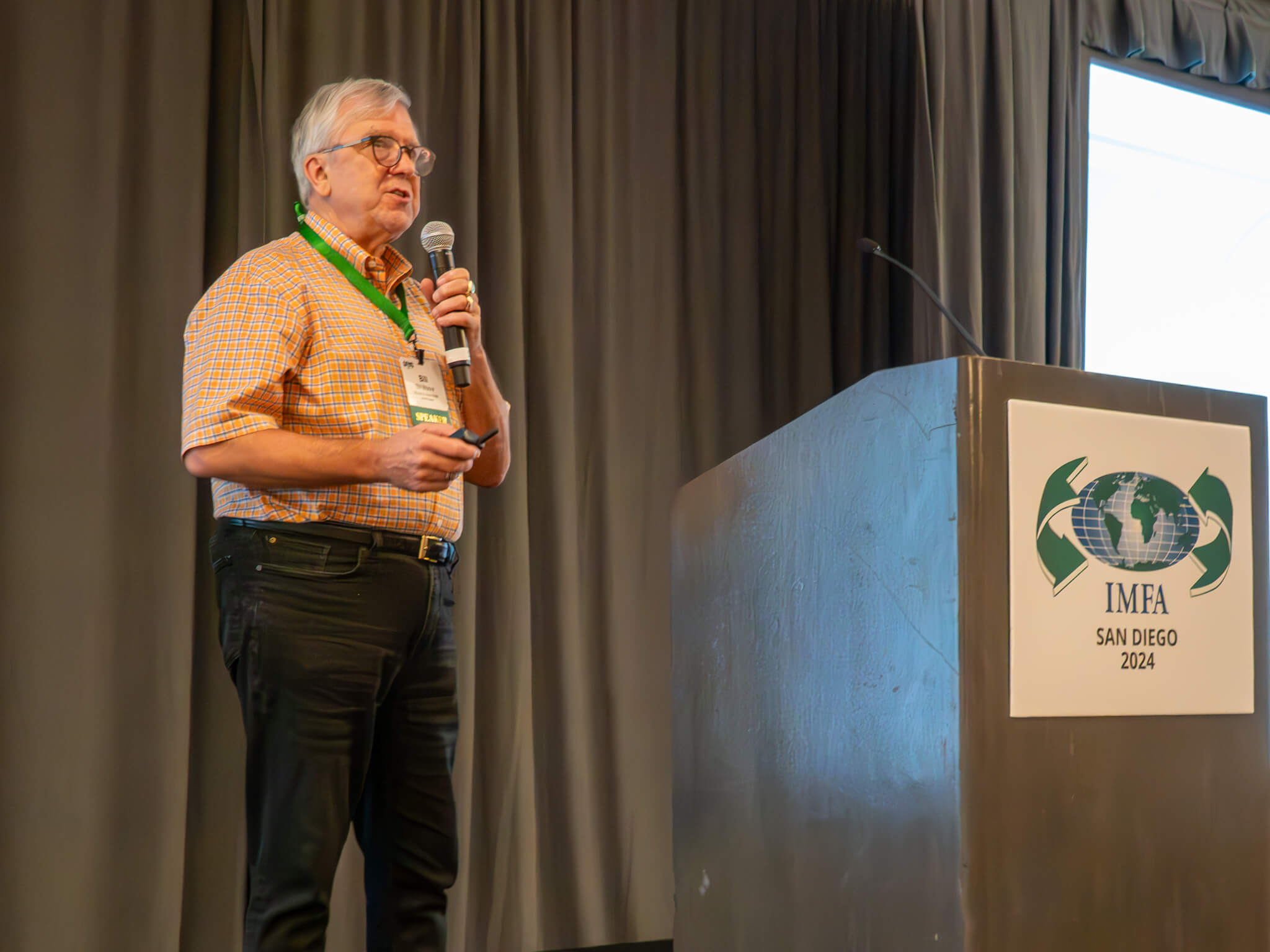
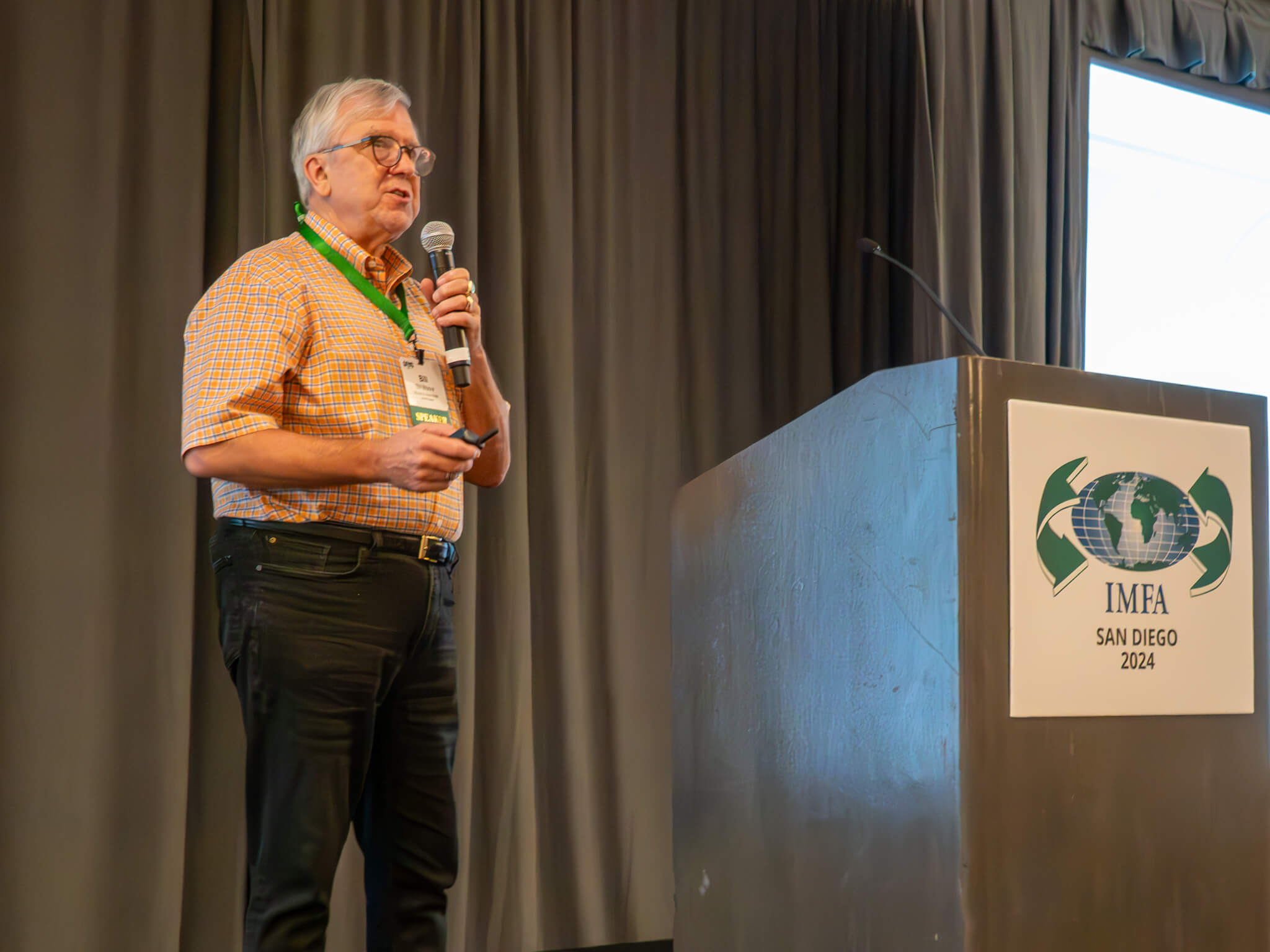
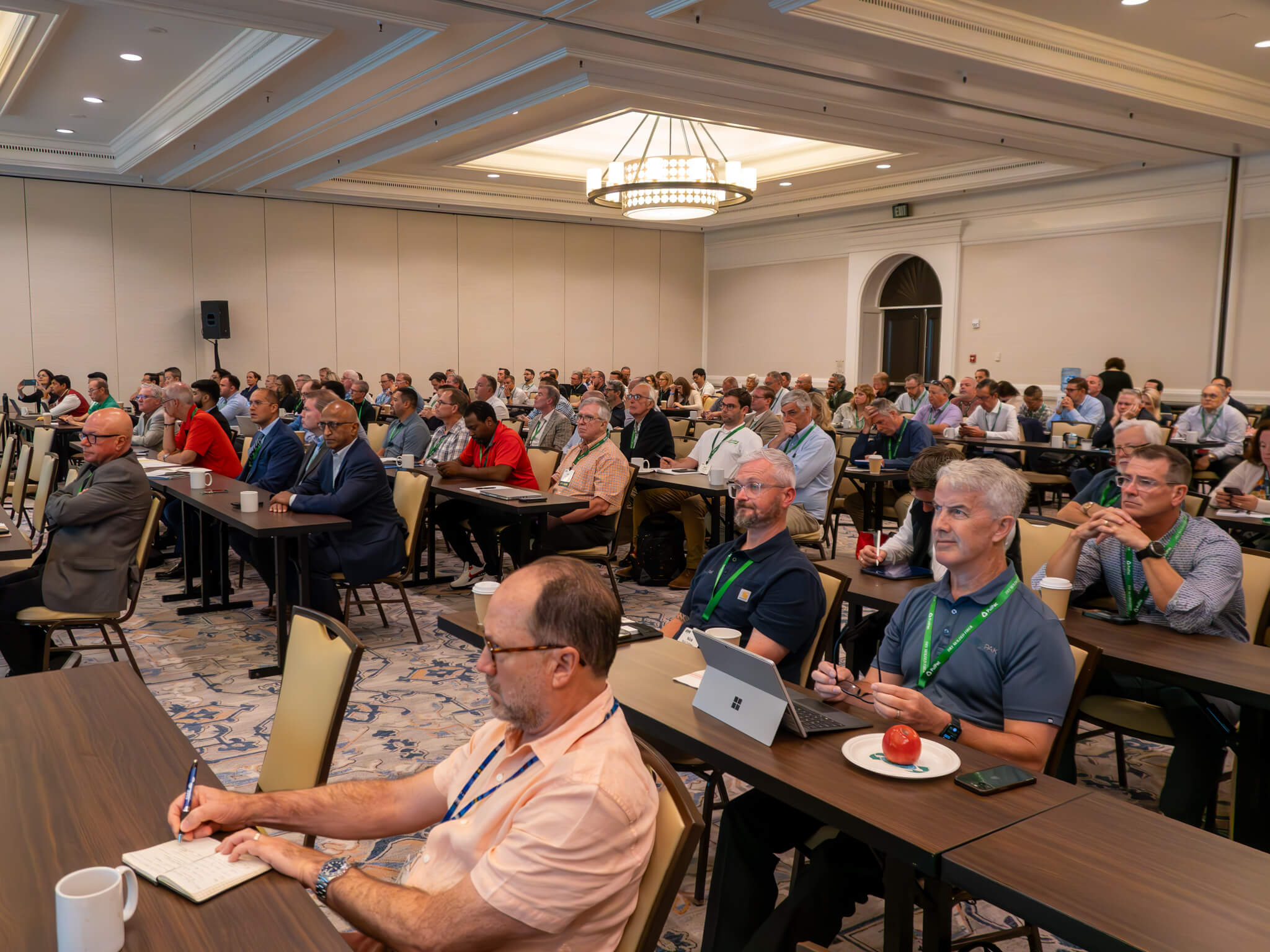
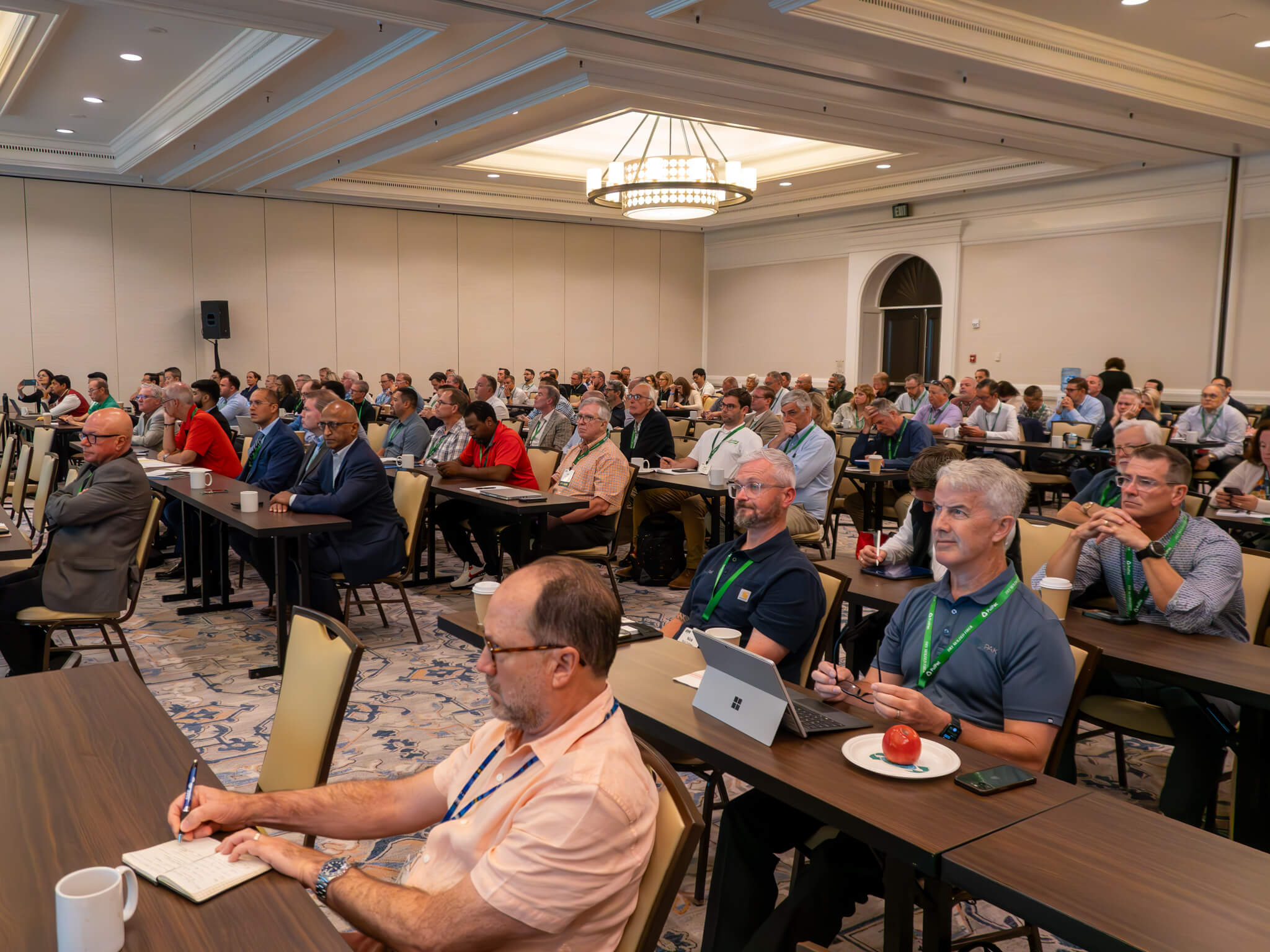
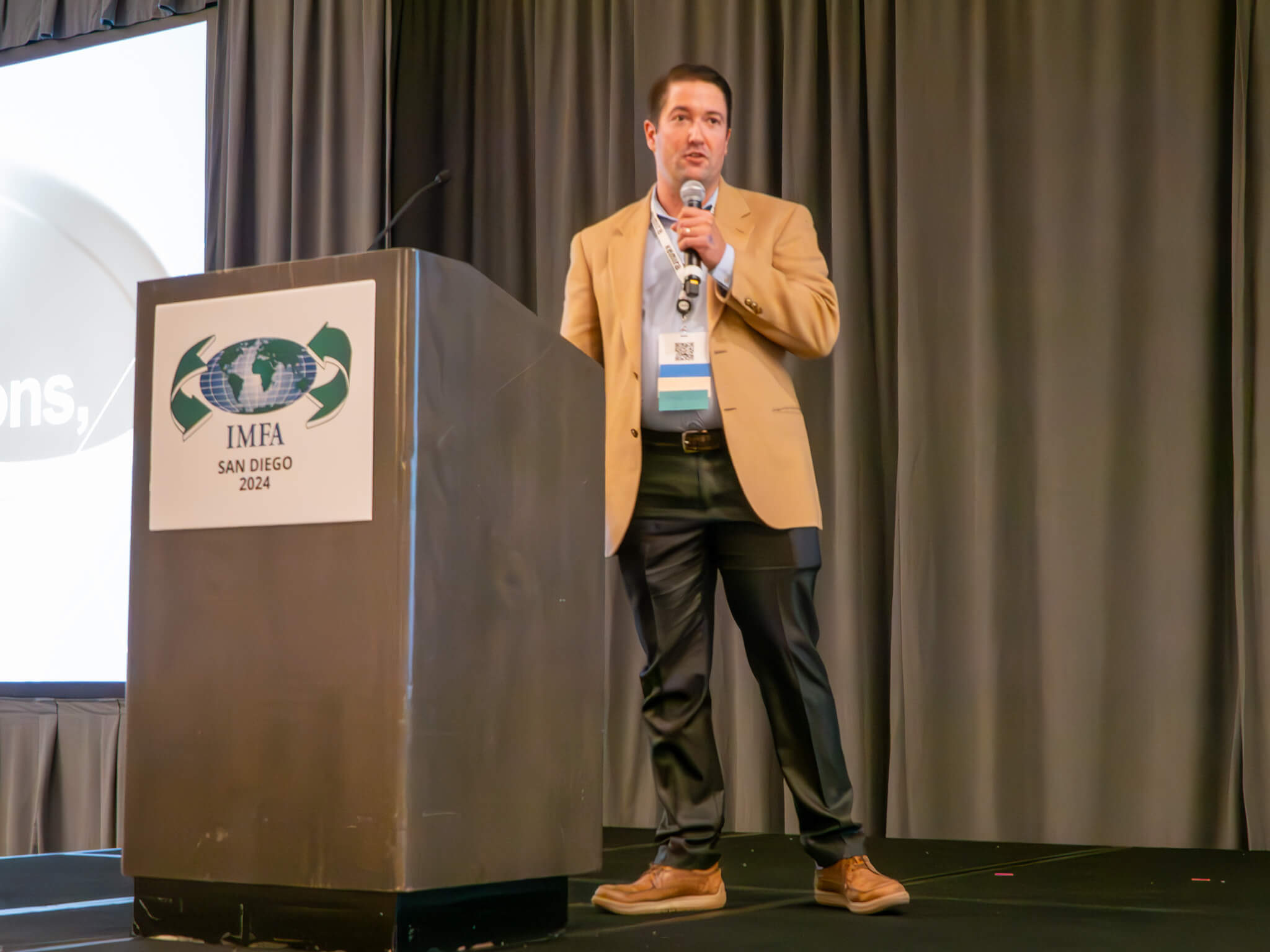
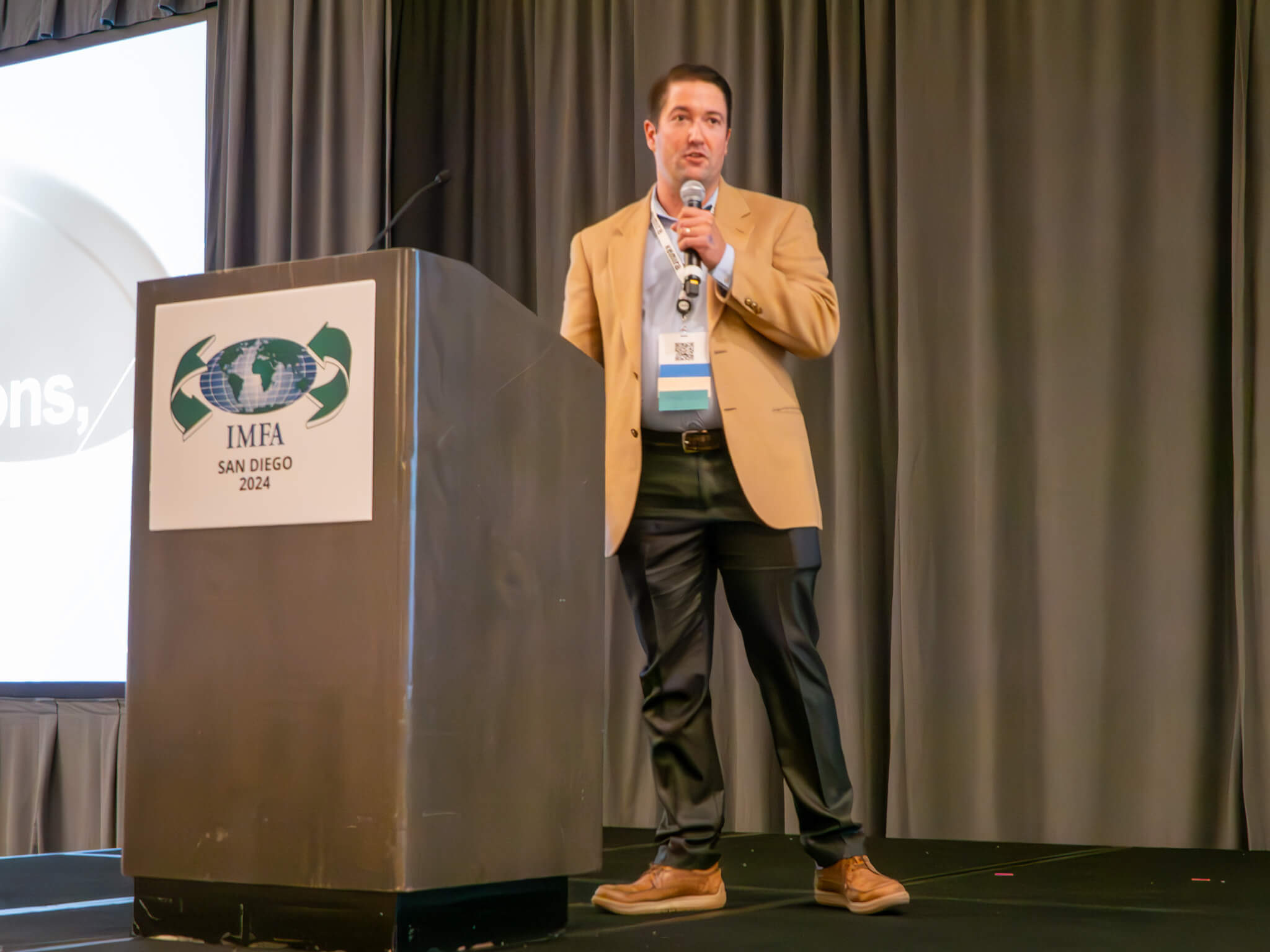
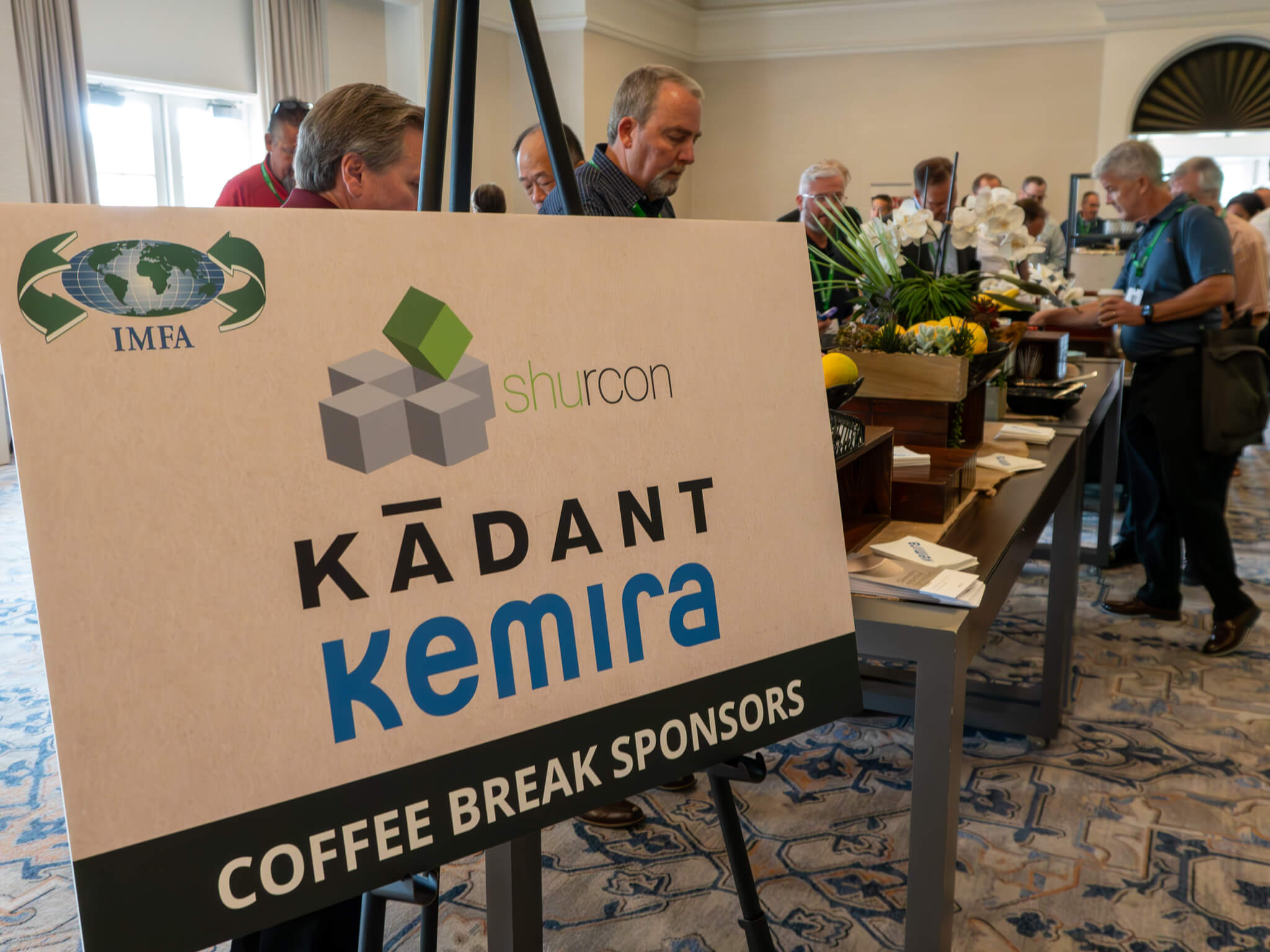
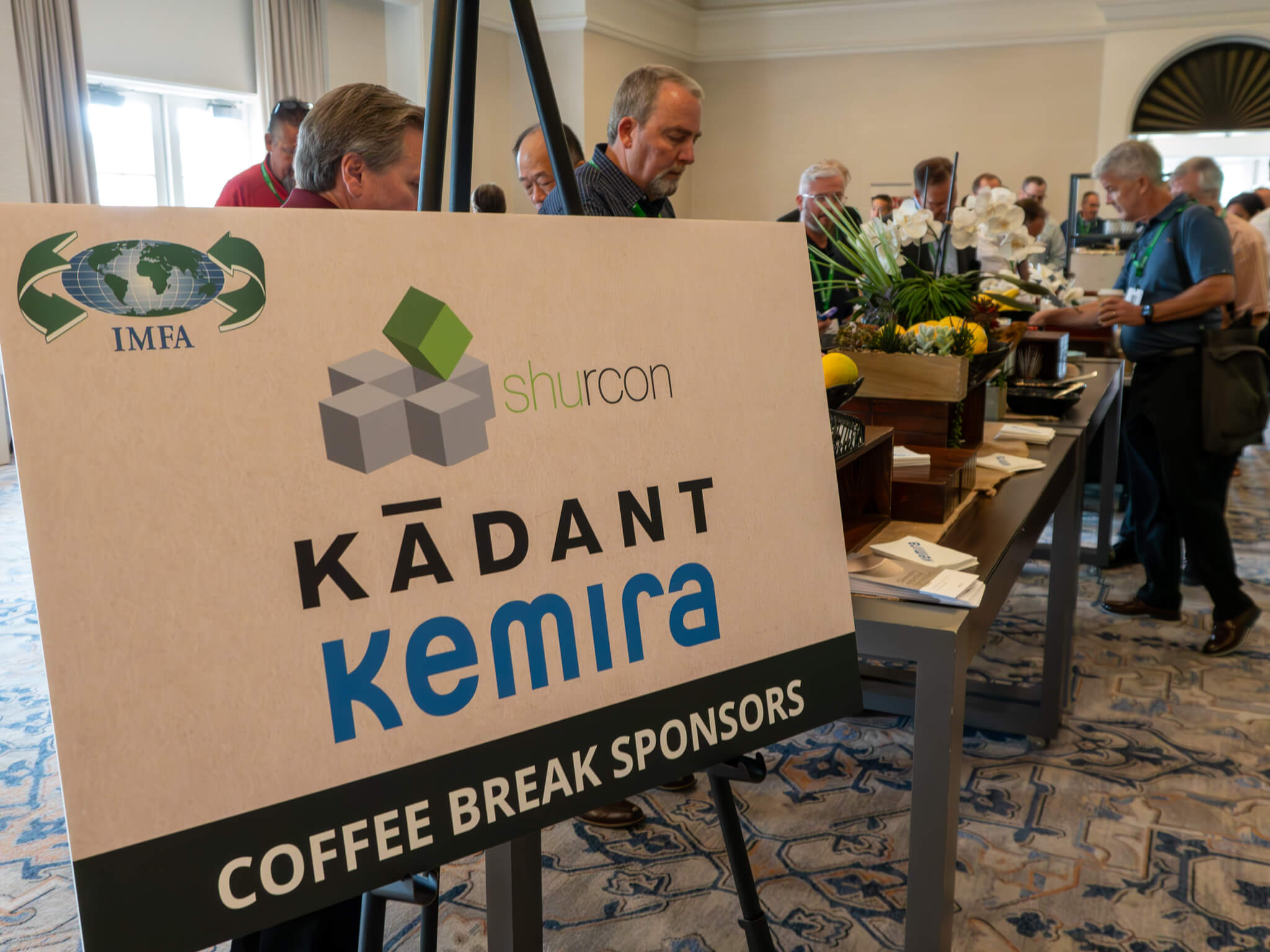
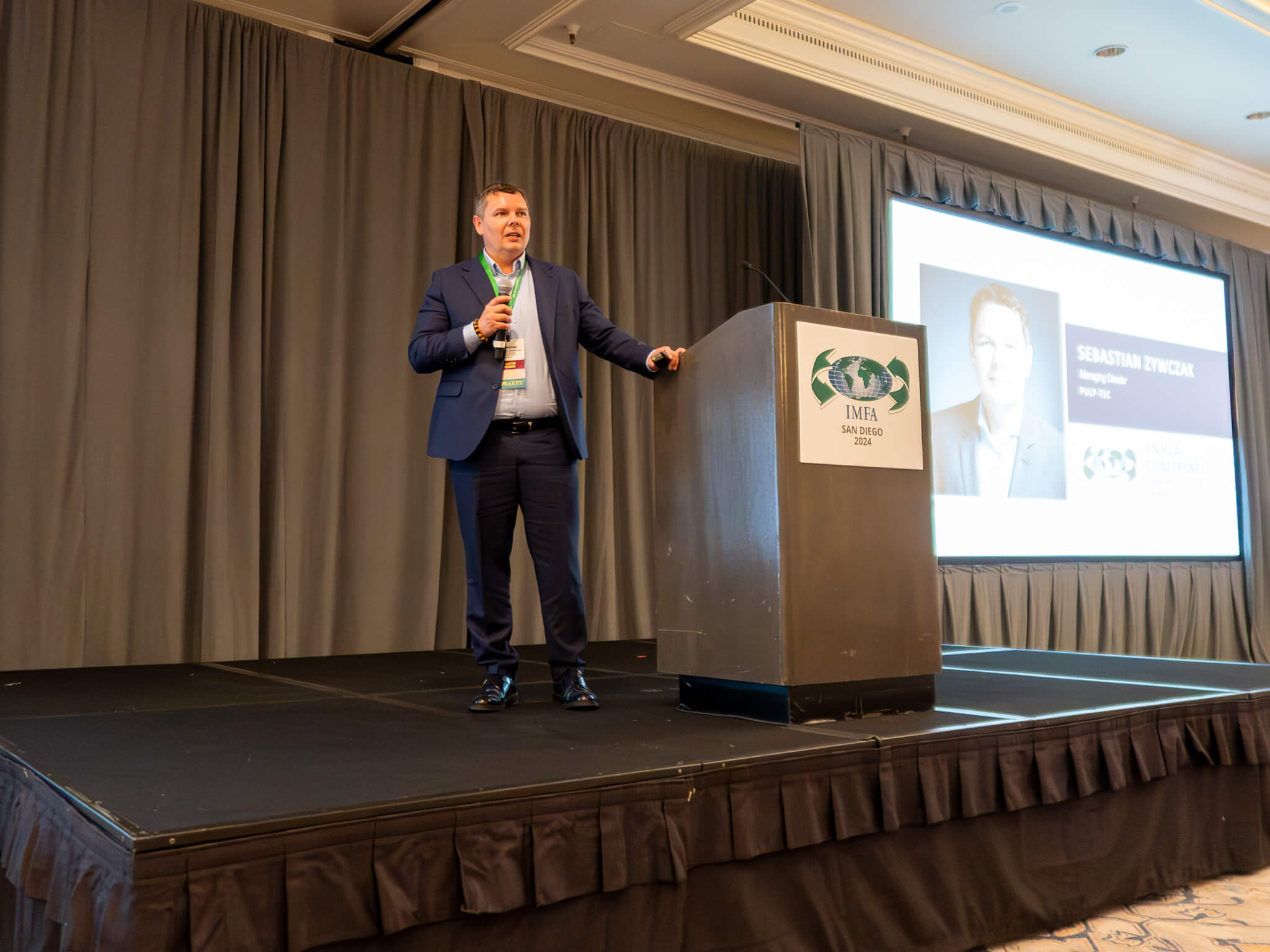
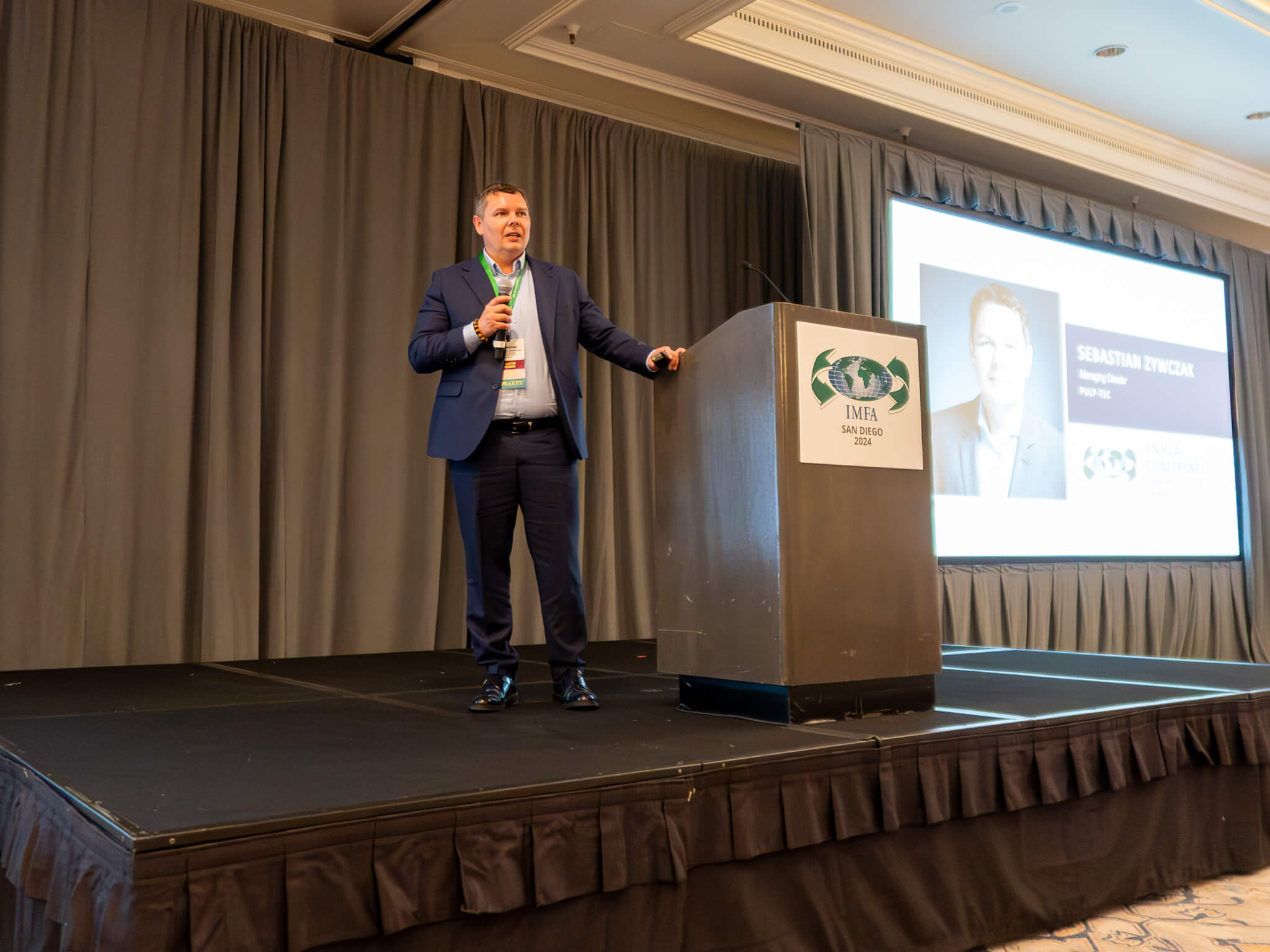
With our welcome reception behind us, our 178 attendees were ready to hit the ground running with the first round of presentations. Following breakfast together on Thursday morning, IMFA Executive Chairman Gary Visser welcomed the attendees, reflecting on the strong foundation of the association. He emphasized the growing demand for sustainable packaging and the bright future of molded fiber products. Attendees were also excited to see so many newcomers from different age groups and regions, contributing to a positive and diverse atmosphere for the conference.
John Sherwin from The Freedonia Group highlighted the rapid growth of the global molded fiber market, driven by demand for sustainable packaging, with the food service sector leading the way. He also discussed emerging opportunities in protective packaging and beverage rings, stressing that continued growth will depend on innovation, regulatory adaptation, and meeting evolving consumer needs.
Among a variety of interesting industry updates, Bill Moore from Moore & Associates spoke about how the decline in newsprint production has led to a decrease in total paper and fiber product output, with many newsprint mills converting to OCC. This shift has increased the use of double-lined kraft in molded fiber products, particularly Grade A, which is most suitable for molded fiber production. Quality and EPR issues have been addressed in five U.S. states, Europe, and Canada.
Alex Beam from Kemira presented “Chemistry and Molded Fiber - Testing, Application, and Best Practices,” focusing on defoamers. He explained foam formation, its issues, and how to select the best defoamers to tackle physical and mechanical problems. He also mentioned that pure liquids don’t foam, but surface foam and entrained air can cause significant issues.
Following Alex Beam’s presentation, Pulp-Tec's Sebastian Zywczak shared an IMFA Member profile of Pulp-Tec. Pulp-Tec, originally founded in 1547 and acquired by the Jaegar family in 2008, uses paper pellets to create molded fiber products. Sebastian Zywczak highlighted the company's many locations and its commitment to the circular economy, noting that pulp production has a lower CO2 footprint and that molded pulp is biodegradable and sustainable.
We're proud to always have engaging and informative presentations that go beyond what you might normally find at a conference – but all that attention requires some caffeine to keep up with! We're grateful to Shurcon, Kadant, and Kemira for sponsoring our breaks and making sure the coffee was always flowing.
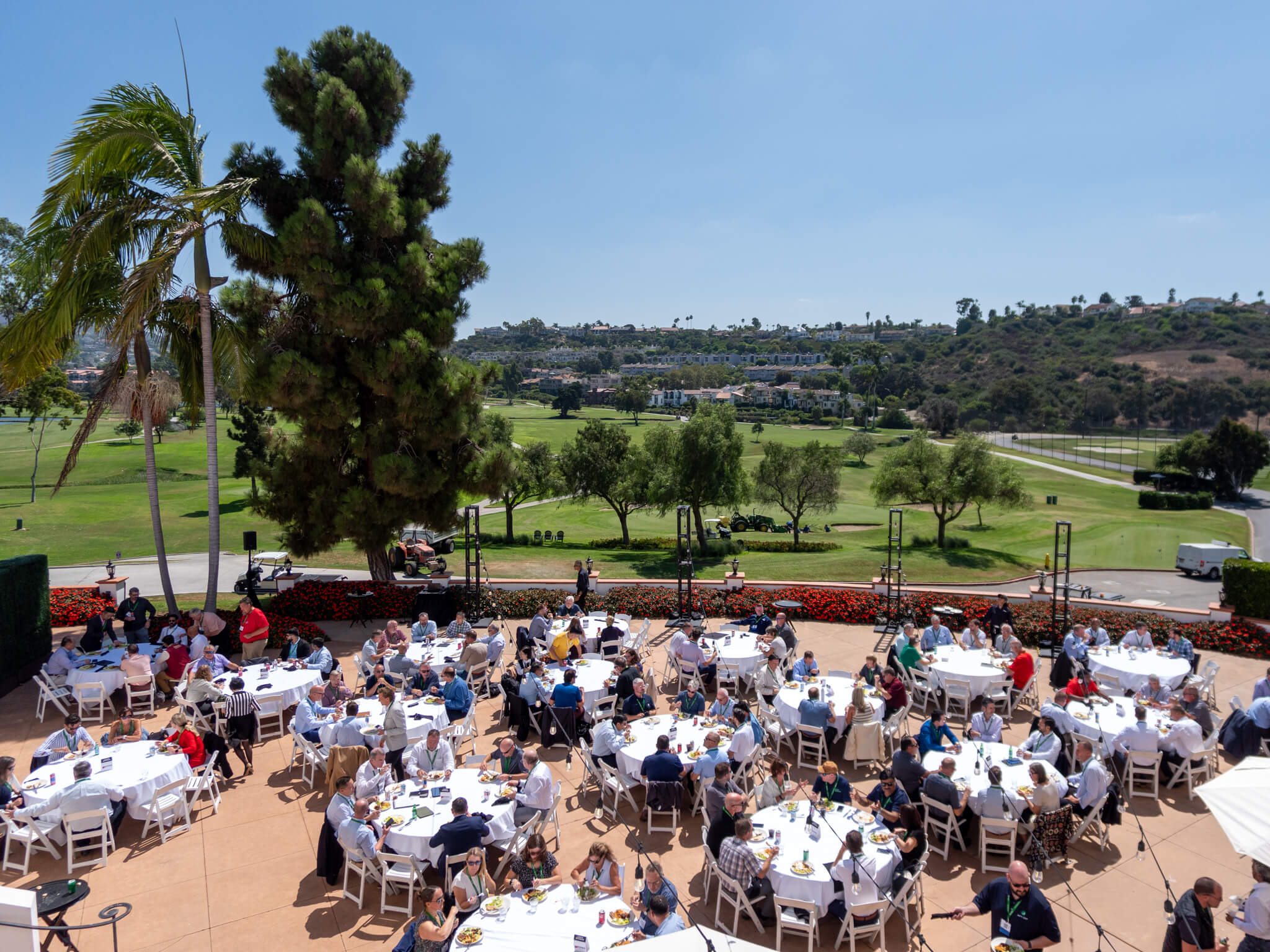
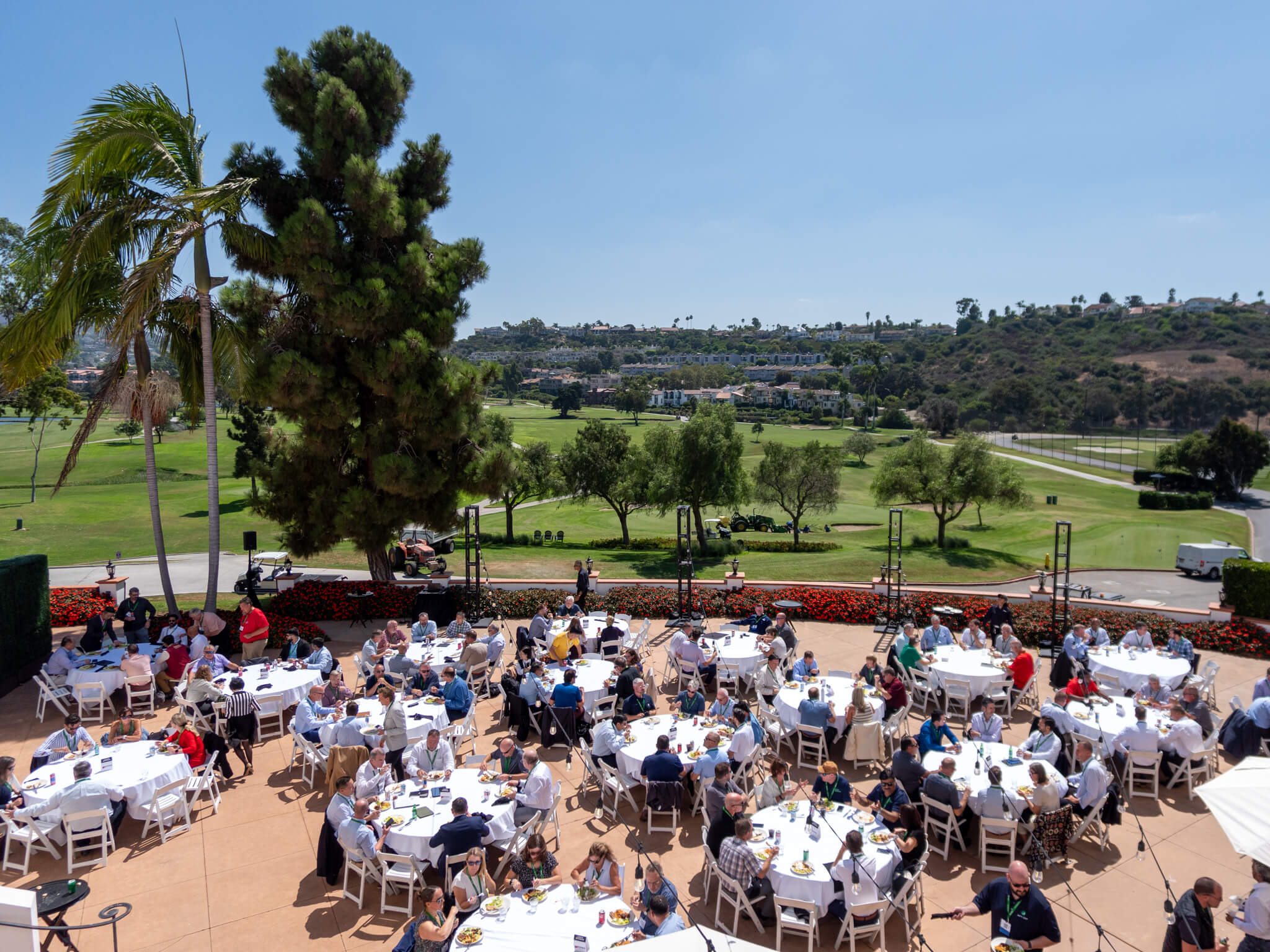
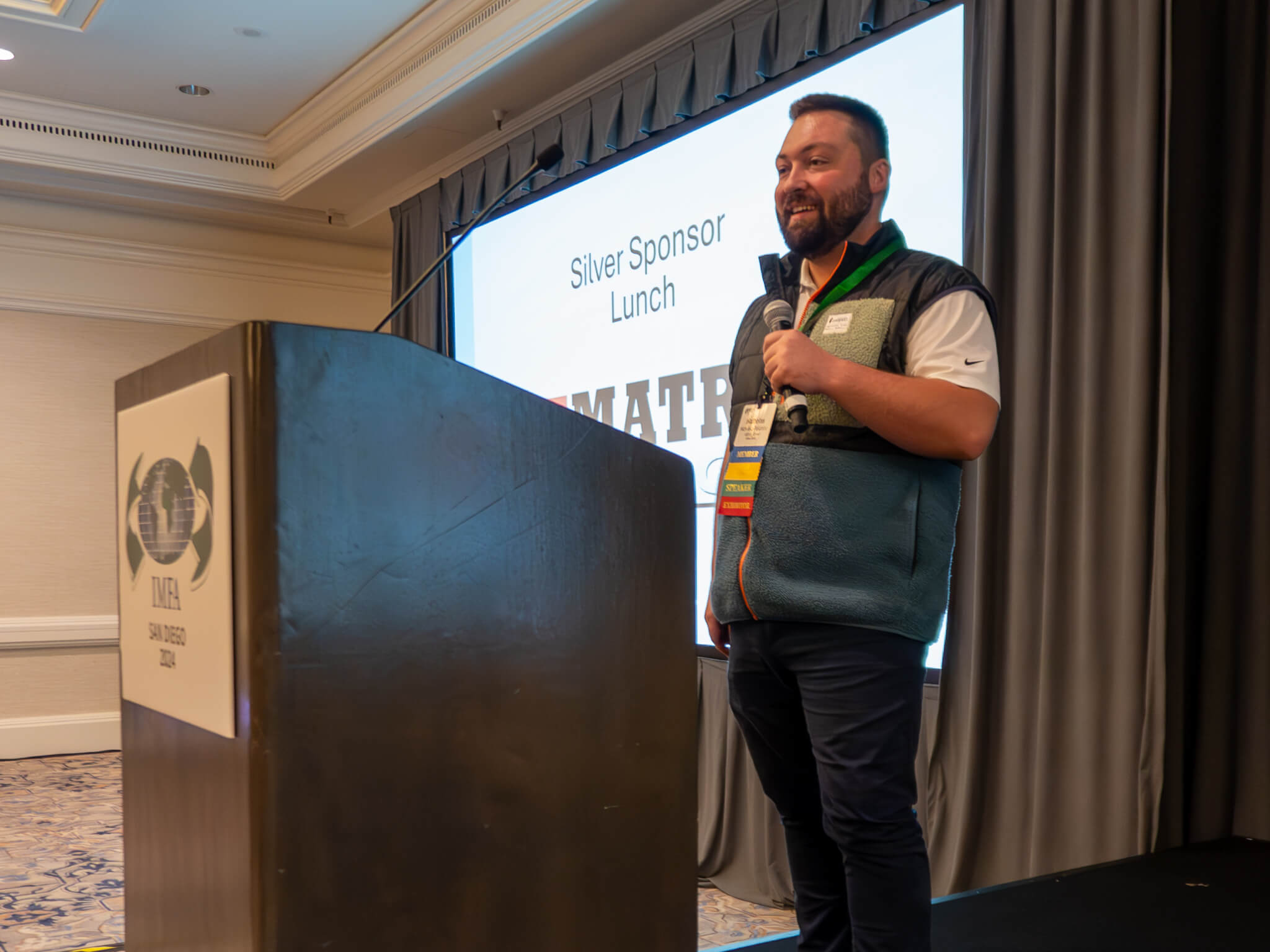
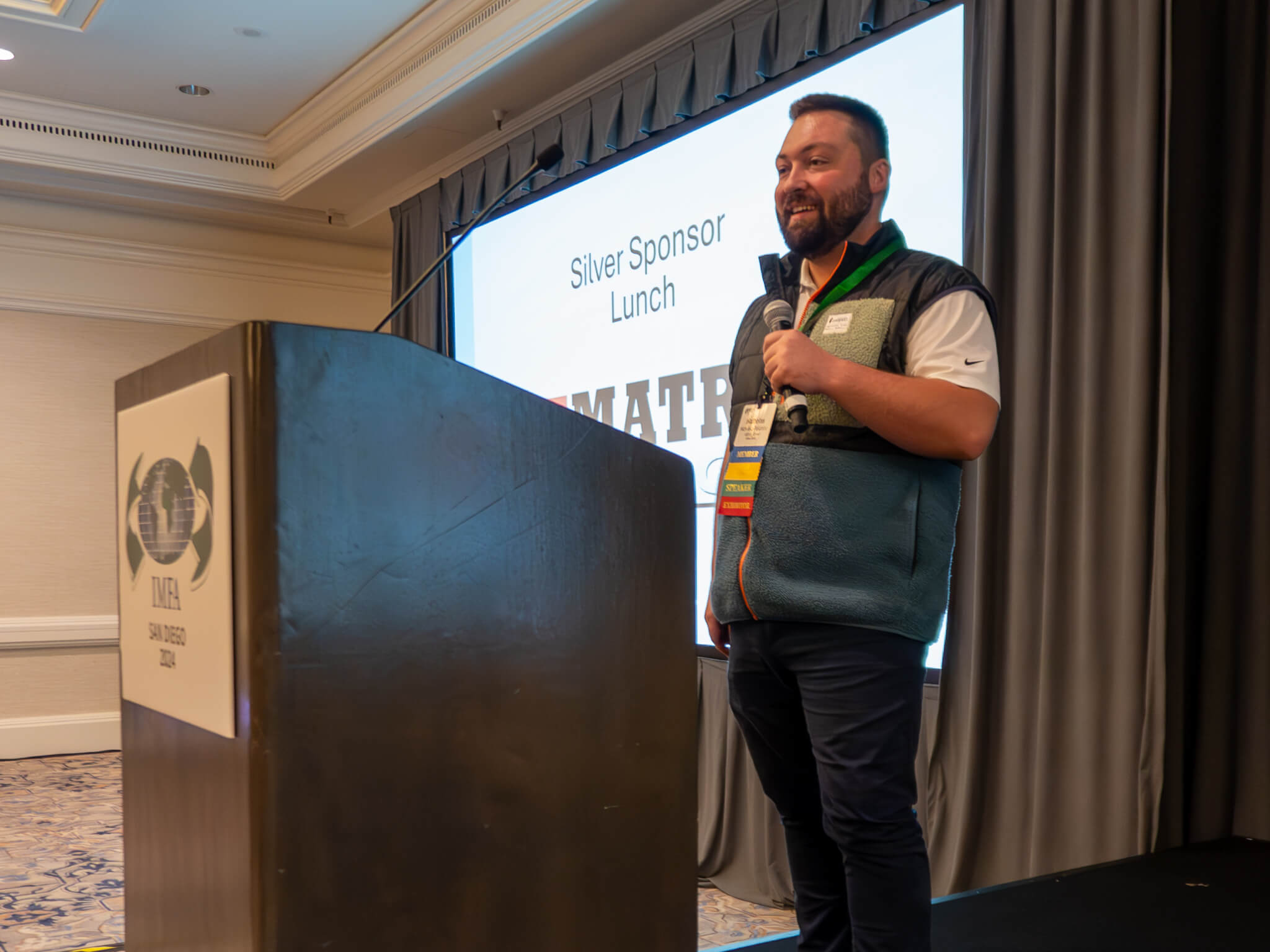
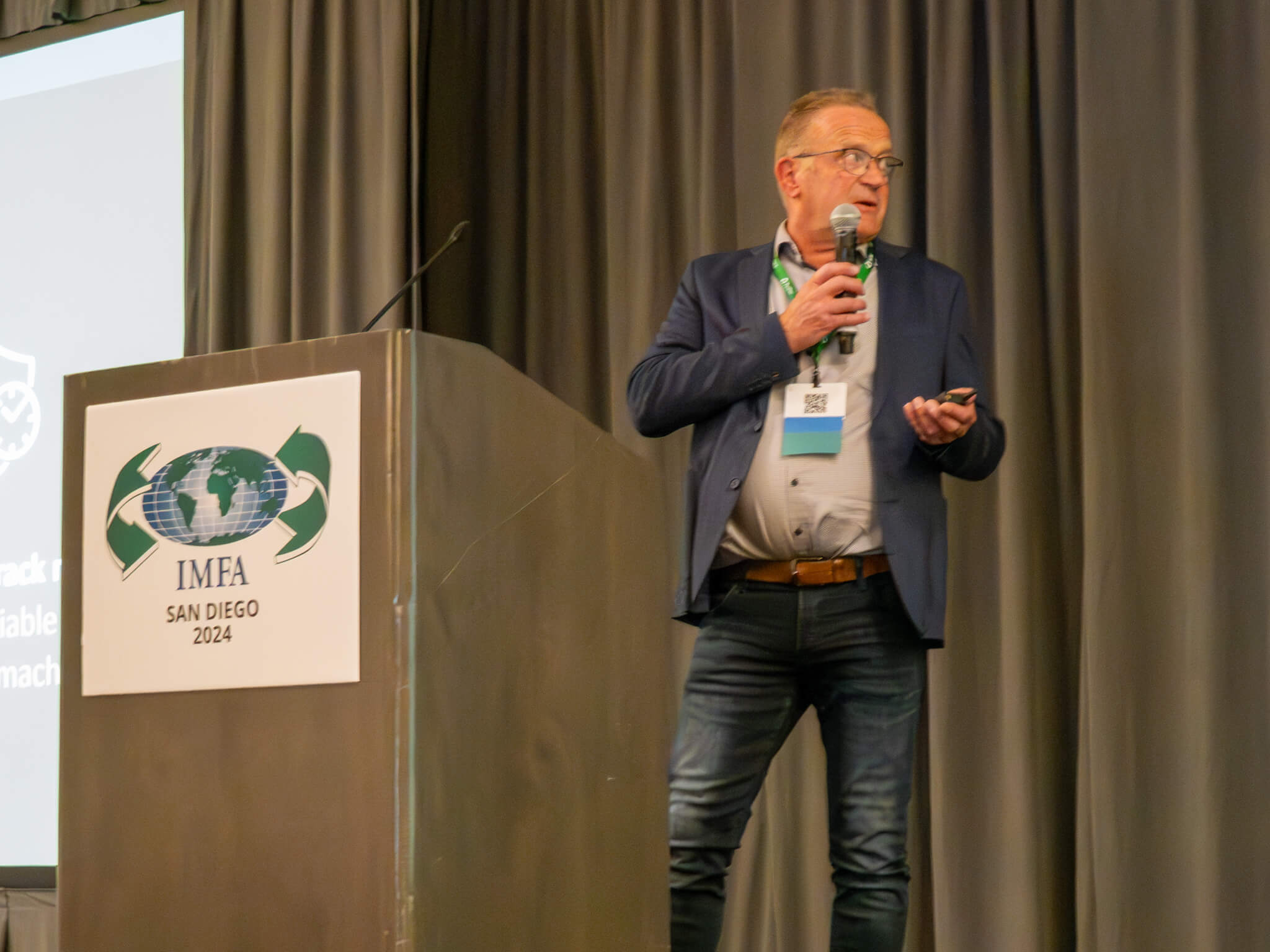
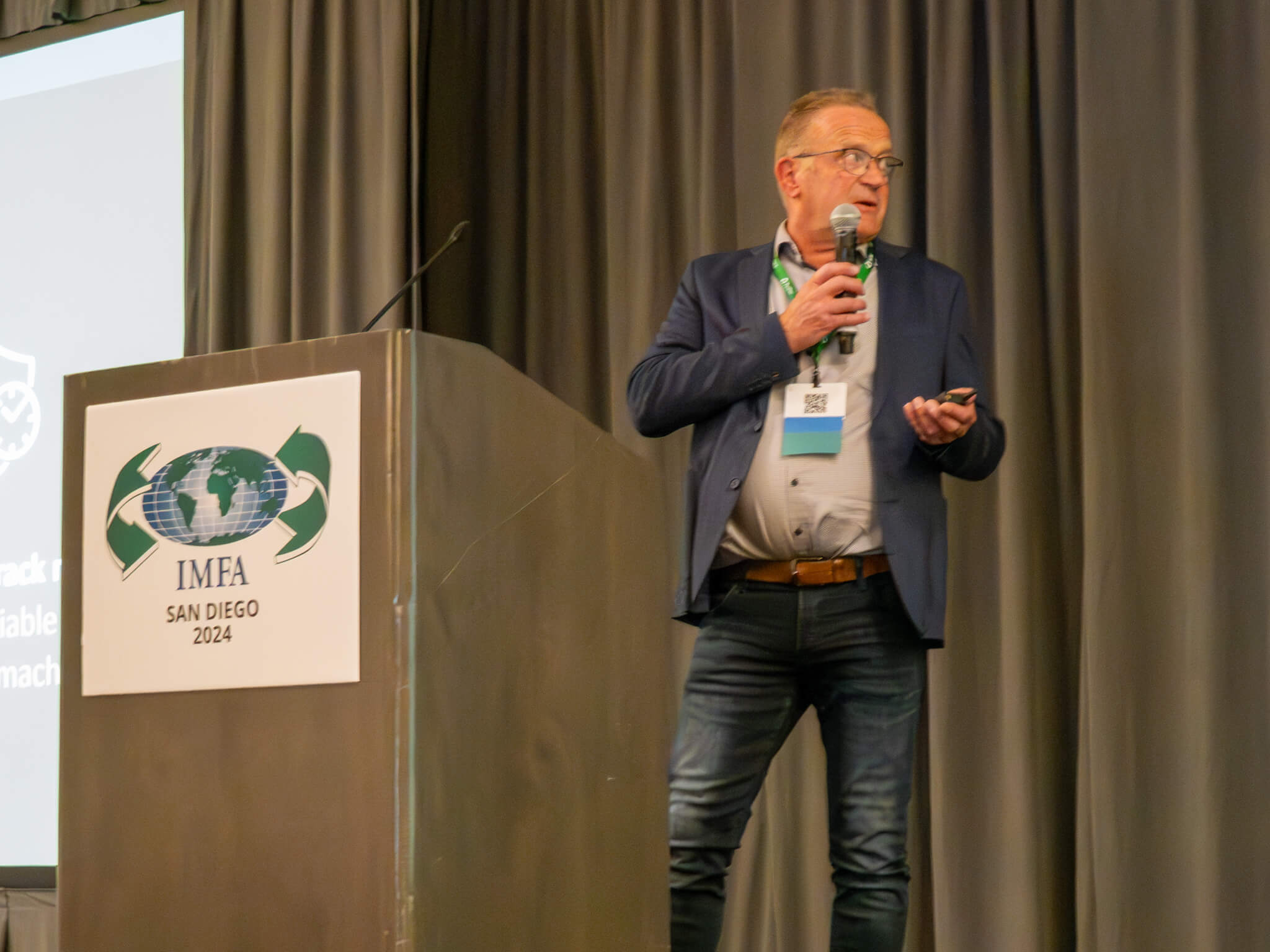
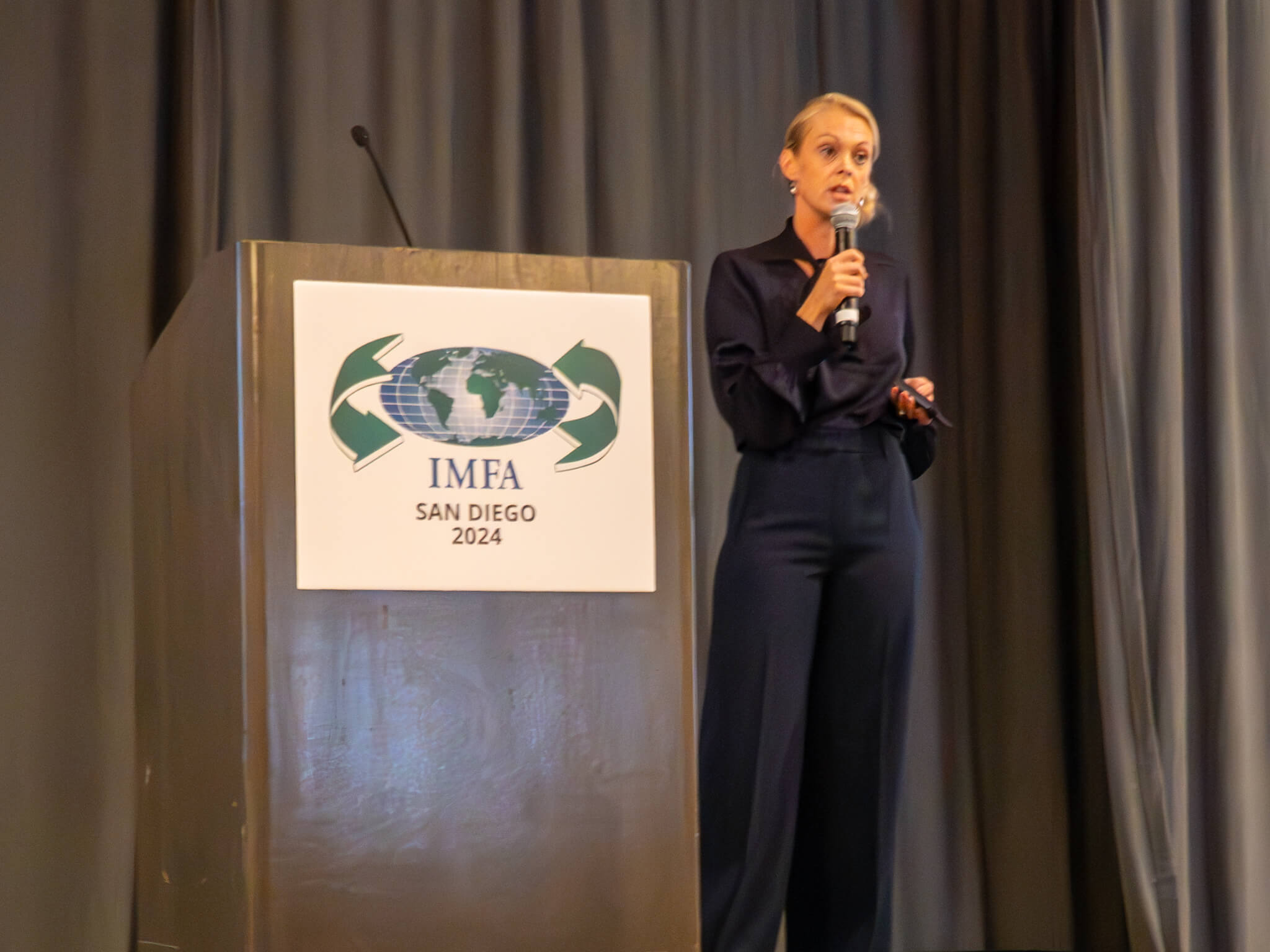
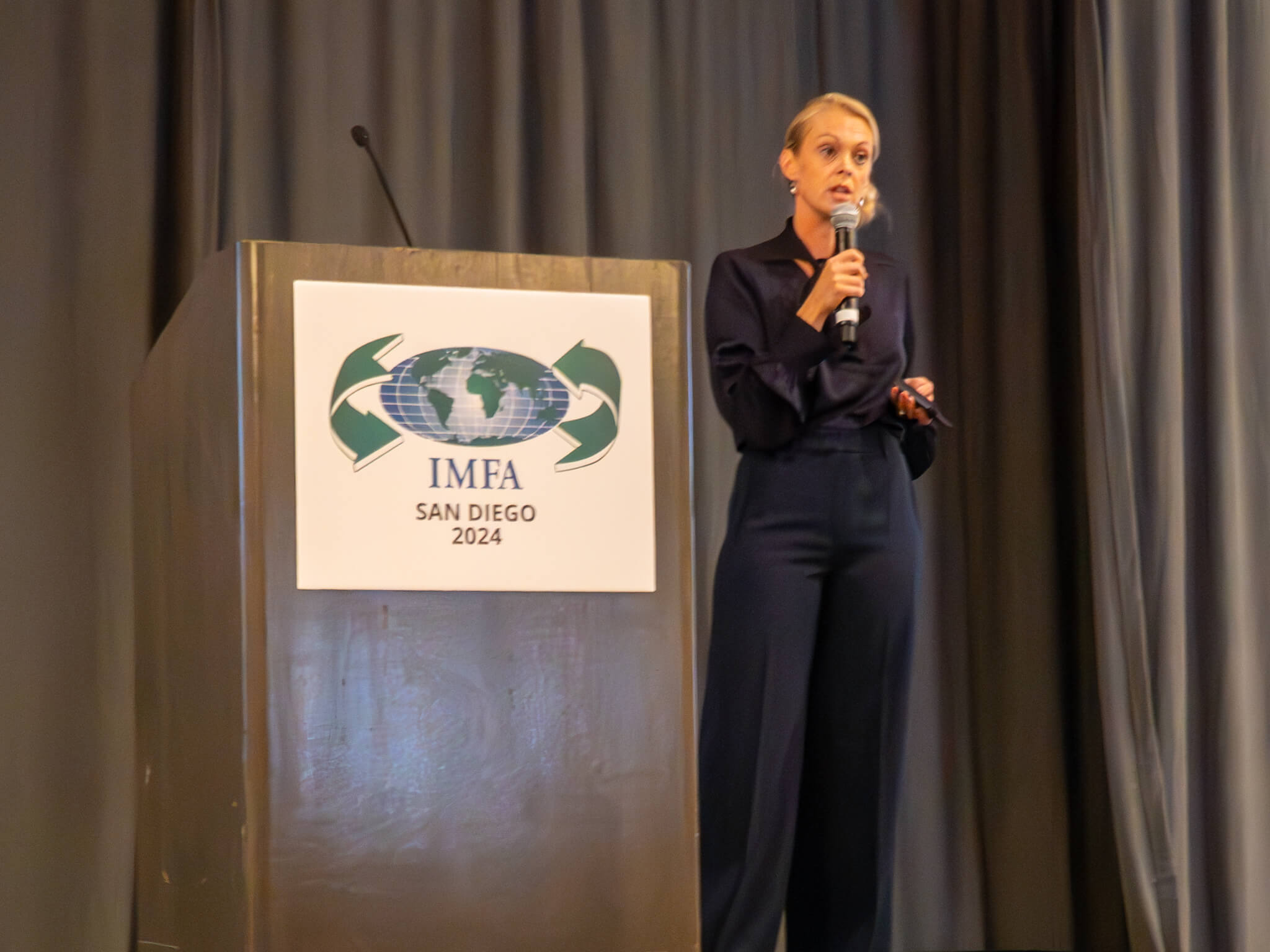
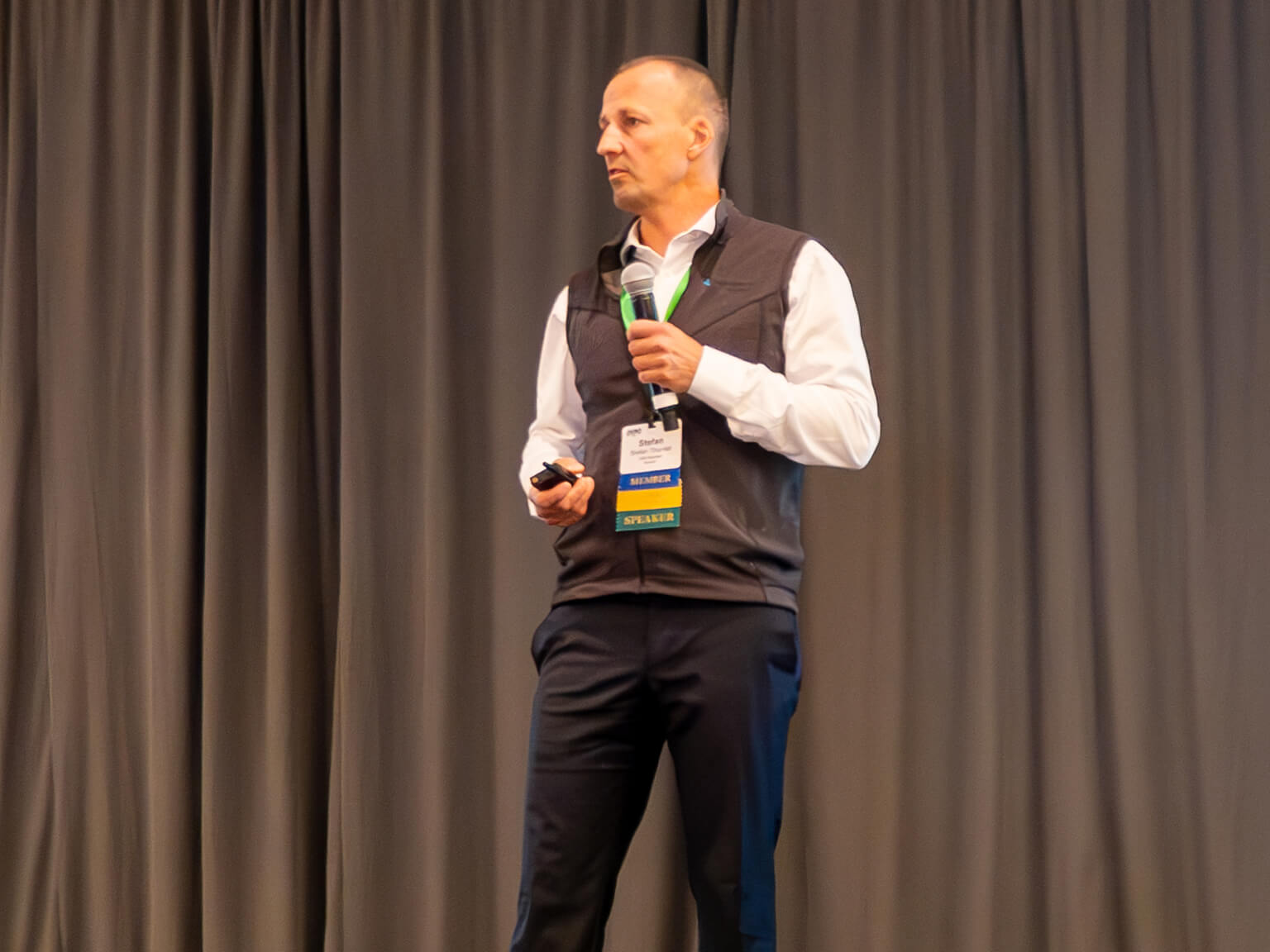
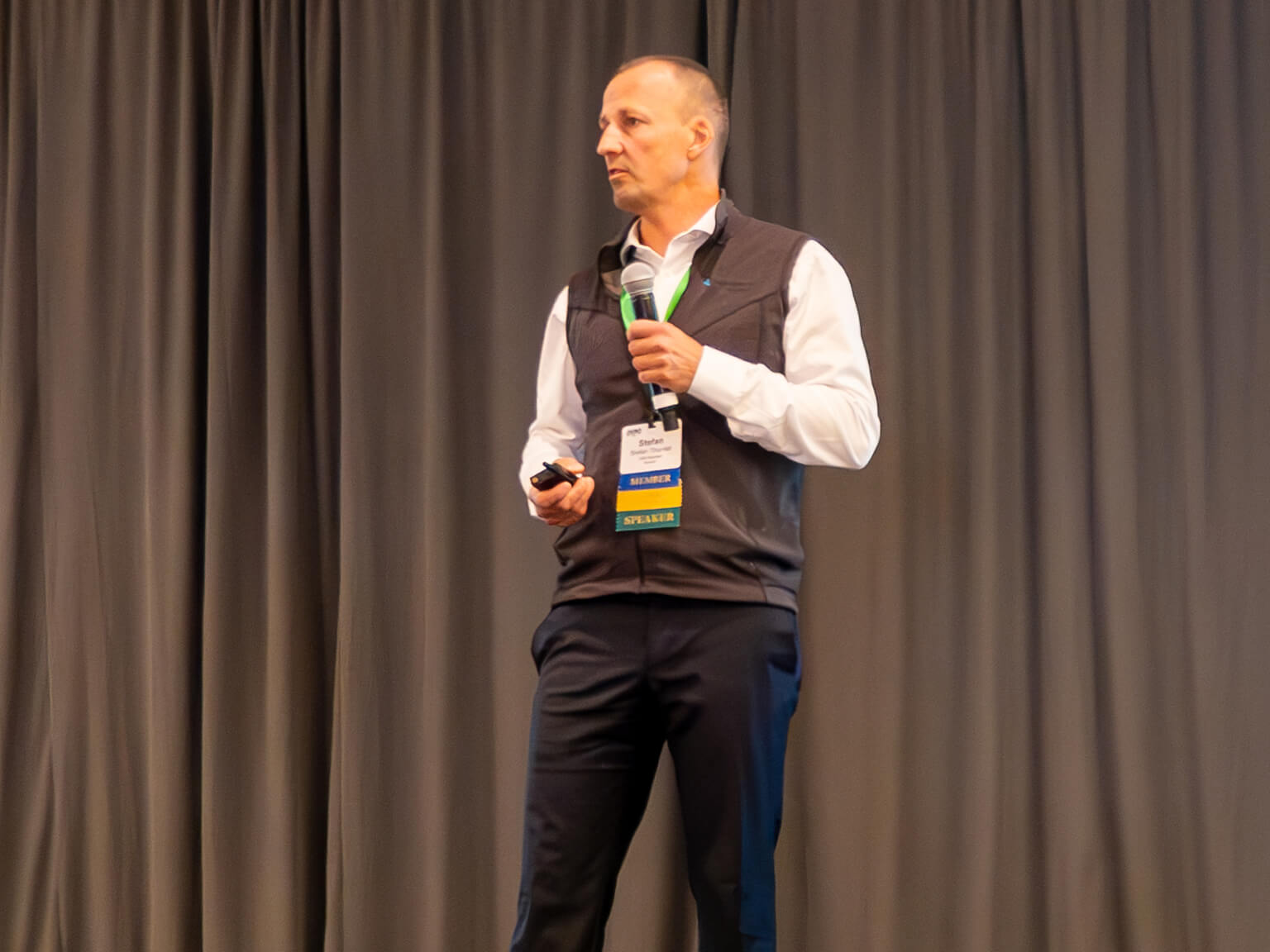
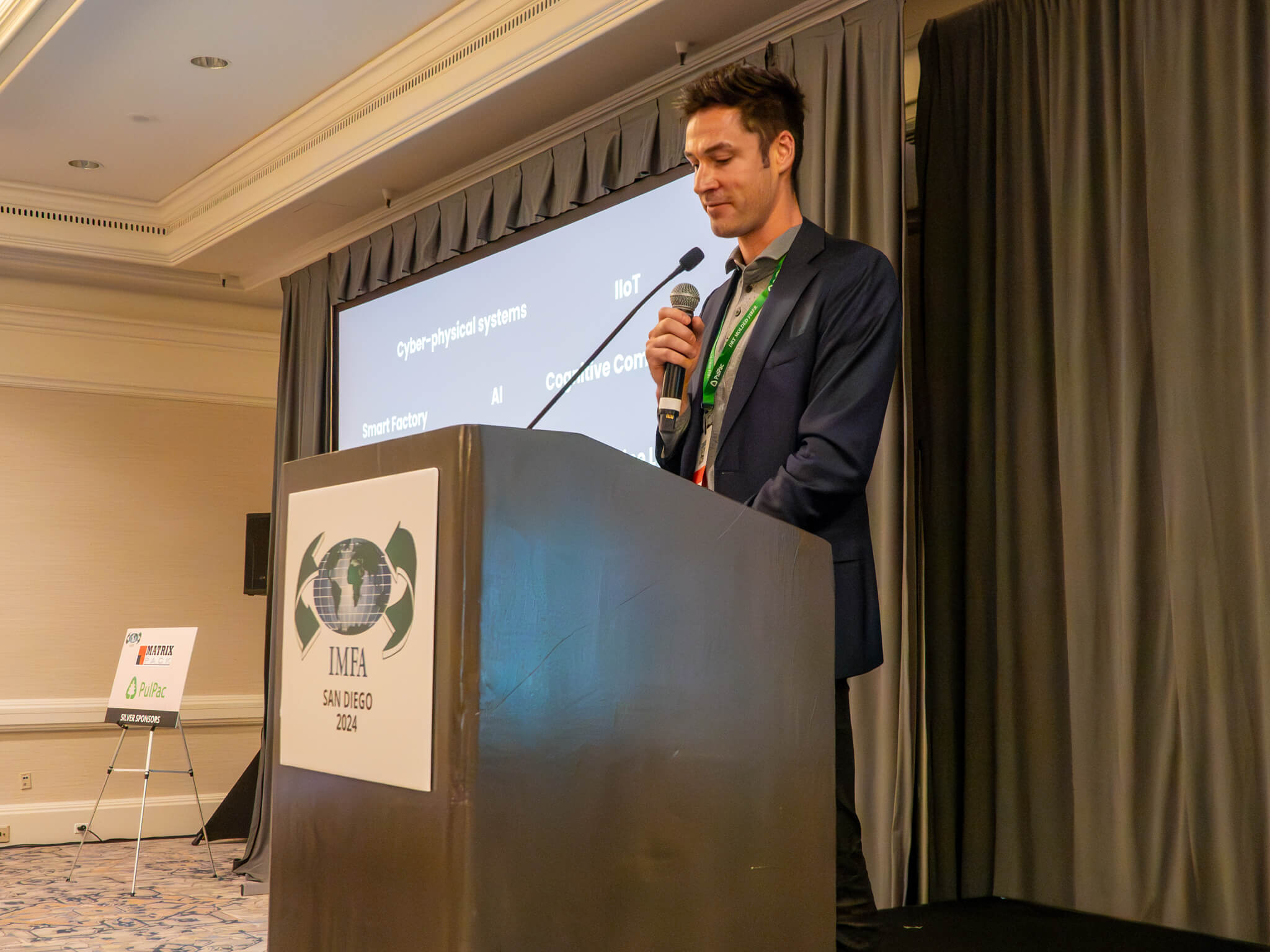
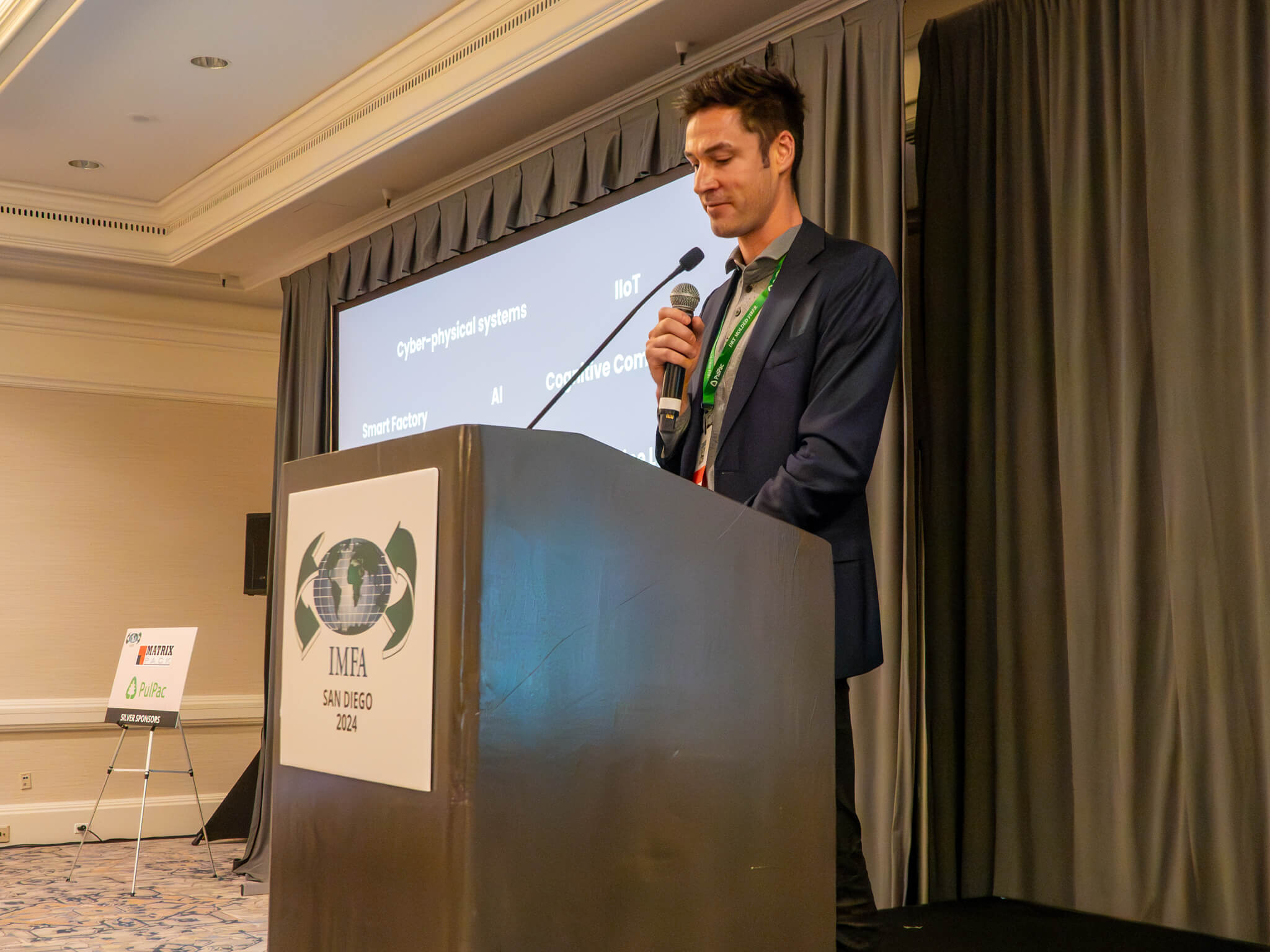
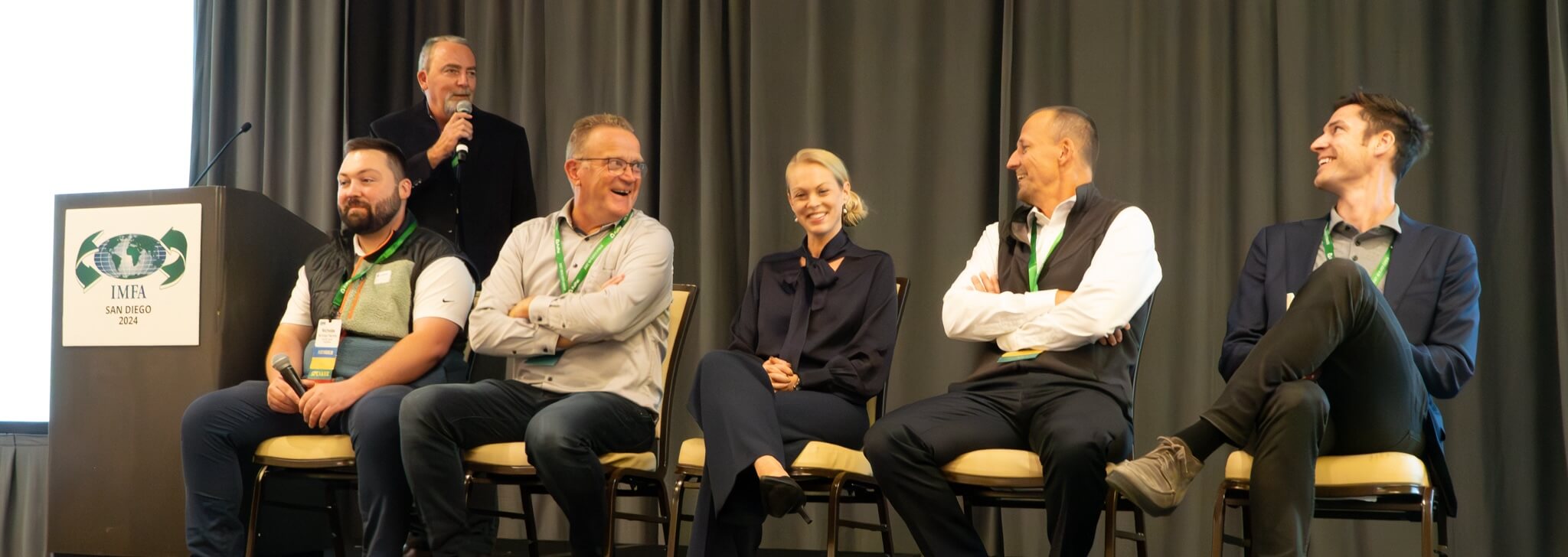
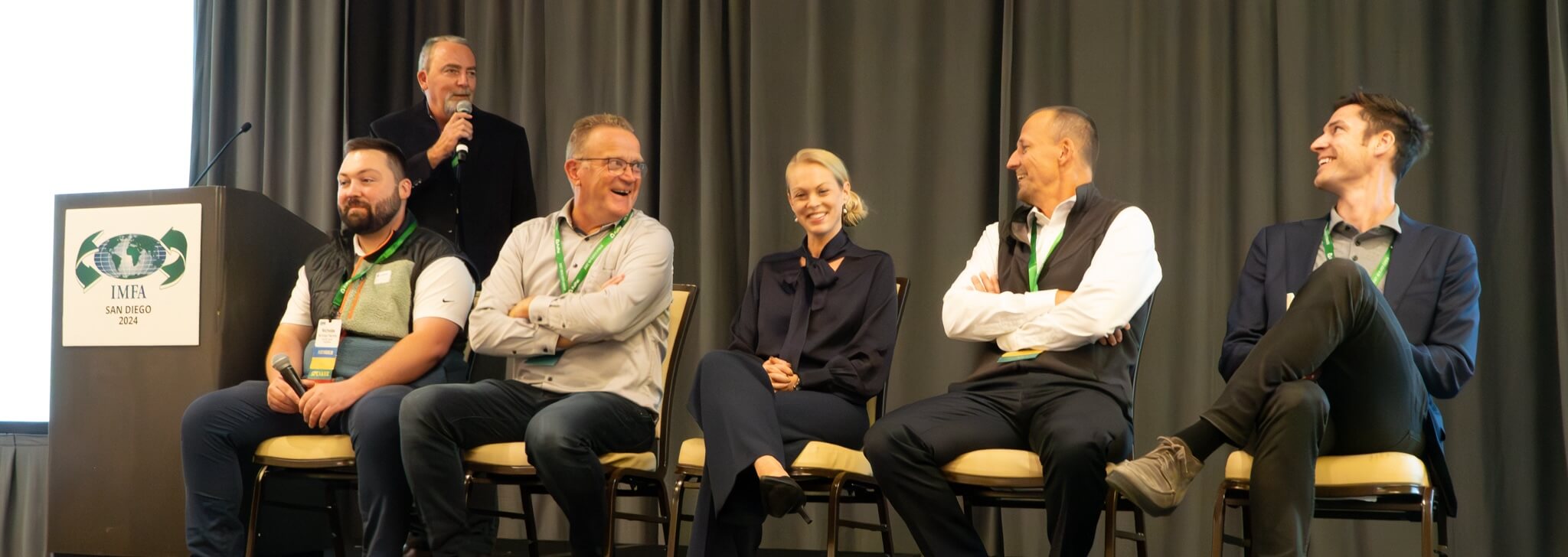
After a packed morning of presentations, we took a well-deserved break for lunch, sponsored by the Matrix Pack Group, before getting back to work for the afternoon.
Kicking off our afternoon sessions, Nicholas Palumbo, North American Technical Sales Manager of the Fiber Division at Kiefel Technologies, explored advanced techniques and materials for optimizing fiber-based products. He detailed innovations in product design, processing methods, and end-of-life solutions, including compostable and recyclable options. Key highlights include the development of multi-stage and laser trimming for increased precision and efficiency, as well as the integration of user-friendly HMI systems for better machine control and process optimization.
Jan Ridderman from Inmaco Solutions discussed their commitment to a plastic-free world through recyclable and compostable molded fiber products. He outlined their process from concept to creation, involving material selection, choosing the appropriate technology (types 1-4), and producing prototype batches. Ridderman also emphasized the importance of understanding the complexities of the production process and showcased a video of Type 2 molded fiber production lines.
Sanna Fager from Pulpac discussed advancements in dry molded fiber technology, focusing on Type 4 molded fiber, with a portfolio of over 300 patents. The dry molded fiber process involves pulping, web milling, molding, and recycling excess materials, utilizing machines like Scala and Modula. Innovations include improved OEE performance, barrier applications via in-line spray, and market validation efforts for products such as hangers, coffee lids, and bottles, including a hot lid pilot at Da Matteo in Gothenburg.
Stefan Thundal from AIM Sweden, a 3D printing company founded in 2016, highlighted their focus on sustainability and their diverse target markets, including orthopedic implants and molded fiber. They enhance molded fiber production efficiency through innovative tooling, such as FreeFlow forming tools with titanium skins, and are developing optimized pressing tools to improve thermal effectiveness. Their unique IP and 3D printing capabilities provide significant design freedom, though some tools are still in the testing and development phases.
Ben Wearing, General Manager of Operations Feedback Systems (OFS) North America, highlighted the transformative impact of Industry 4.0 on the molded fiber industry. By leveraging advanced technology, manufacturers can enhance human roles, boost output, and minimize downtime, as demonstrated by significant improvements in production efficiency and operator empowerment. Key results include better loss time comprehension, machine capacity insights, and accurate output visibility, all achieved in just a few hours of system implementation.
After hearing each of these presenters speak to their specialties, we brought them all together for a Q&A panel moderated by Gary Visser, with Paul Carter and Mike Gallant assisting from the audience. This discussion provided insights into advancements in molded fiber technology, exploring topics from product design and processing innovations to sustainability and Industry 4.0 impacts. Thank you to our breakout sponsor, Kemira, for sponsoring today’s panel.
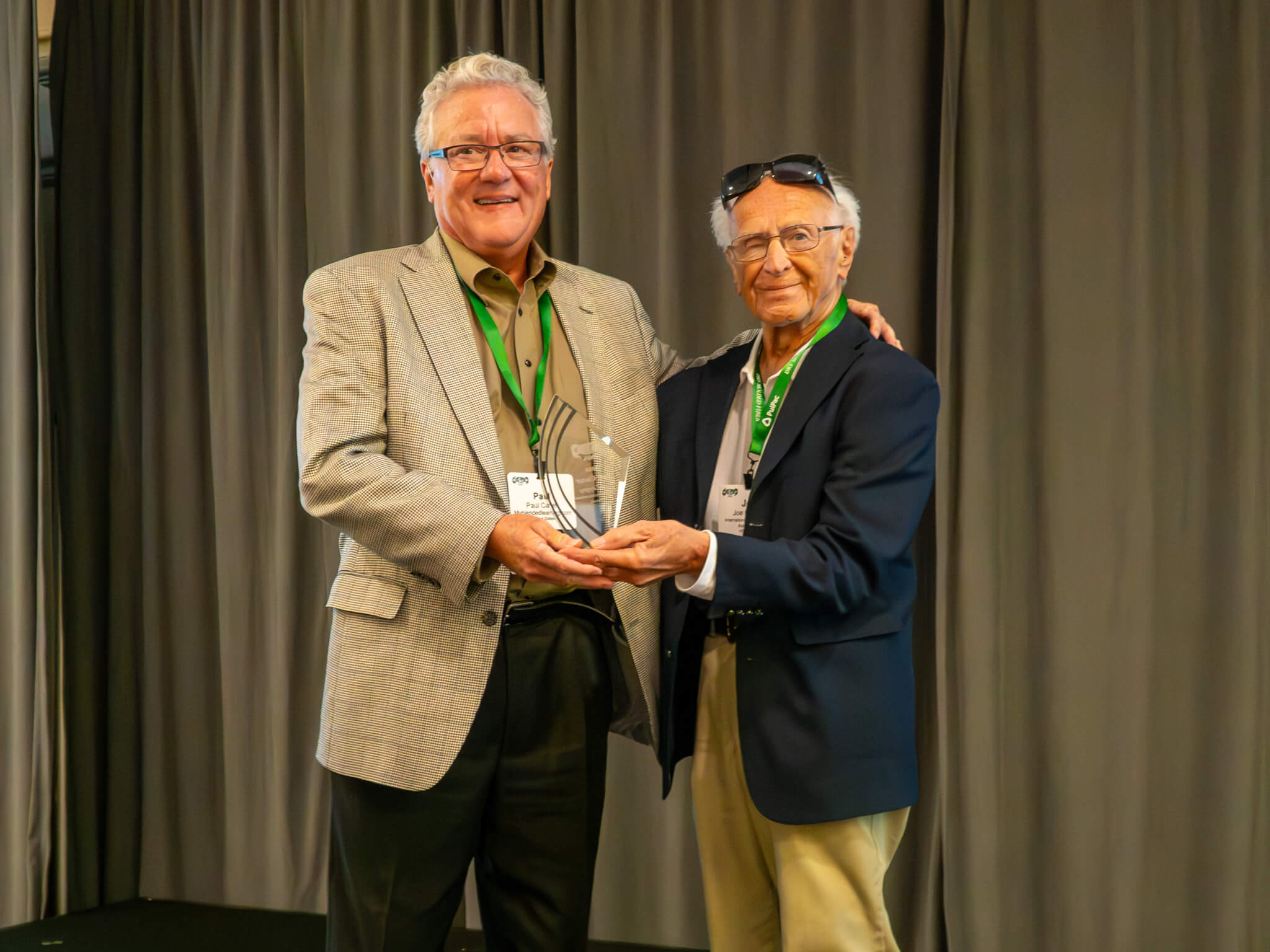
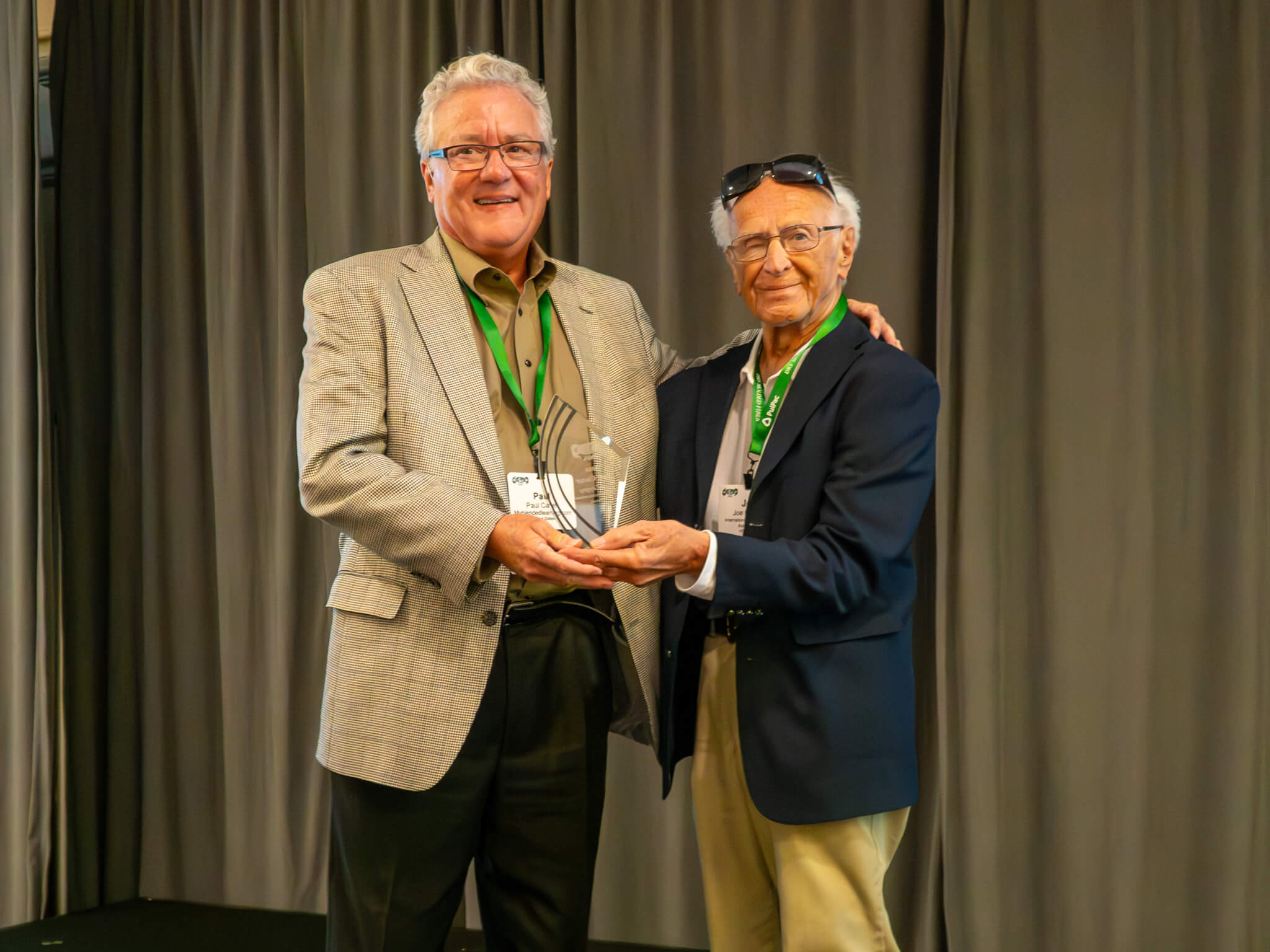
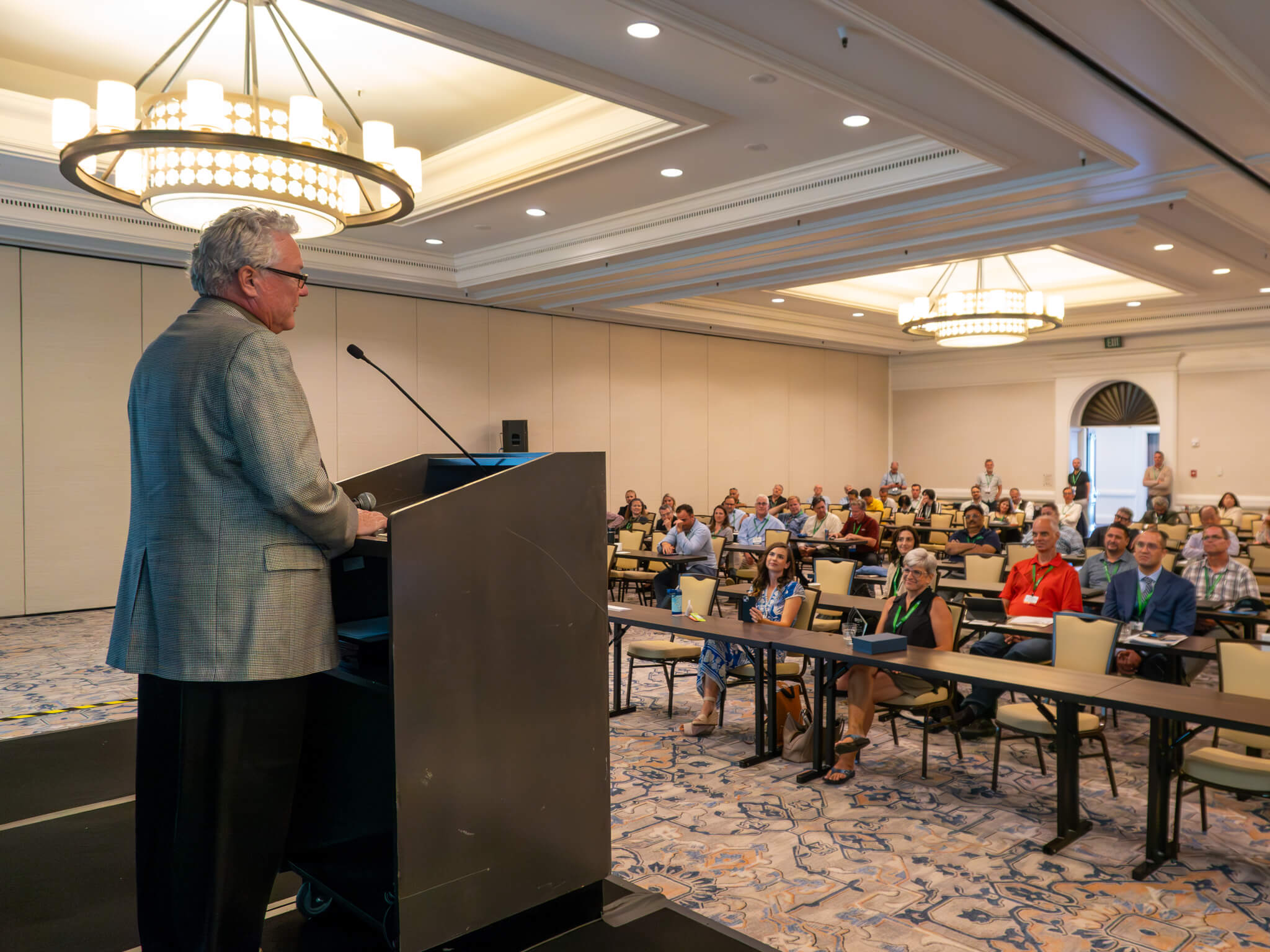
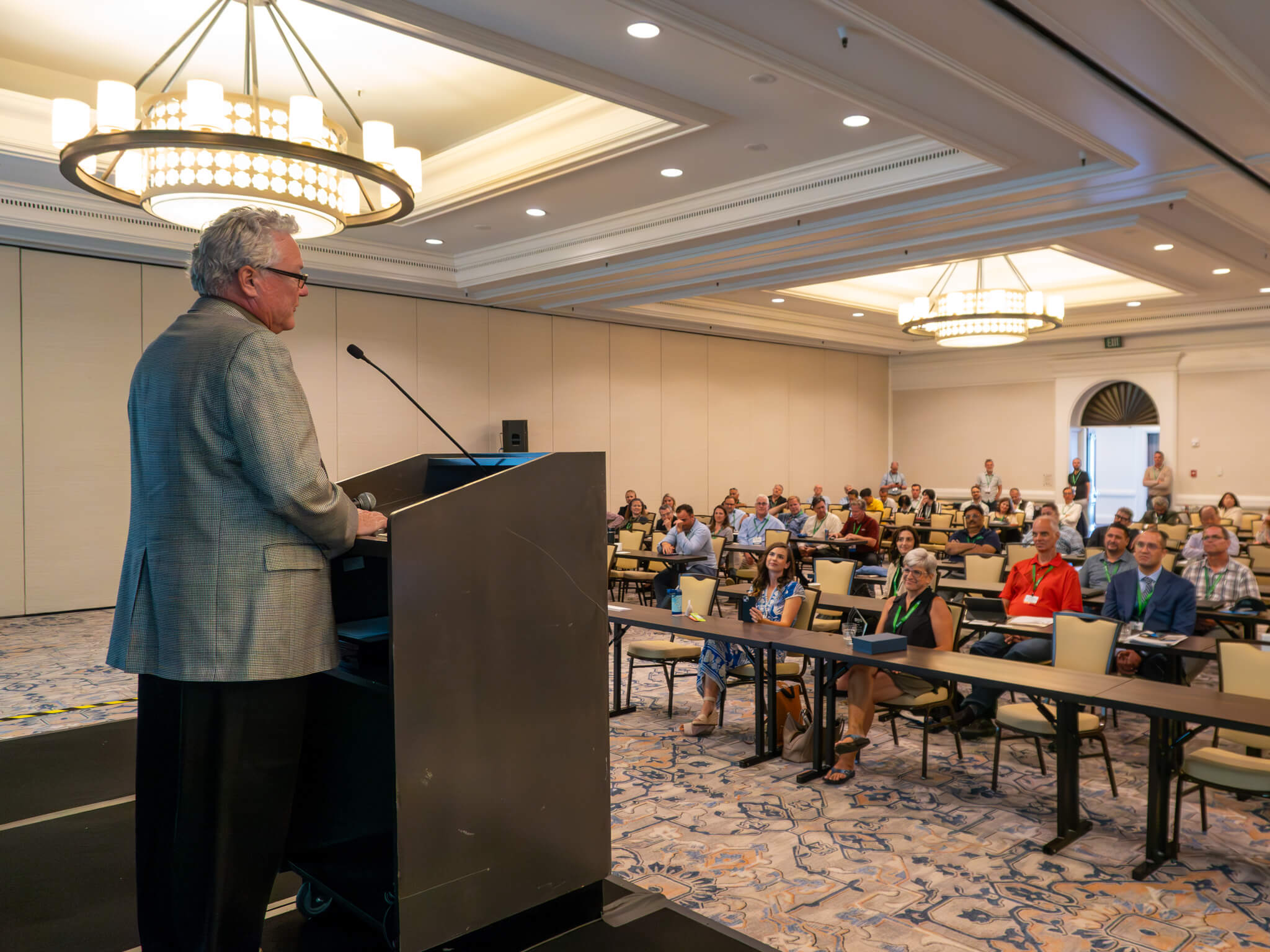
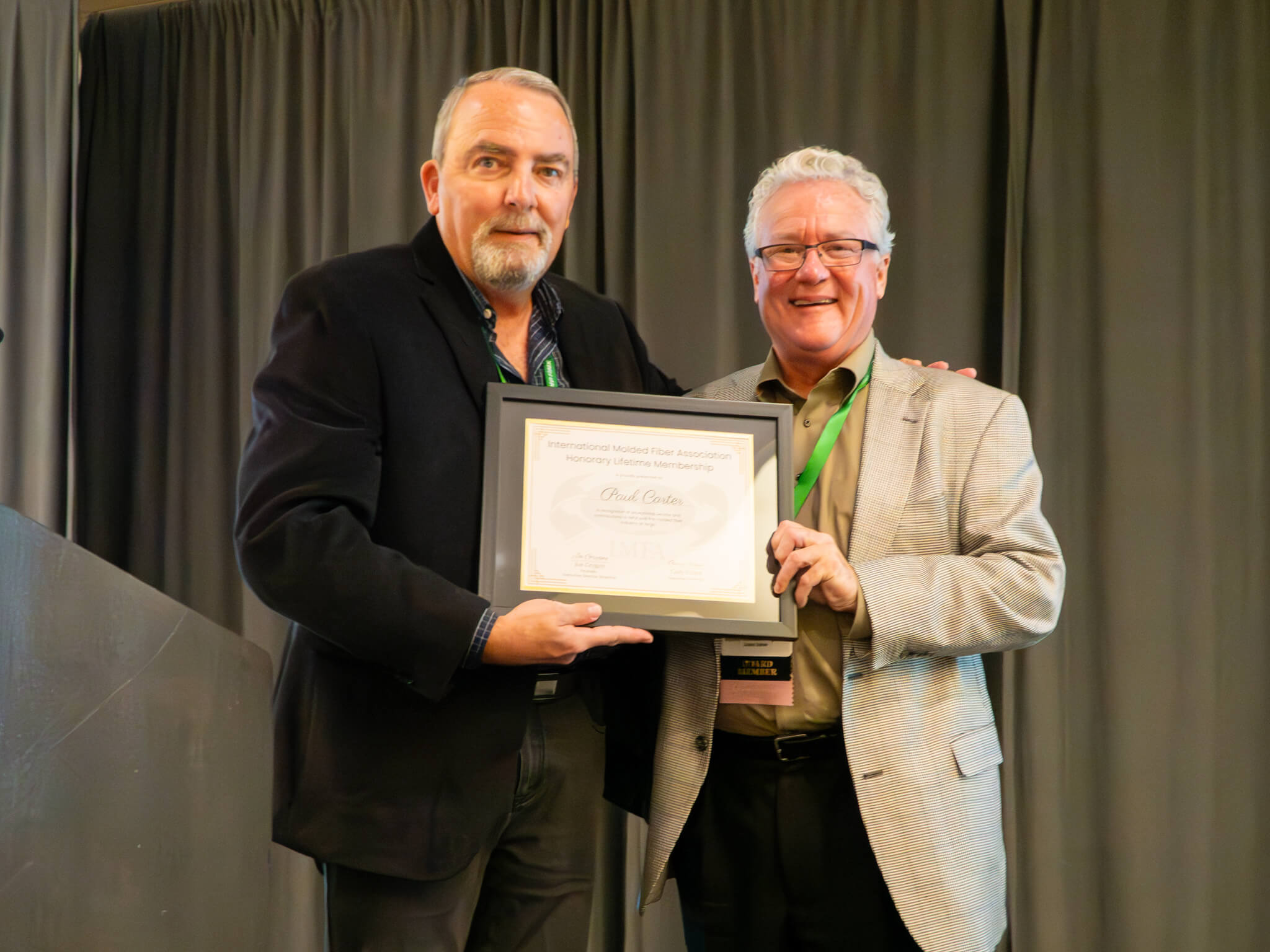
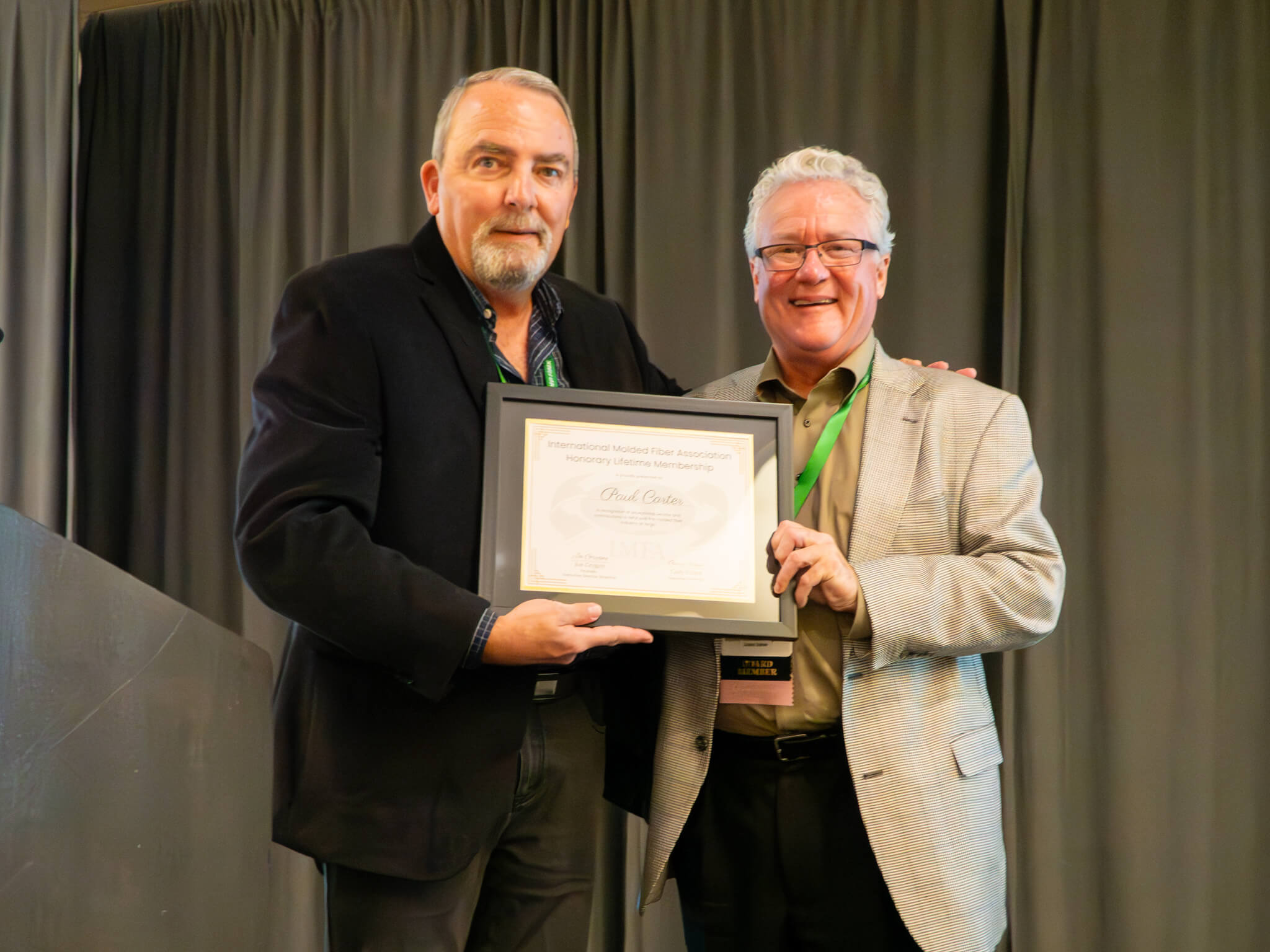
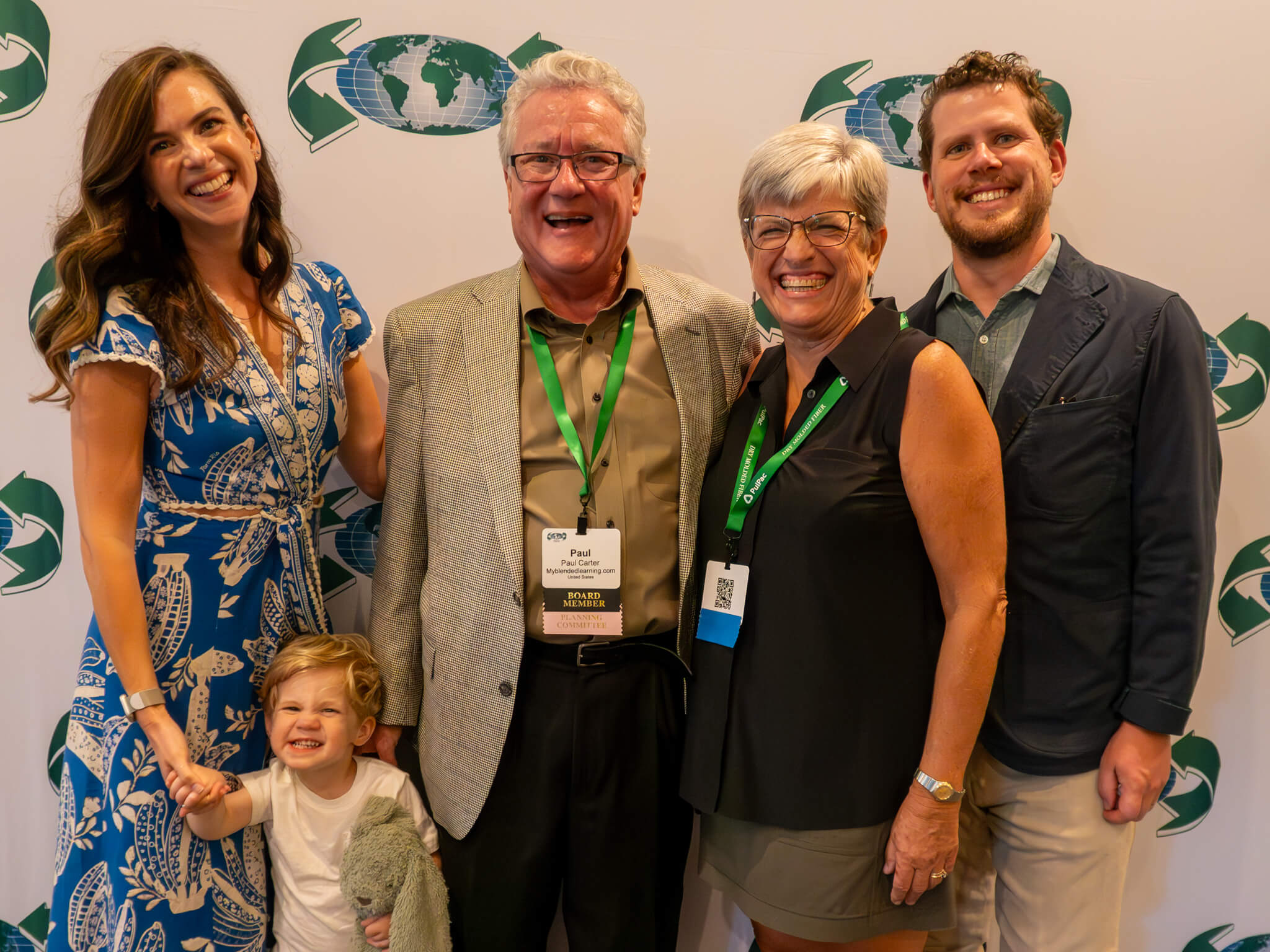
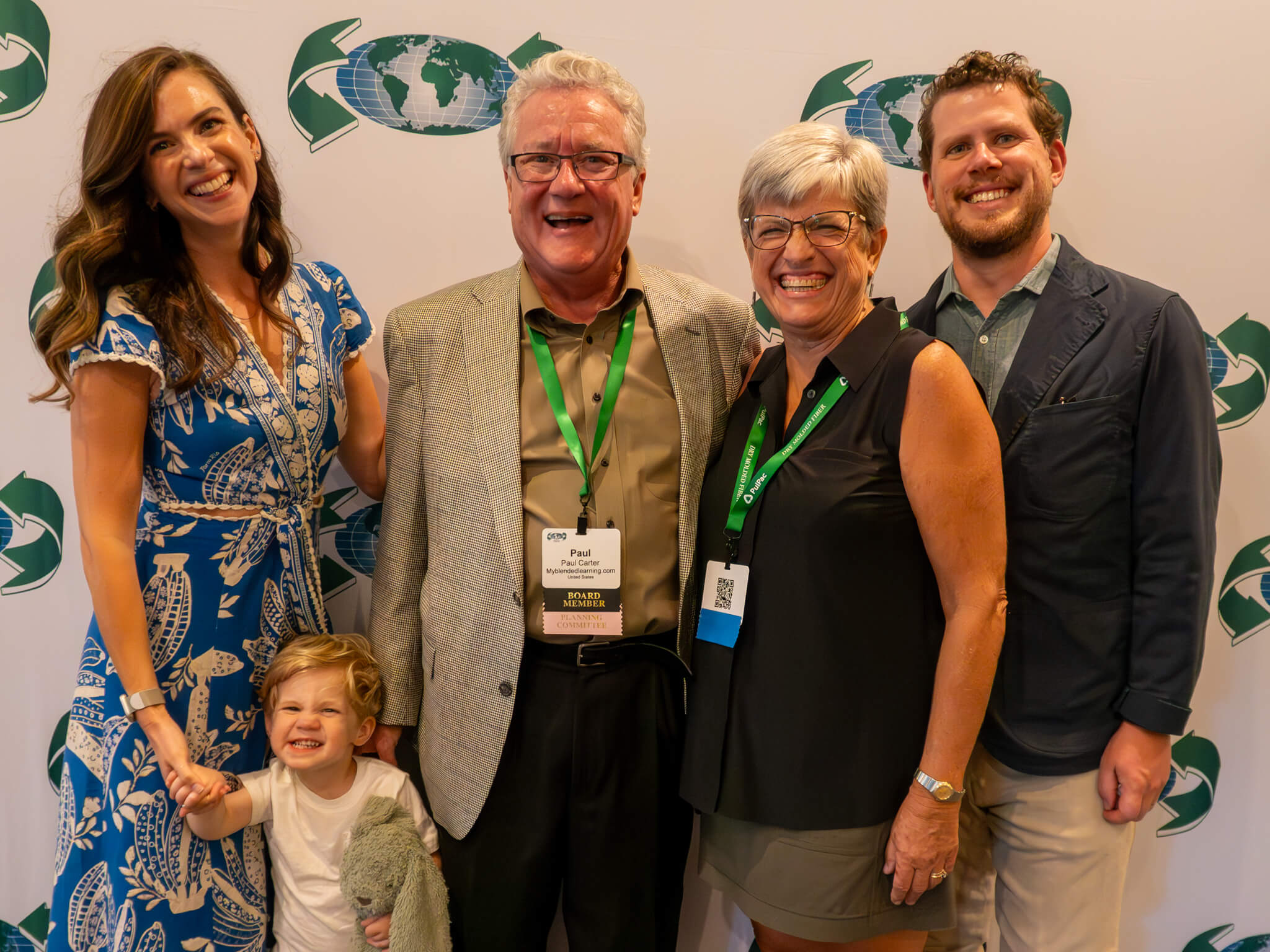
We closed our sessions on Thursday with a memorable awards ceremony where Paul Carter was honored with the Joe Grygny Lifetime Achievement Award for his dedication to advancing the molded fiber industry through innovative product and process development. The ceremony also recognized past and future recipients with honorary lifetime memberships, celebrating their contributions and ongoing commitment to the legacy of Joe Grygny and the growth of molded fiber technology.
Click here to read the full blog detailing Paul's accomplishments and contributions to our industry – it's a great article that shares some insight into a truly incredible person who we are lucky to call a colleague and friend. Thank you to our partner AIM Sweeden for sponsoring this award ceremony.
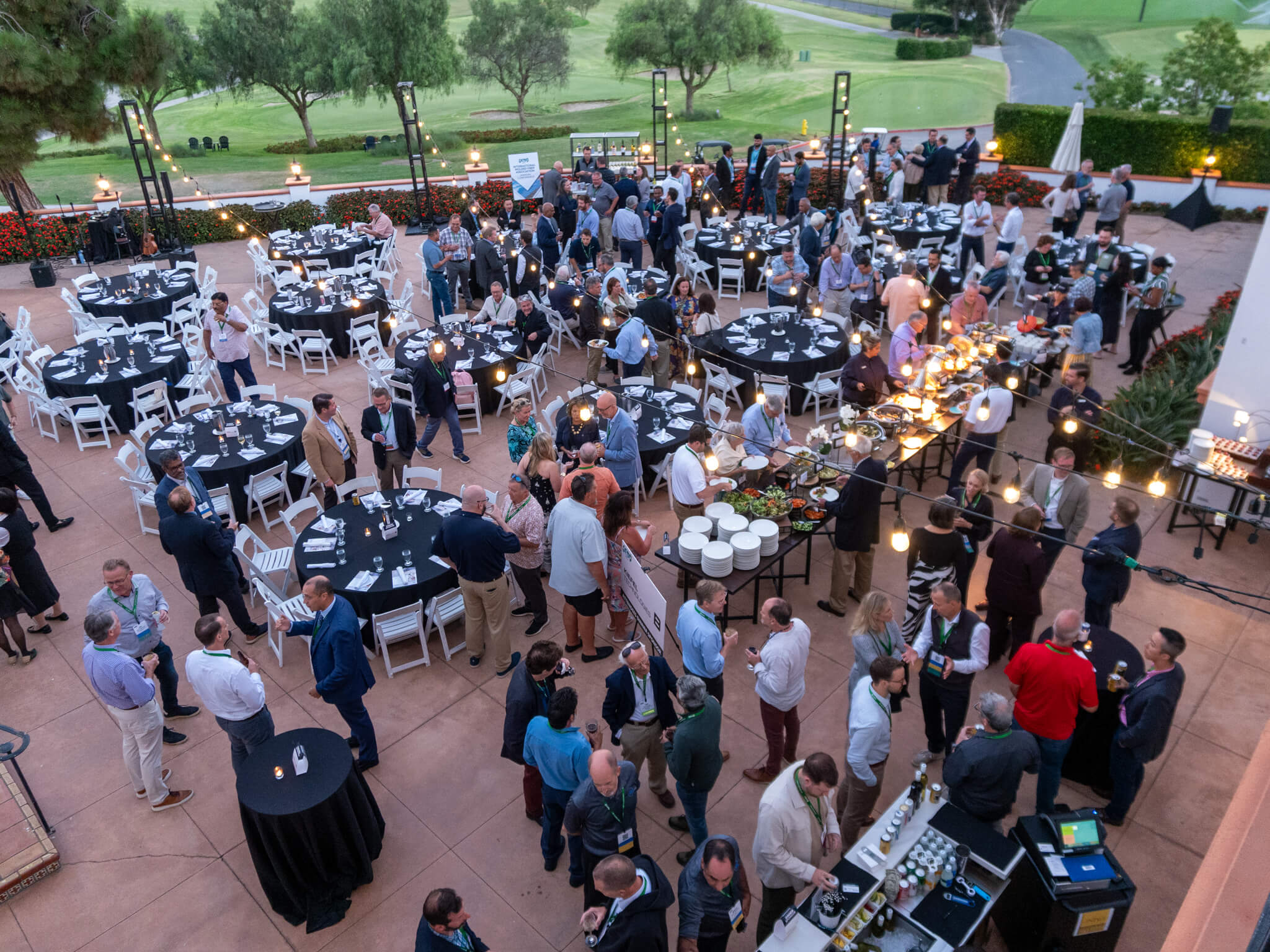
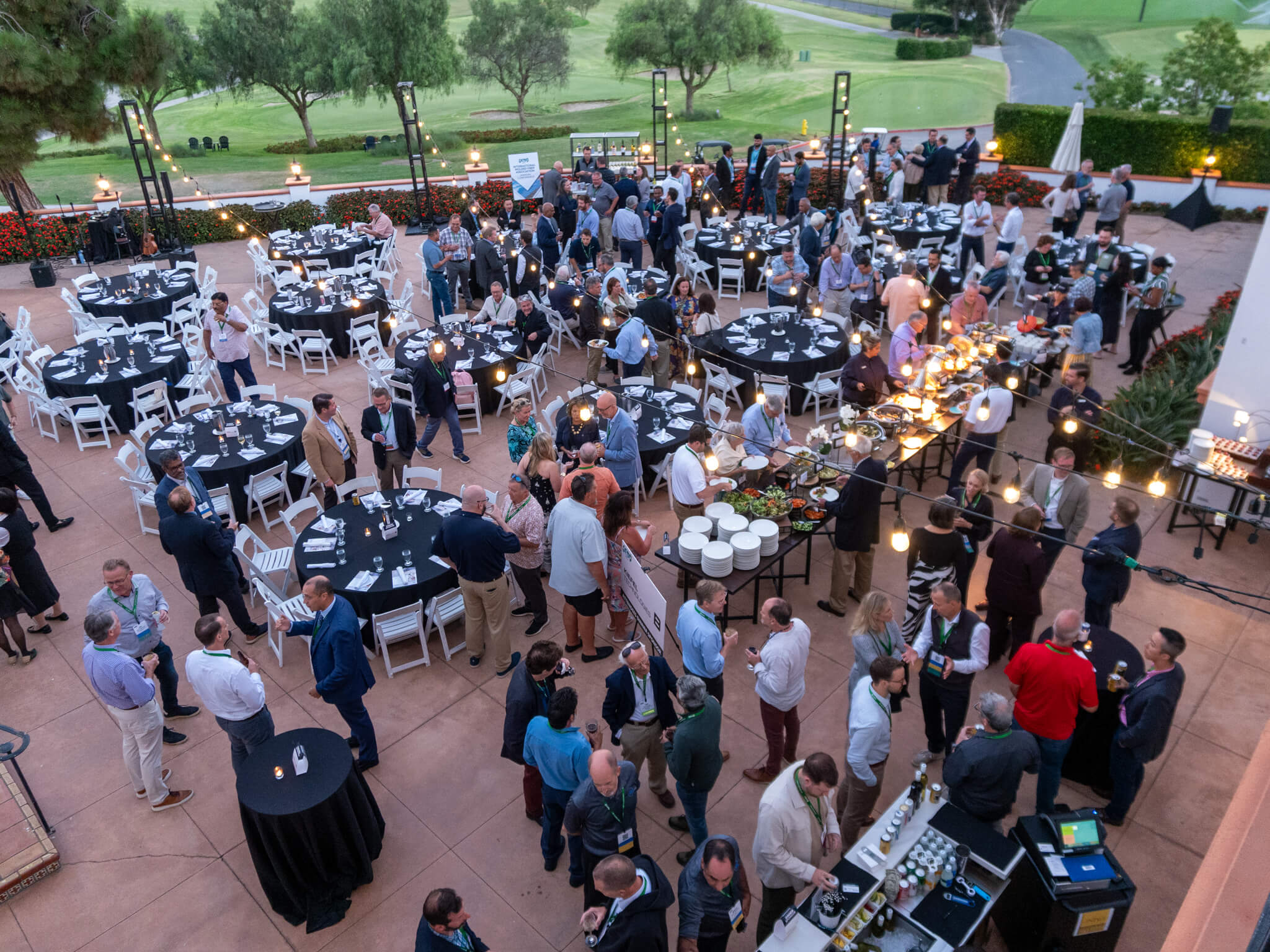
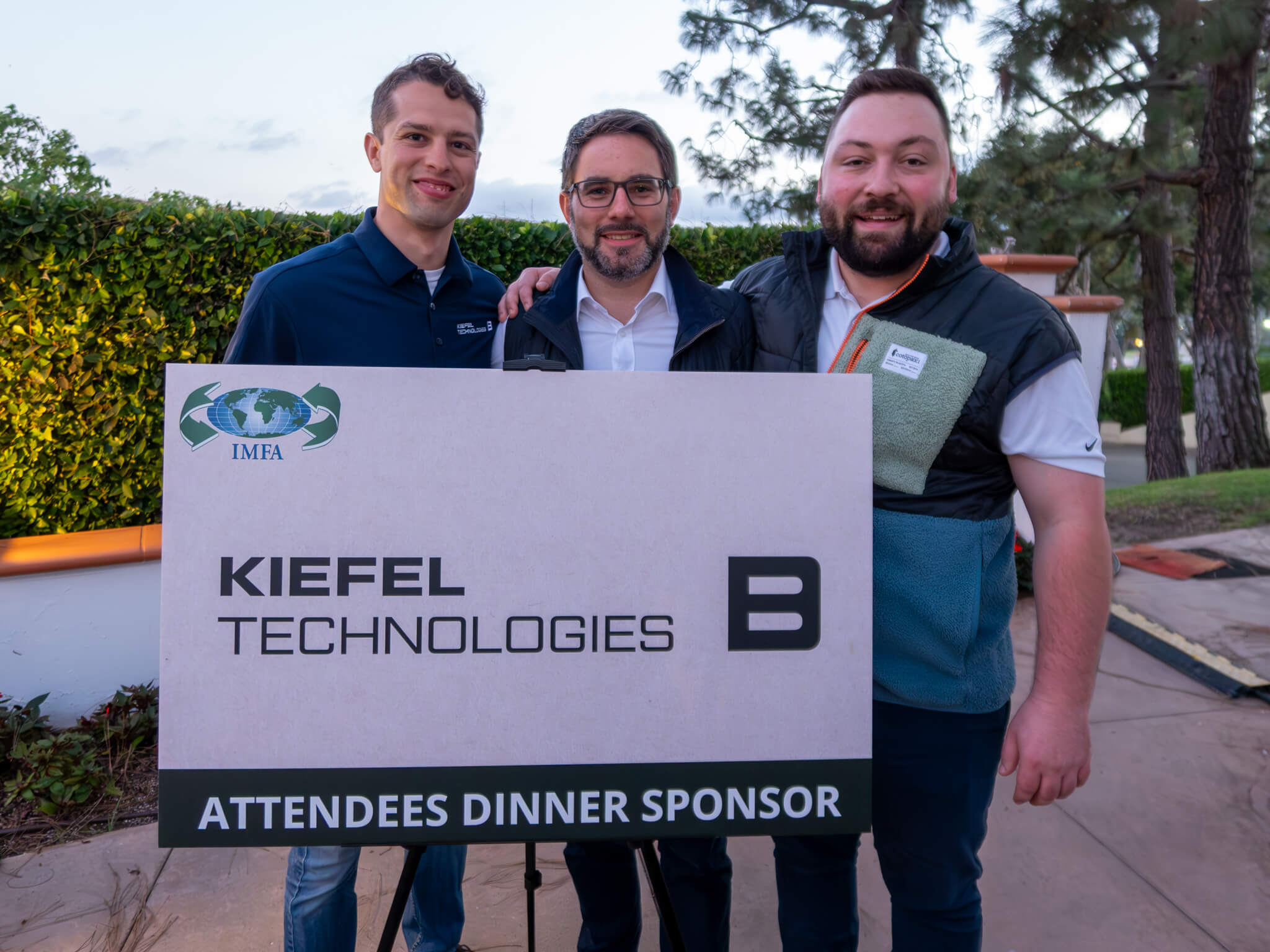
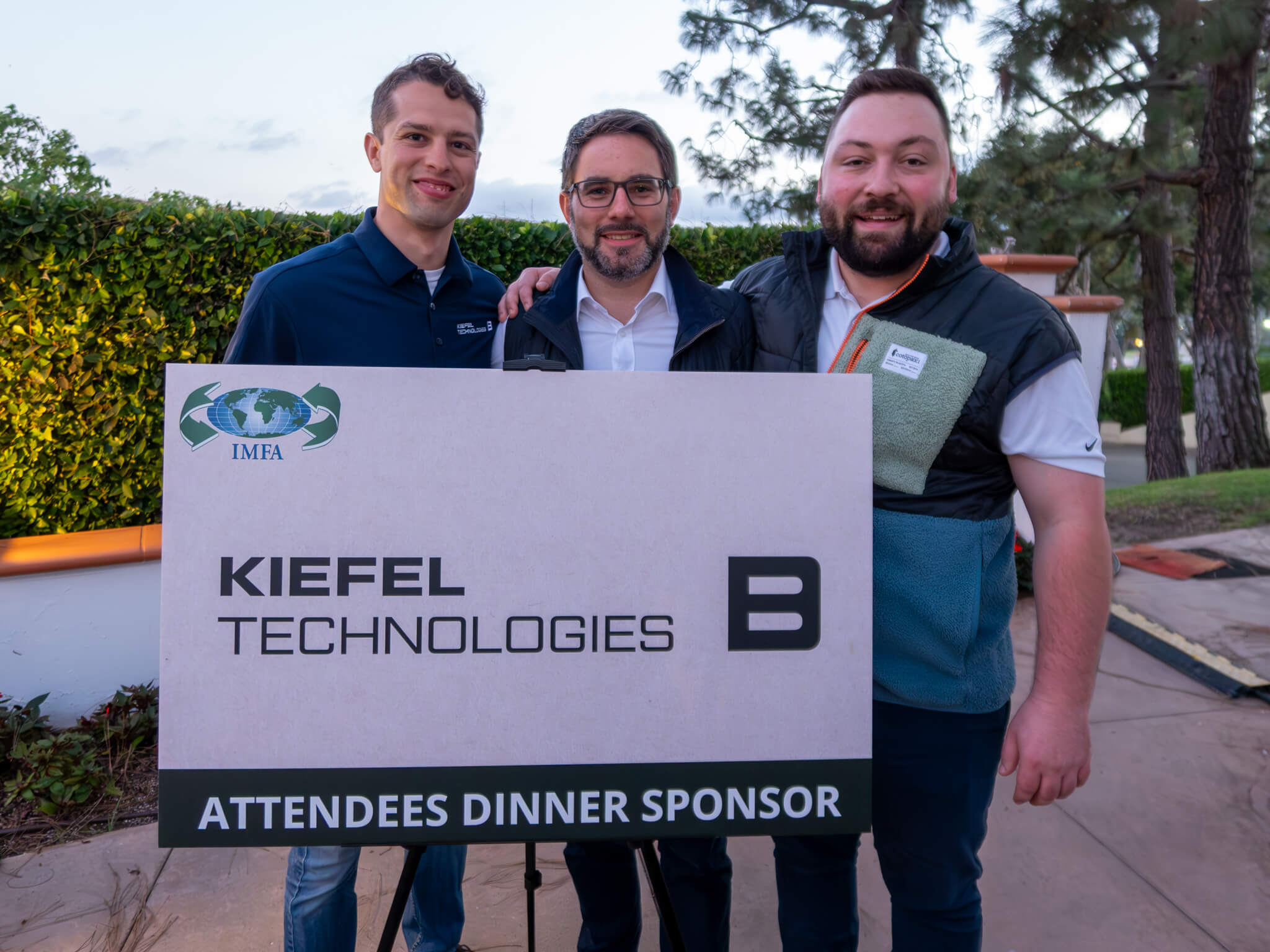
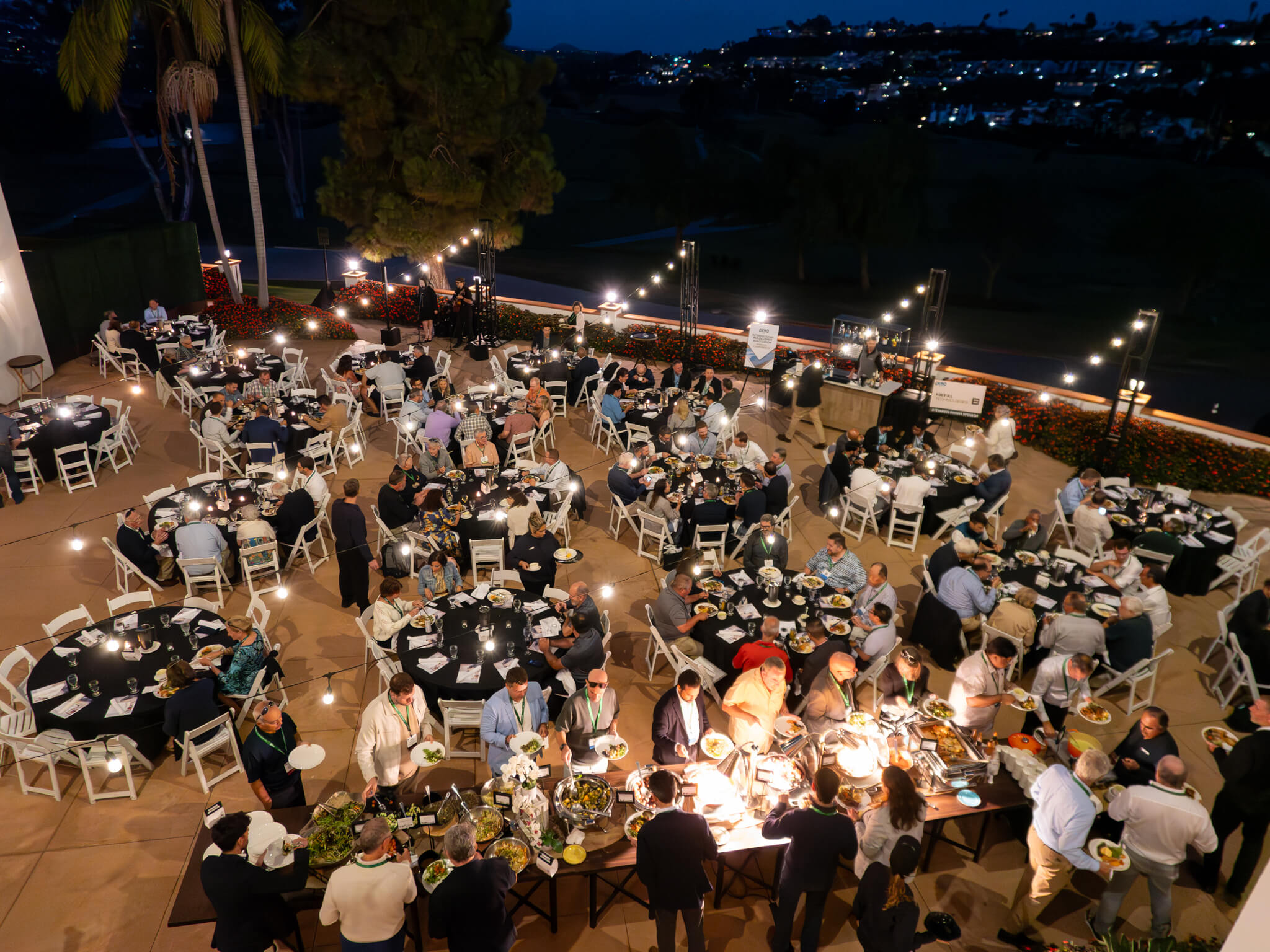
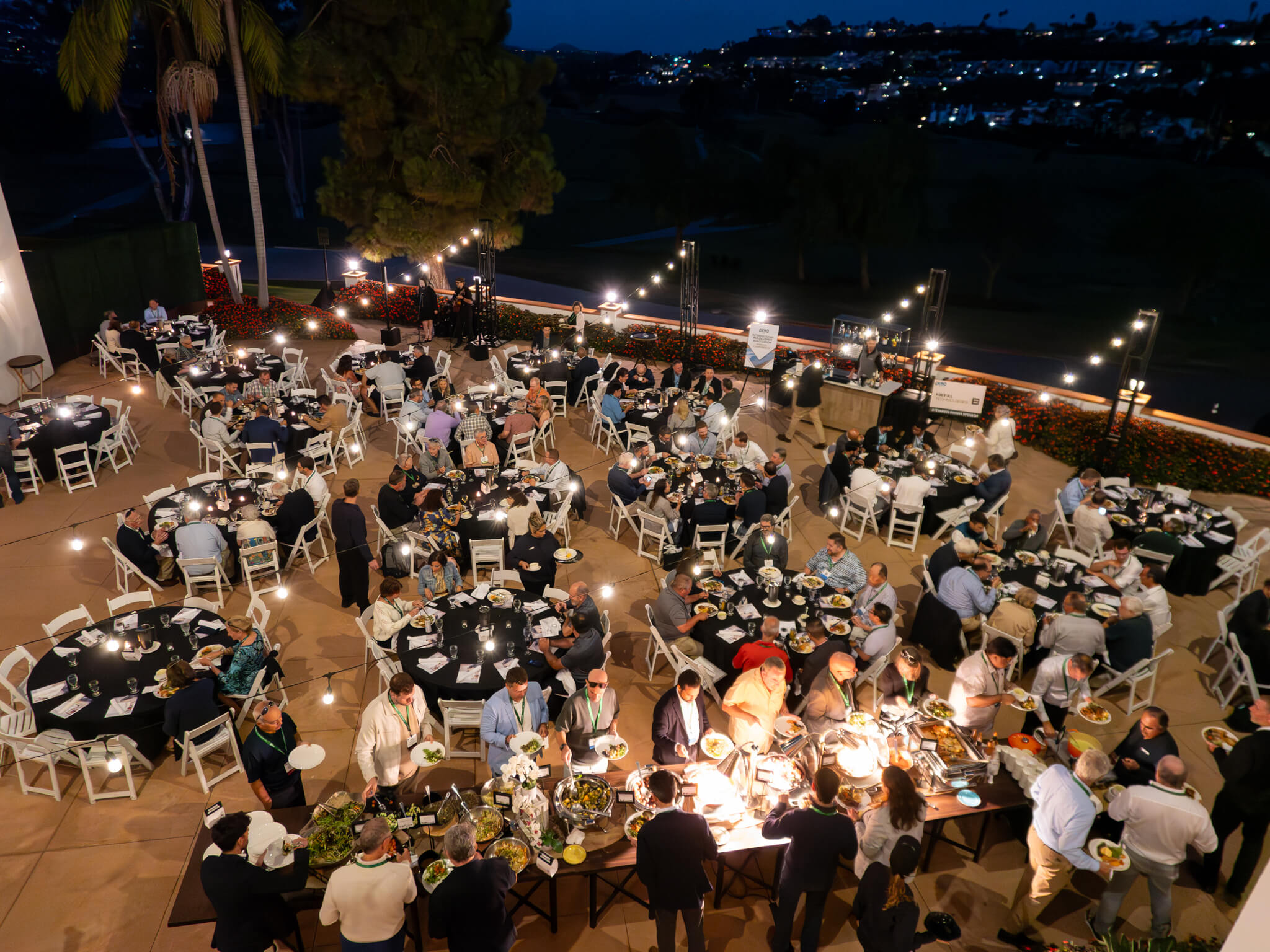
Back again by popular demand, we gathered for dinner with great food and better company. As natural competitors, we’re always so grateful for the friendship and camaraderie that comes whenever we gather in association. Thank you once again Nicholas Palumbo and the team at KIEFEL for picking up the tab on our meal!
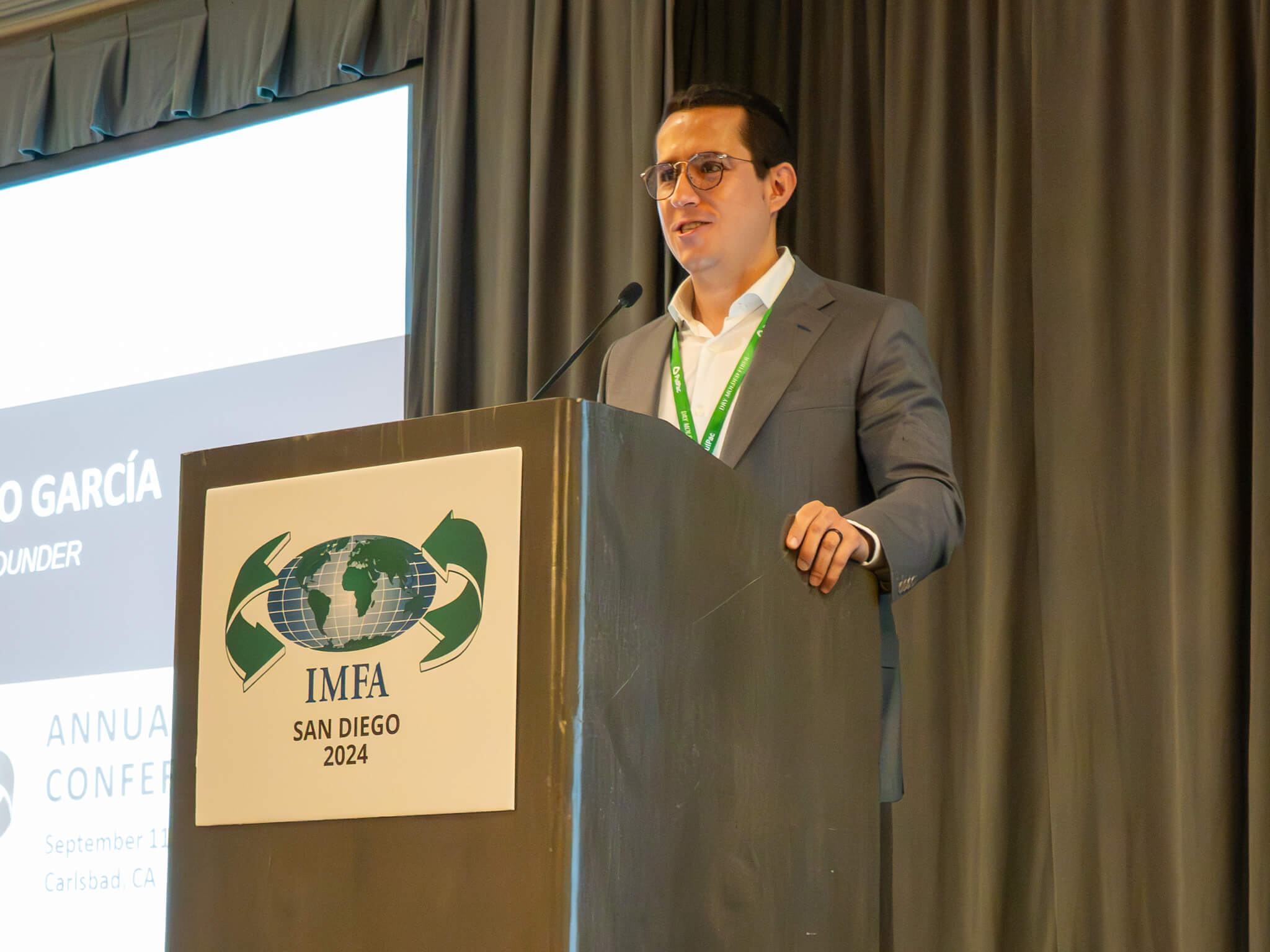
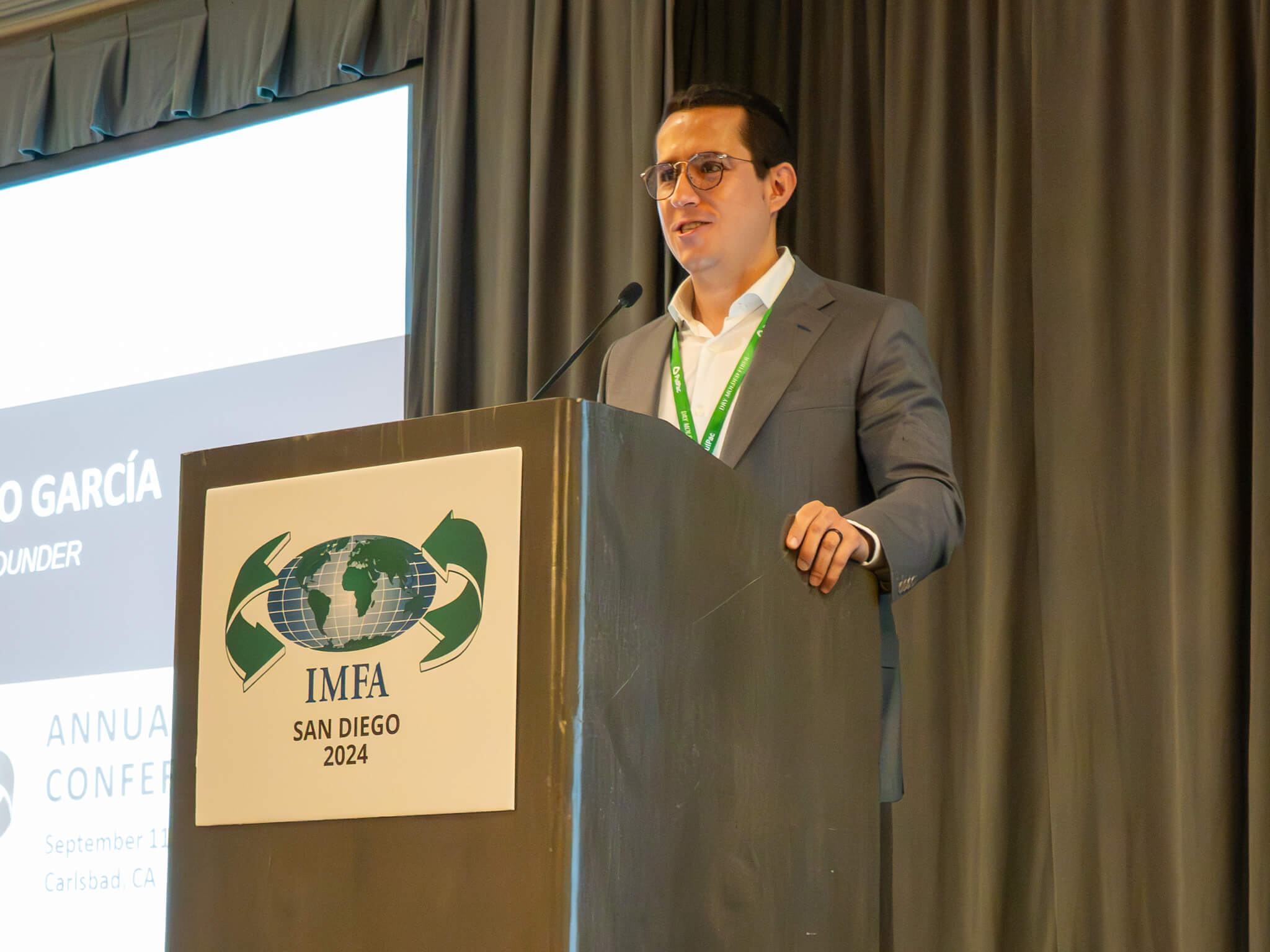
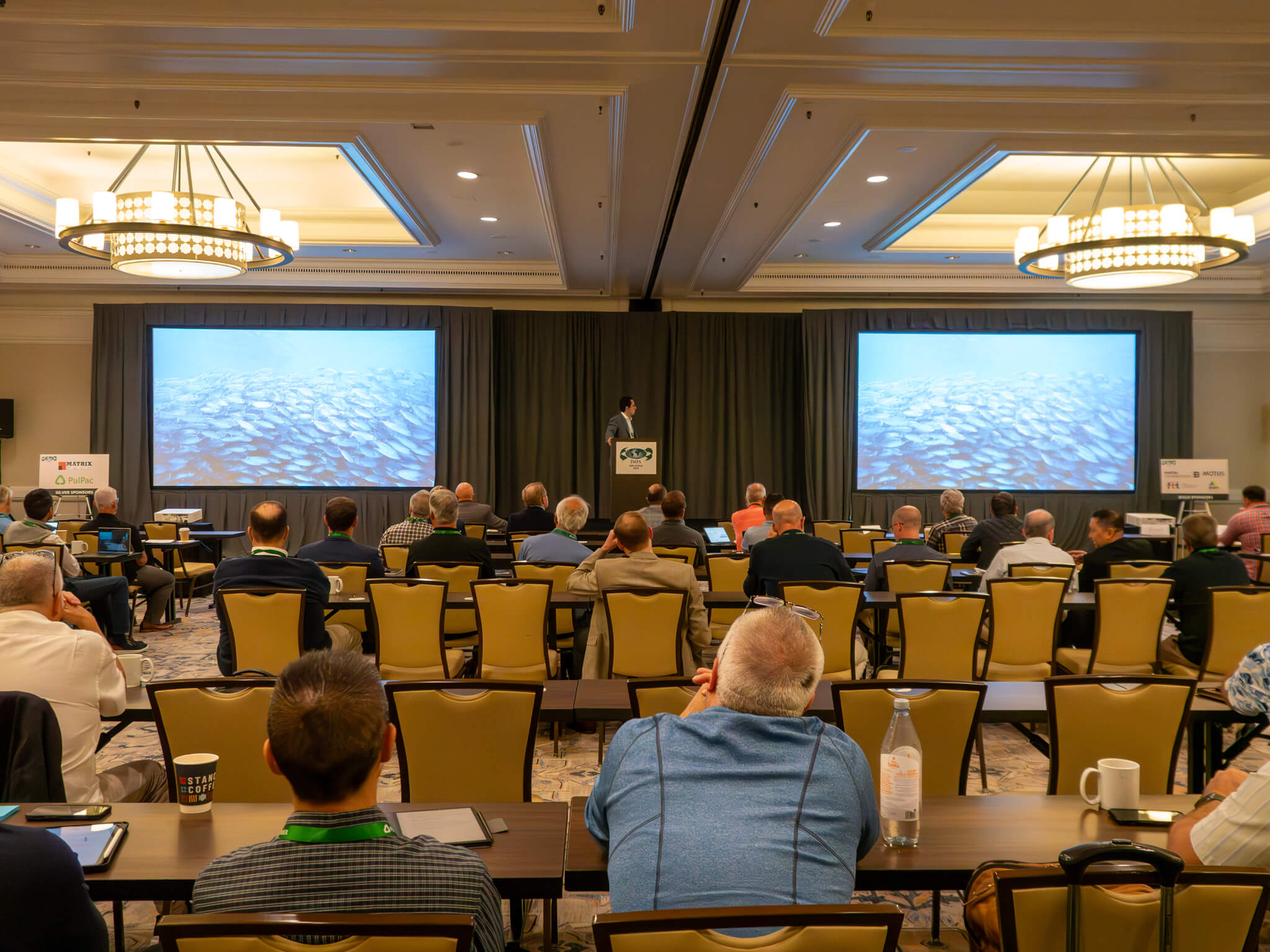
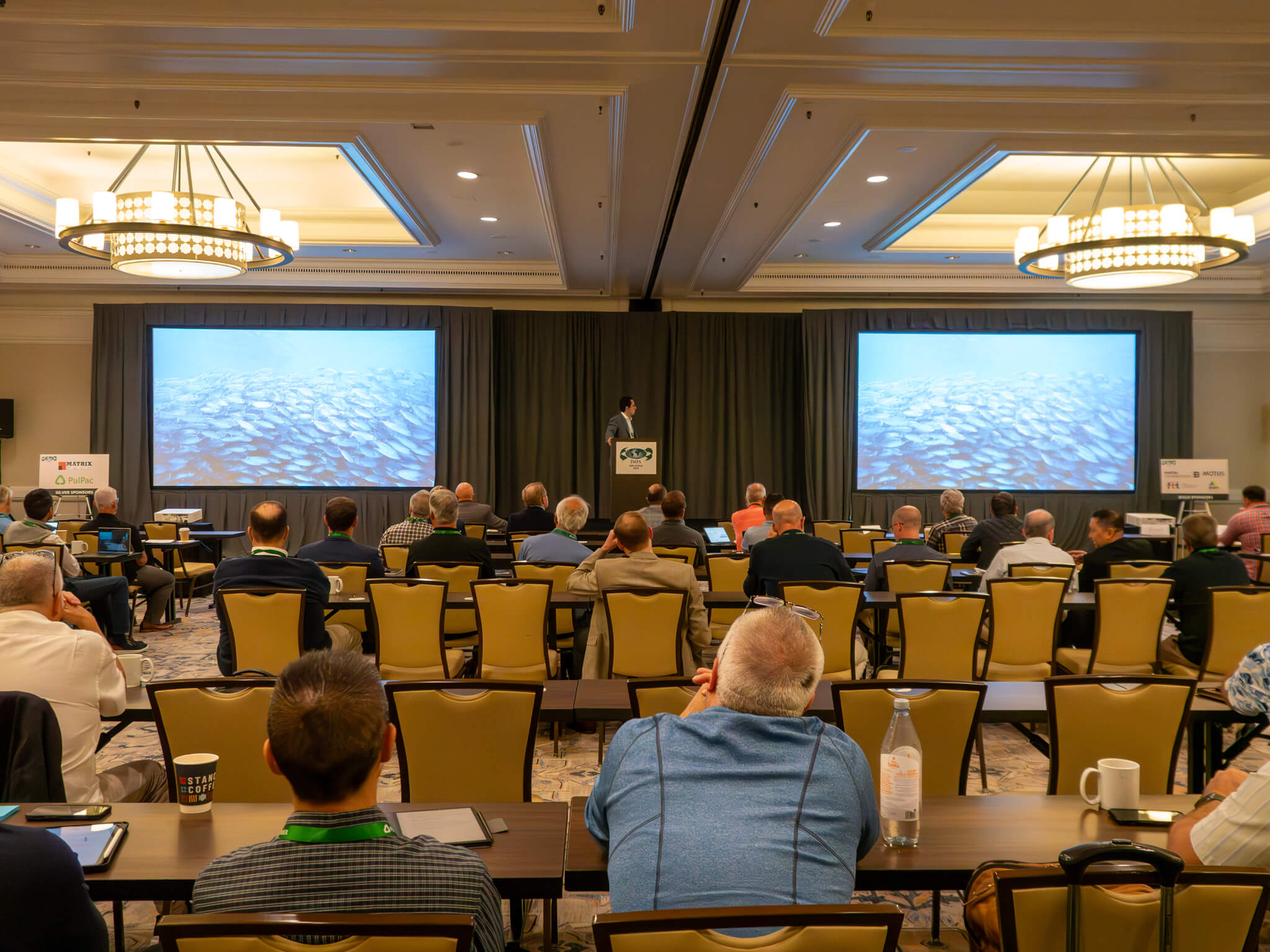
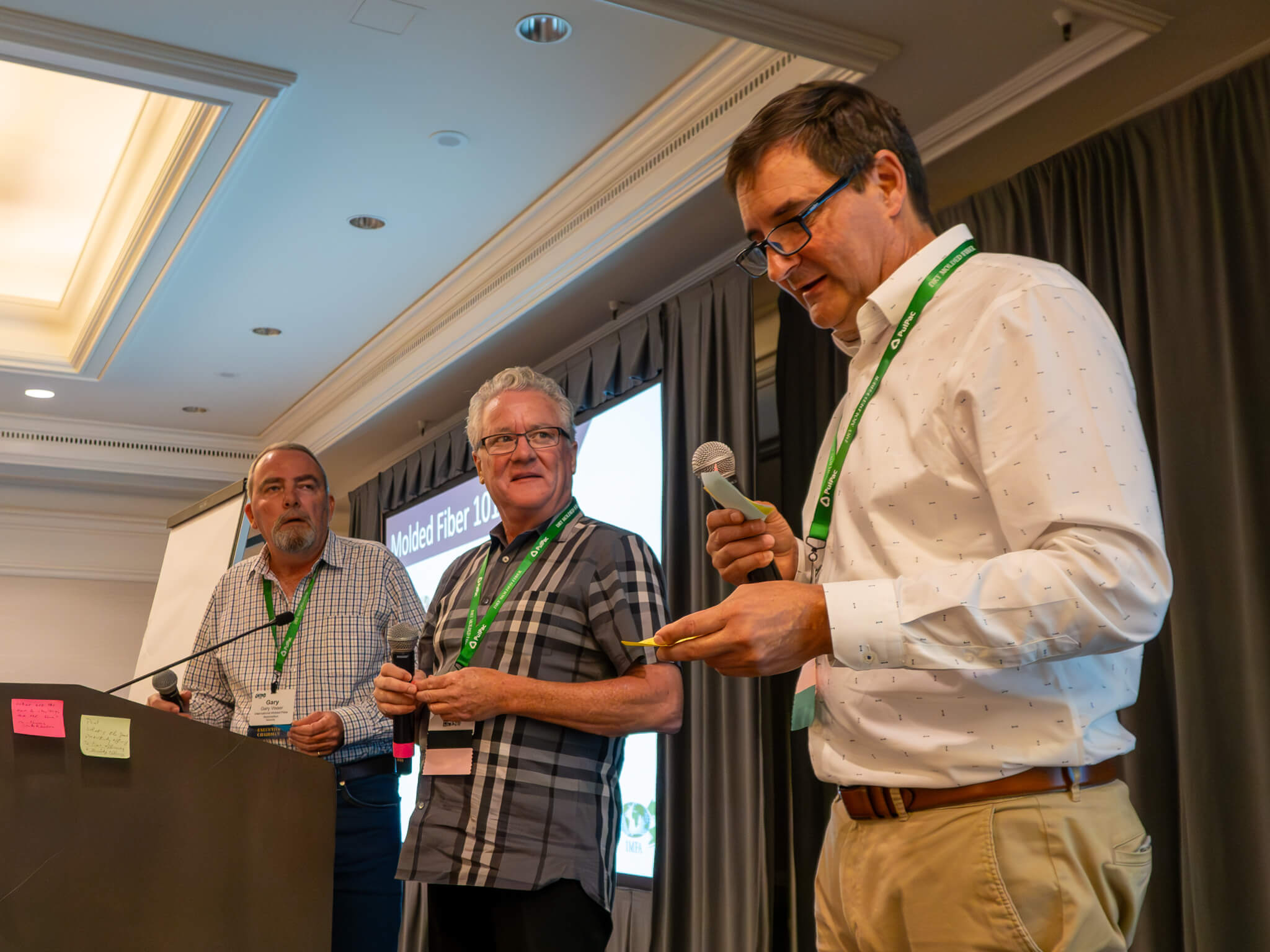
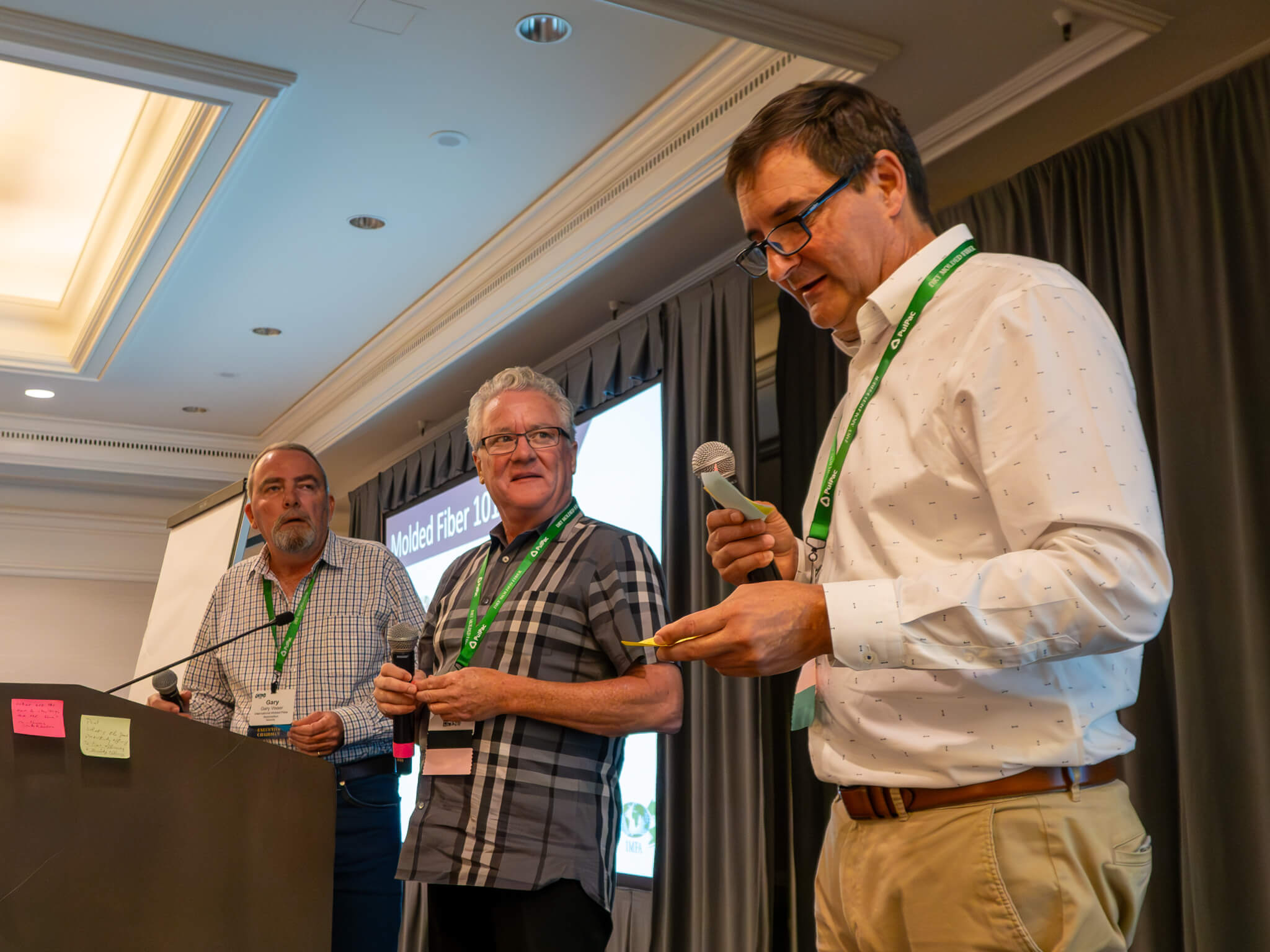
Friday morning kicked off with a presentation from E6PR's Francisco Garcia, who discussed their eco-friendly six-pack ring. He highlighted early challenges in design, performance, and production scalability. Cost is a significant concern to customers due to cheap plastic alternatives, and sustainability is also a key factor. The product initially faced performance issues, including moisture handling and customer interaction, but version 6 successfully passed tests. The rings are recyclable with minimal additives and are used by over 500 customers and 25 companies. High-speed application machines are nearly flawless, underscoring Garcia's belief that "molded fiber is changing the future of packaging."
As always, we couldn’t close out our conference without going back to basics with our Molded Fiber 101 workshop – thank you to Gary Visser, Paul Carter, and Mike Gallant for once again leading this session to help round out our knowledge! Look out for more of the questions we discussed to be added to the Molded Fiber FAQ on our website.
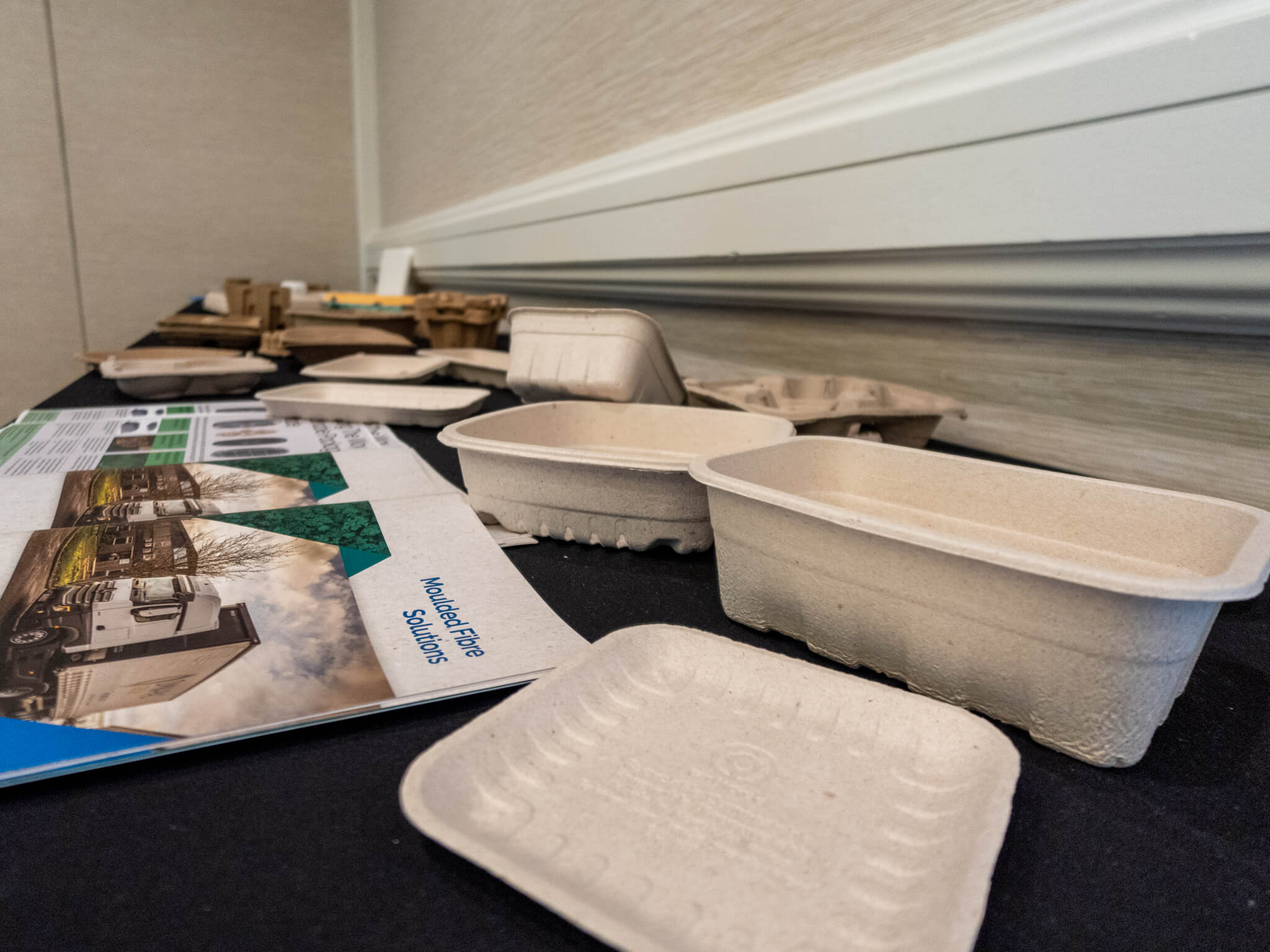
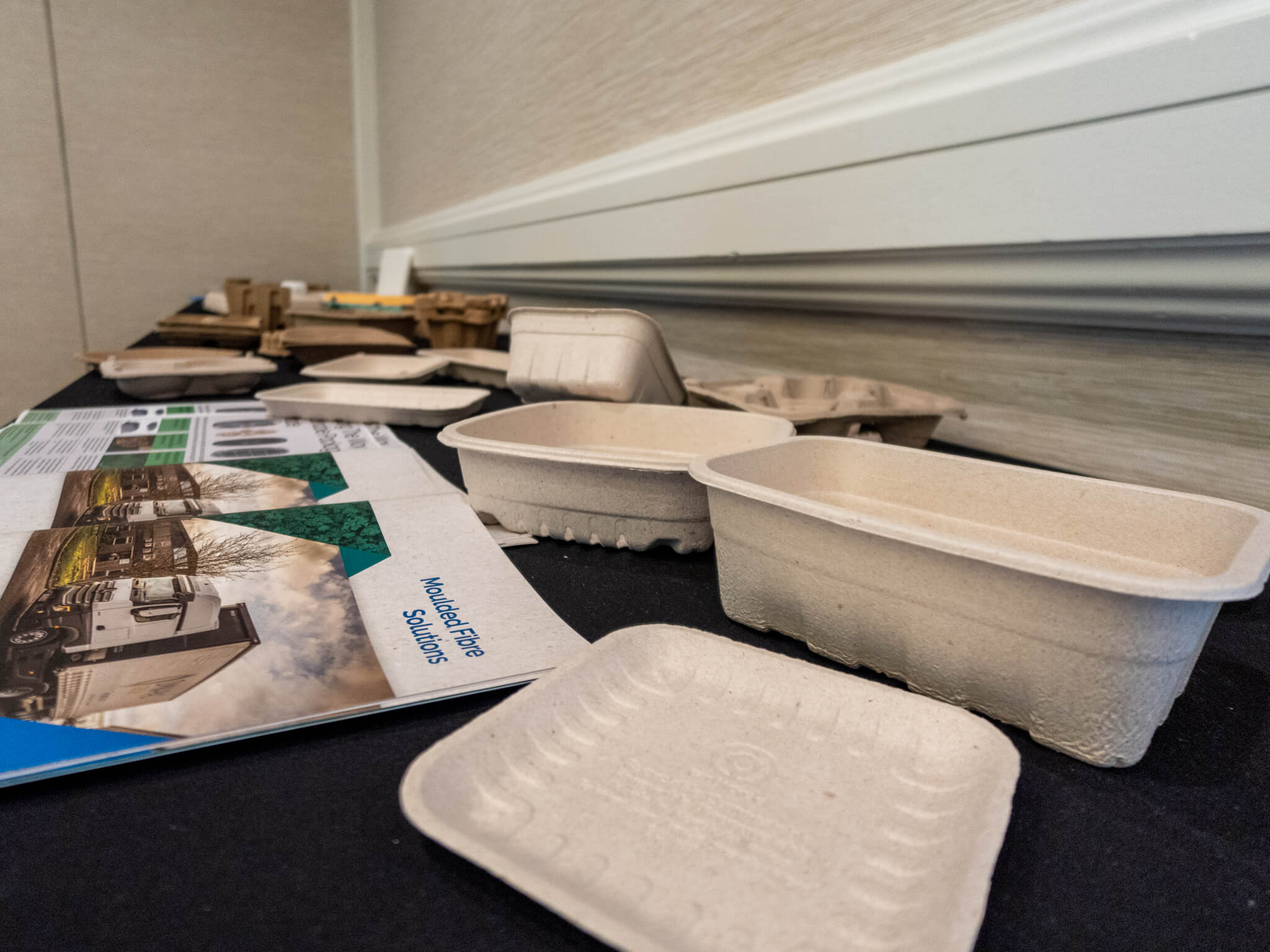
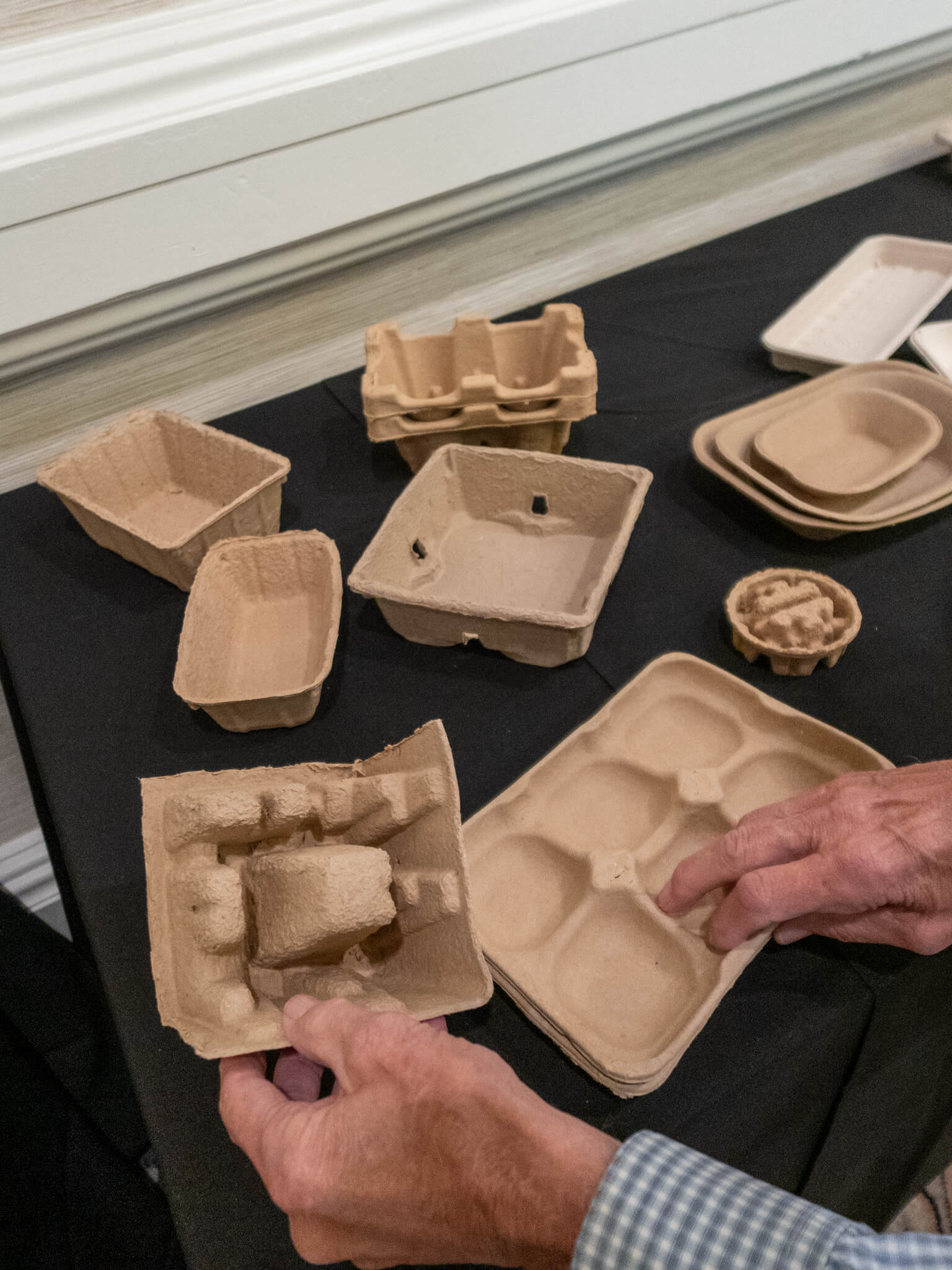
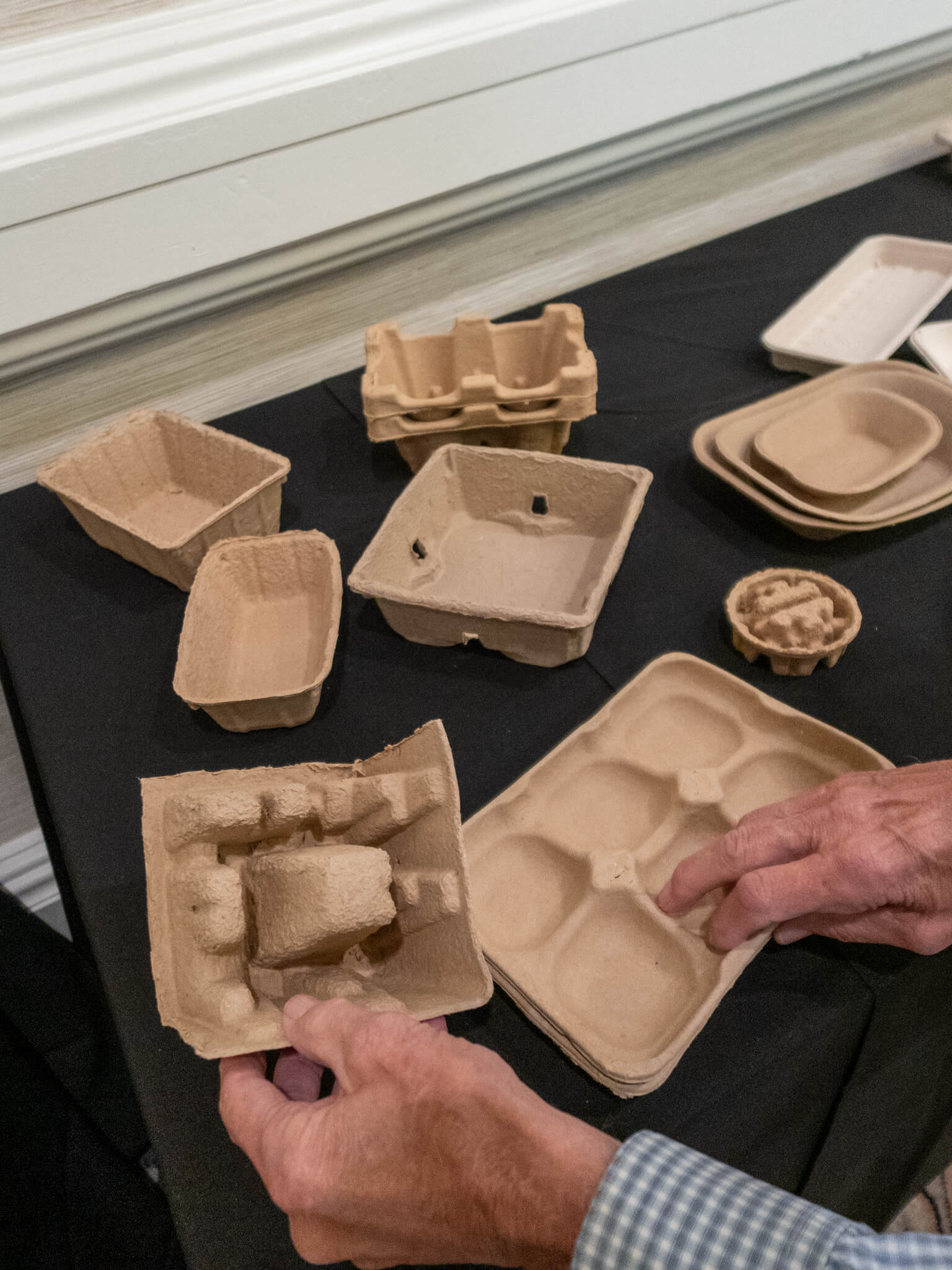
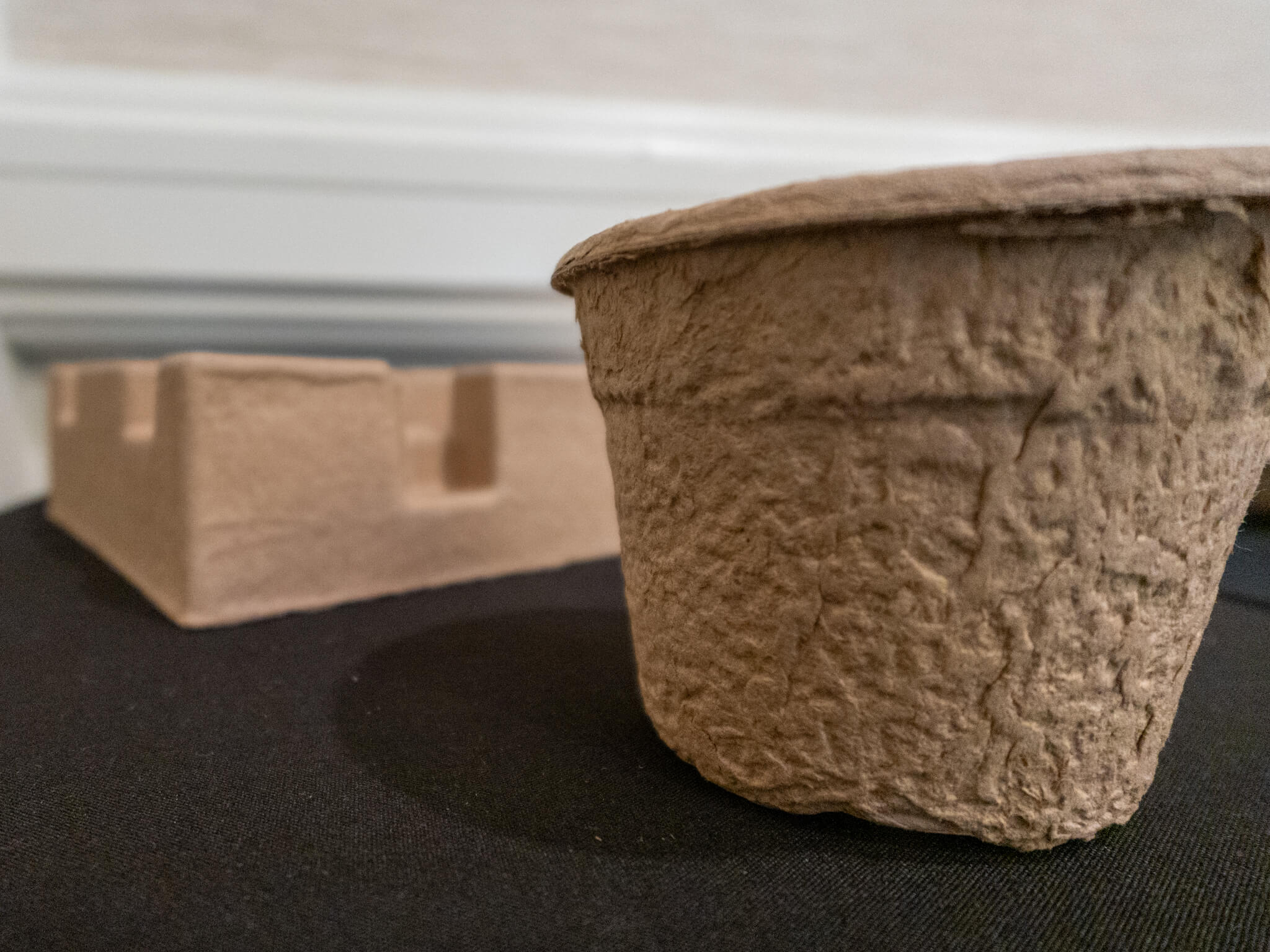
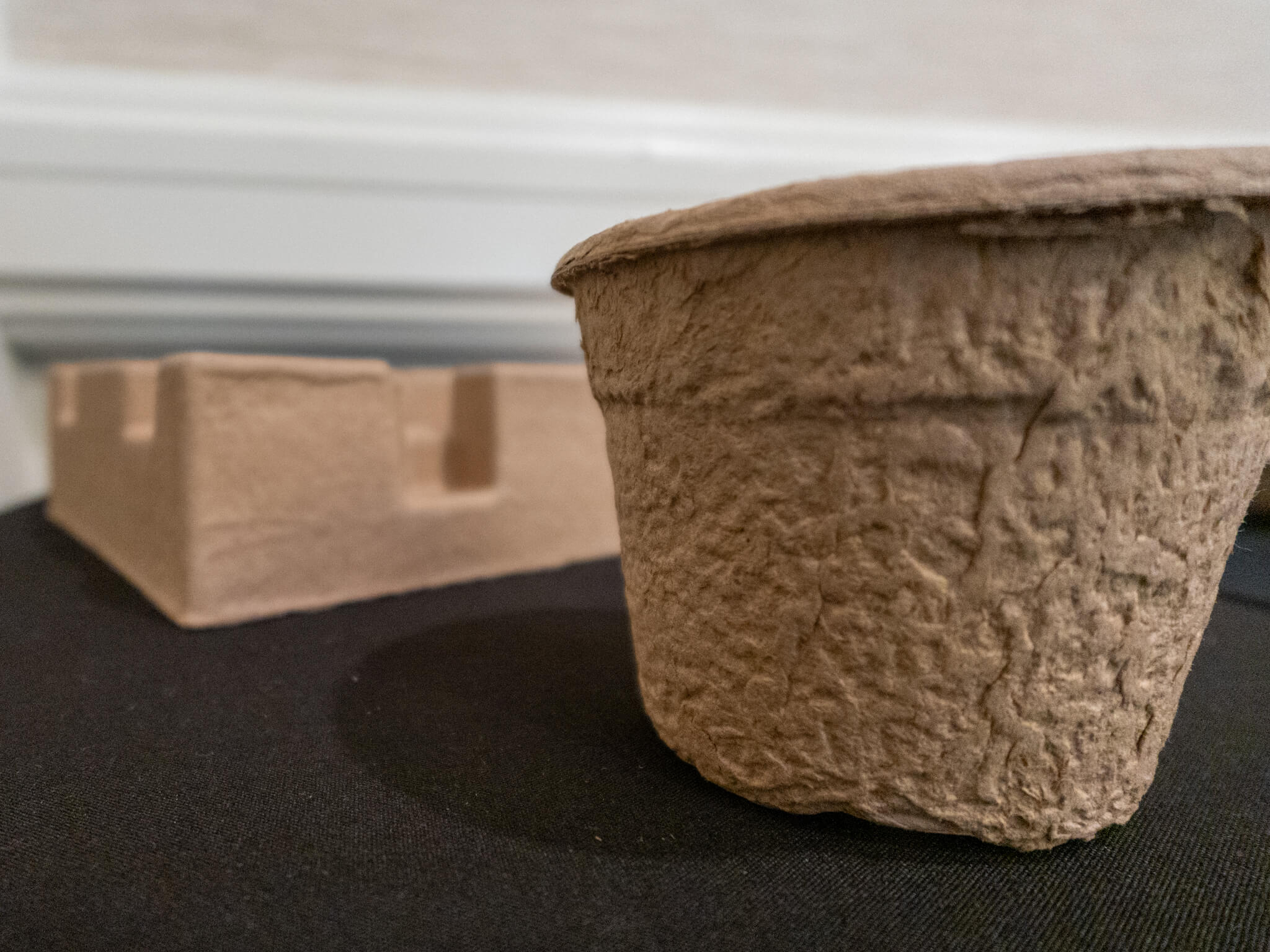
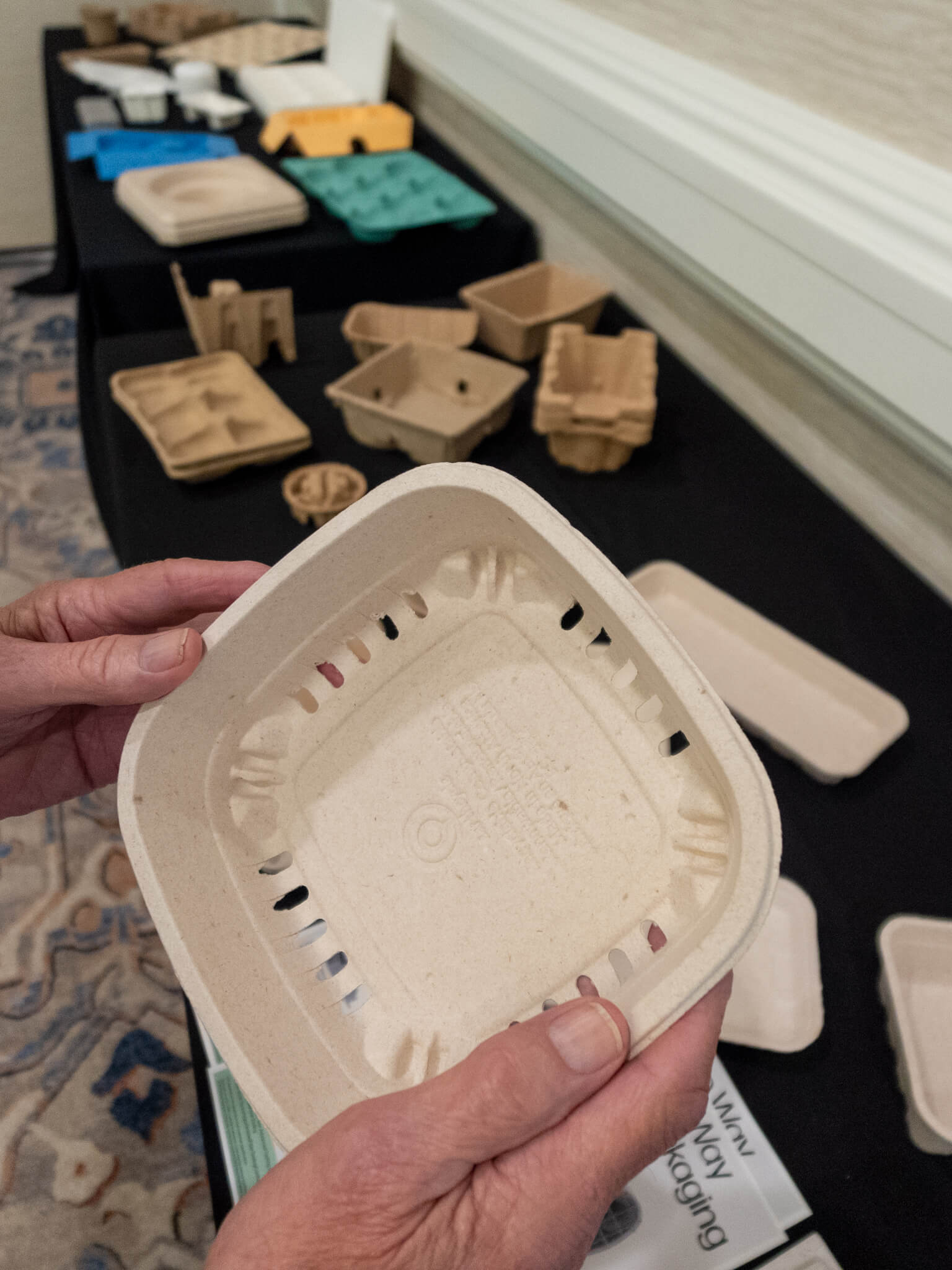
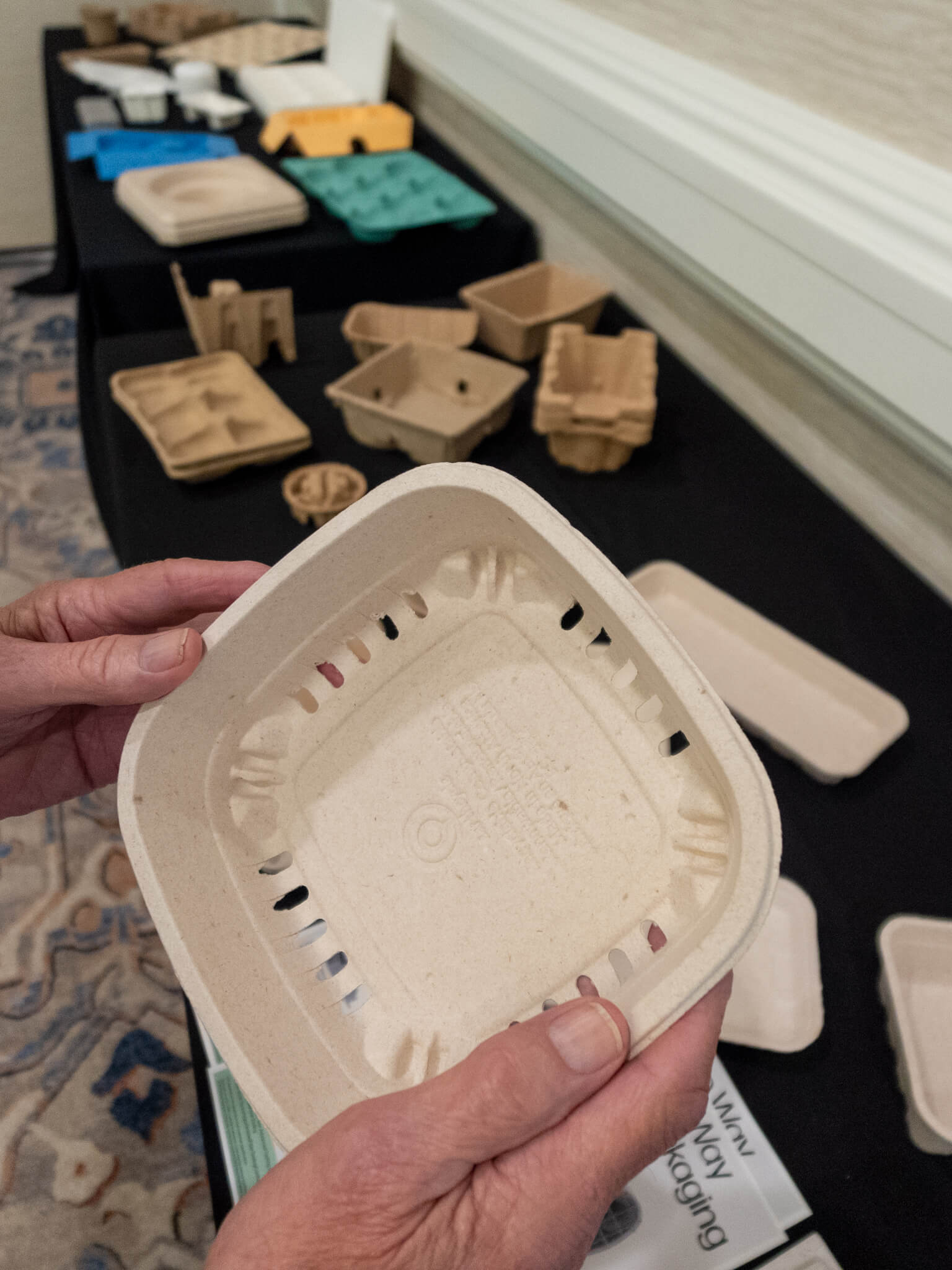
And just like that, our 2024 conference came to a close – we hope everyone found the presentations and networking opportunities as valuable as we did. It's going to be tough to match this week's success in the spring when we gather again, but we're up to the challenge! Registration for Spring 2025 in Miami opens this October – we can't wait to see you there!